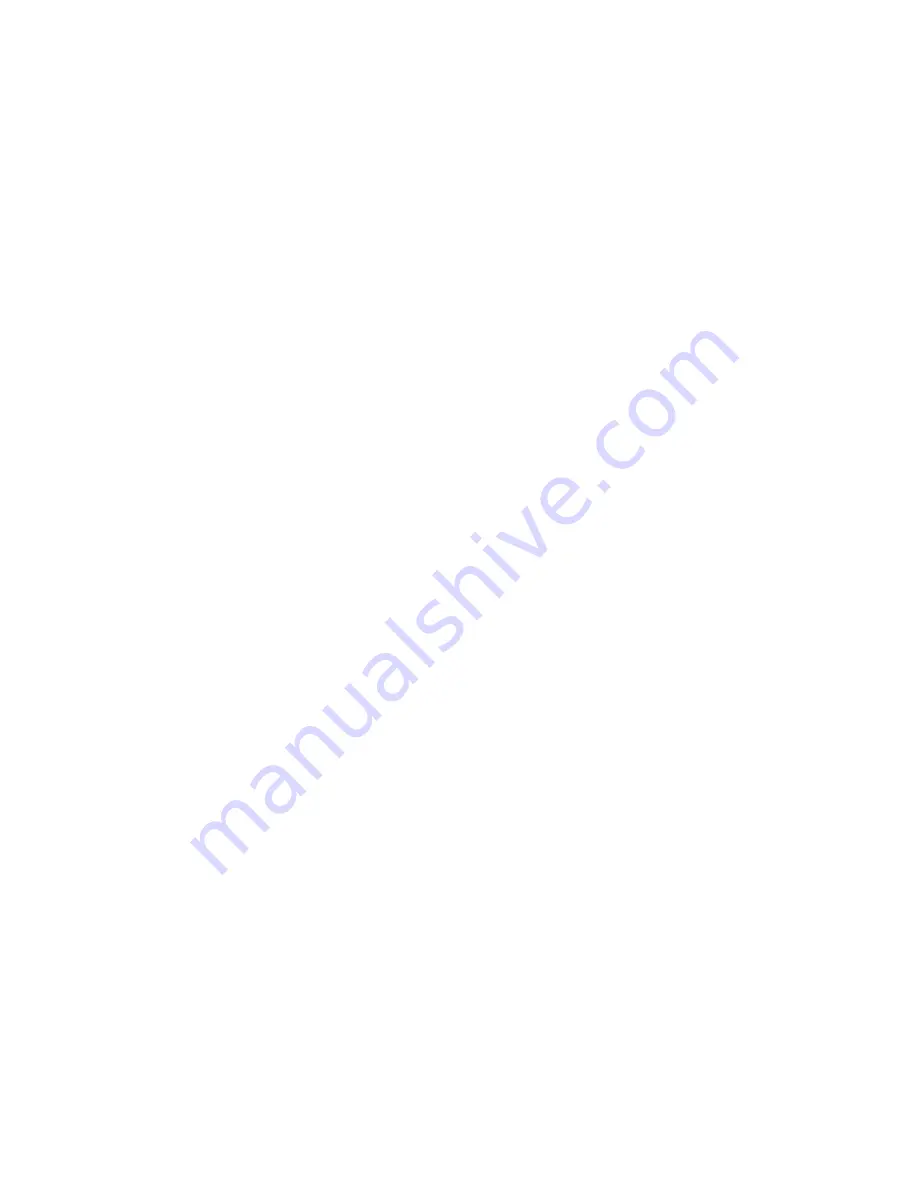
36
Appendix II—Glossary
Arc Force
Related to amps and volts when welding. When stick welding, the Pro Pulse 300 power source produces a
CC, or constant current, output; in other words, the machine holds a constant amperage level, while the voltage varies
according to the arc length, or the distance between the rod and the work surface—longer arc lengths increase voltage and
shorter arc lengths decrease voltage. Increased voltage (a long arc length) keeps the puddle more fluid and the arc more
stable, while decreased voltage (a short arc length) allows you to achieve better metal transfer and a wetter weld quality.
The decrease in arc voltage, however, does pose the risk of extinguishing the rod, which is where arc force comes into
play.
When you set arc force and your arc voltage begins to drop while welding due to a short arc length, arc force increases
your amperage (not you voltage) to give the weld puddle more drive and to keep the rod lit, and burn in (or burn through)
deeper, without snuffing out the arc. Arc force is an adaptive-dynamic process. If, for instance, you select 50% arc force
and set your welding machine to 100 amps, a decrease in arc voltage will cause the amperage to increase automatically up
to 150 amps (as needed and only when you meet certain voltage drop conditions; you will NOT run at 150 amps
continually). Likewise, if you weld at 100 amps and set arc force to 200%, the amperage can increase, under certain
conditions, up to 300 amps. At a 200% setting, drops in arc voltage will cause the amperage to climb faster than if would
if set at 50% arc force. Essentially, with arc force set, you will not see the voltage go up at all if you hold the correct arc
length, and if you hold the arc length too tightly, your amperage will increase, as needed, so the rod stays lit. Of course,
you cannot watch the machine’s display and weld at the same time, but you will hear the difference if/when arc force
kicks in—our inverter welding machines sound unique, especially when arc force kicks in.
Hot Start
A burst of amperage for a very short time—typically less than one (
1
) second to help light the rod, or start the
arc.
When you set hot start, you select a percentage of the welding current. For instance, if you set the machine to weld at
100 amps and then set hot start to 30%, for a fraction of a second the machine puts out 130 amps to help light the rod and
start the arc.
i-Cold Pulse™
Spray arc transfer welding is hot, which causes metal distortion and issues with welding speed. i-Cold
Pulse technology reduces thermal heat, and, in turn, increases the welding speed by 35%. In i-Cold Pulse programs, the
arc becomes more concentrated and intense. The i-Cold Pulse programs preinstalled on the Pro Pulse 300 are especially
designed for production welding where higher travel speeds, less heat input, and less distortion are desired.
P.A.W.™
Stands for Precision Aluminum Welding. Designed for use on very thin aluminum (1 to 2mm thick) with a
standard MIG welding gun. P.A.W. programs offer a short and concentrated welding arc.
Pulsed Process MIG Welding
Pulsed process MIG welding happens in spray arc transfer as opposed to classic MIG
welding, which happens in short arc transfer and sounds like frying bacon. In short arc transfer, the wire literally shortens
out in the puddle, burns back, and then shortens out again. Spray arc welding is much hotter than short arc welding, has
excellent penetration, virtually no spatter, and is typically very quiet (mostly a quiet hissing with an occasional crackle).
This form of welding is so hot that it typically can only be used in flat position, though sometimes in horizontal position
as well. Pulse gives you the option to run the process out of position while retaining the same desirable characteristics of
deep penetration and a virtually spatter-free weld with excellent bead appearance—but does so while enabling you to join
materials of different thicknesses at an increased travel speed, all while lowering heat input and distortion.
Pulsed process MIG welding is different than pulsed process TIG welding. In the MIG process, filler material has to be
added constantly to maintain the welding arc, and this sets the ground rules of the pulse function. When pulsing in TIG
welding mode, you have the ability to adjust peak current, background current, pulse-on time, and pulse frequency. When
pulsing in MIG welding mode, on the other hand, you typically only have the choice of pulse-on and pulse-off. High end
pulsed process MIG welding machines, like the Pro Pulse 300, typically have what is referred to as synergic pulse, which
means the pulse frequency and other welding parameters are preprogrammed into the machine, and change automatically
when you adjust the wire feed speed. The pulse frequency adjusts with the wire feed speed; slower wire feed speeds have
a lower frequency, while higher wire feed speeds have a higher frequency. However, the Pro Pulse 300 also offers peak
pulse (in some programs, under certain conditions, and up to 600 amps).
Because of the pulse frequency, electronic interferences may occur. For this reason,
it is forbidden for people with
PACEMAKERS to use or come near the machine
. During the research and development process at HTP, we
found that some brands/models of auto-darkening welding helmets experience interference issues with the Pro Pulse 300.
Since the frequency changes according to wire speed, we noticed that a wire speed adjustment of +/-20 IPM typically
alleviates the issues. We also noticed that video cameras within close proximity to the Pro Pulse 300, when welding in a
pulse program, show the interference in the recorded picture.
Summary of Contents for Pro Pulse 300
Page 6: ...6 Fig 1...
Page 8: ...8...
Page 31: ...31 Pro Pulse 300 Wiring Diagram...
Page 32: ...32 Pro Pulse 300 Parts Diagram...