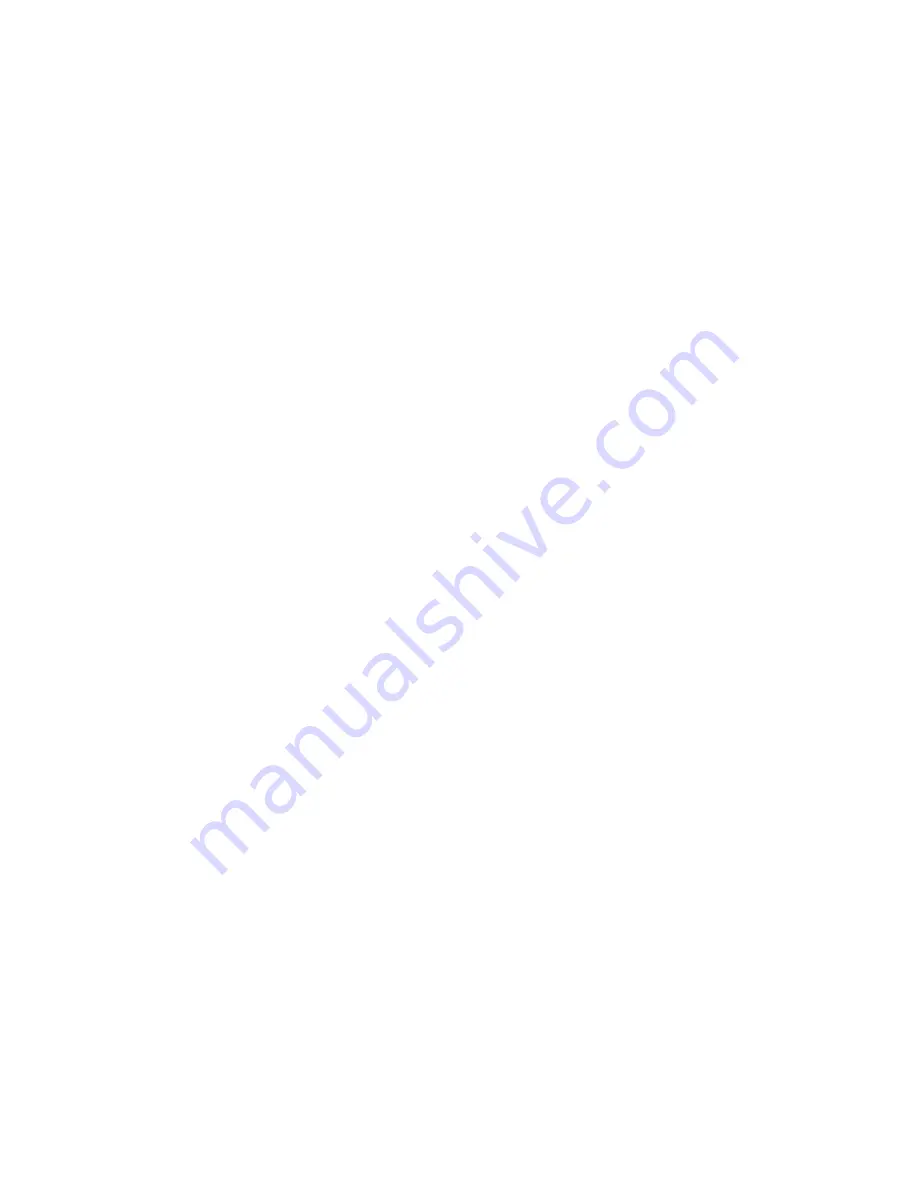
3
Muscle Memory.
Operators who typically MIG weld steel are accustomed to the frying bacon sound the machine
makes when welding and accustomed to holding the gun close to the work piece. Operators may be thrown off by the
sound the Pro Pulse 300 makes when welding, and muscle memory causes the operator to keep the gun too close to
the work piece when welding aluminum, which requires a 3/4” to 1” stick-out.
Old Habits and Frugalness.
For aluminum welding (all spray arc transfer and pulse welding applications), your gas
flow rate must be significantly higher than for classic MIG welding (steel). Flow rates, in fact, must be set upwards of
35 CFH and often as high as 50 CFH. We also see operators running economy Asian import wire or random wound
wire. For aluminum welding, where everything must be just right, a bad roll of wire can make a bad day in aluminum
welding. We recommend using HTP brand wire (made in North America) or Alcotec brand wire (Made in the
U.S.A.). We found that the HTP and Alcotec brand wires work best with the Pro Pulse 300. Spool size matters as
well when welding aluminum; 8” and 12” spools work great and 4” spools do not work at all—the cast is too tight,
and 4” spools are actually designed for spool gun use, NOT for regular MIG welding or push-pull gun use.
Unrealistic Expectations.
No matter what, MIG welds will never look identical to TIG welds. Although, with manual
adjustable double pulse, and when the settings on your machine and the movements of your hand are in perfect
harmony, your MIG welds can look very similar to your TIG welds.
Also, when everything works right, welding aluminum is a lot like welding steel, though there are a few
differences—from gas, to the torch and the torch angle, to the consumables and consumable use. When welding
aluminum, even a skilled welder may go through a few contact tips before finishing a roll of wire; unlike when
welding steel, where some operators can weld an entire 12” spool of wire, or more, through one tip. Aluminum, due
to the nature of aluminum, requires more contact tips. As a novice welder, you may go through five to ten contact tips
in the first few hours, or first day, of welding with the Pro Pulse 300. Typically, air-cooled MIG welding guns expend
a good deal of consumable life in high amperage welding applications. Also air-cooled MIG welding guns typically
use more consumables than water-cooled MIG welding guns.
Birds nesting is not much of an issue with the Pro Pulse 300. However, burn back may occur and must be addressed
immediately—failure to do so will result in EXCESSIVE tip usage! When a burn back occurs, the damaged tip
becomes useless and must be replaced. Furthermore, if you experience burn back, run about 10’ of wire through your
MIG gun to discard any wire damaged by slipping in the drive roll (an effect of burn back into the contact tip).
Material Thickness Ratings Displayed in the Machine.
We designed this feature to give you an idea about settings
(wire speed and voltage). The ratings displayed, generally speaking, are designed for straight line, push or pull
(depending on the application) welds made at a rather fast travel speed (to reduce heat input into and distortion of the
material you are welding on) and without any gun manipulation (no weaving, swirly motion, etc.). However,
depending on the joint configuration (butt, lap, or T-joint) and on the welding position (flat, horizontal, vertical up or
down, and overhead), you need to adjust the synergic setting accordingly.
Now, with a better understanding of what you will experience when welding with the Pro Pulse 300, enjoy finding out all
of the details by reading the rest of the manual and watching the videos.
If you already read through the entire manual once, and you simply want to locate essential information quickly, please
look for our
Pro Tips: in bold, italicized, blue print
.
Summary of Contents for Pro Pulse 300
Page 6: ...6 Fig 1...
Page 8: ...8...
Page 31: ...31 Pro Pulse 300 Wiring Diagram...
Page 32: ...32 Pro Pulse 300 Parts Diagram...