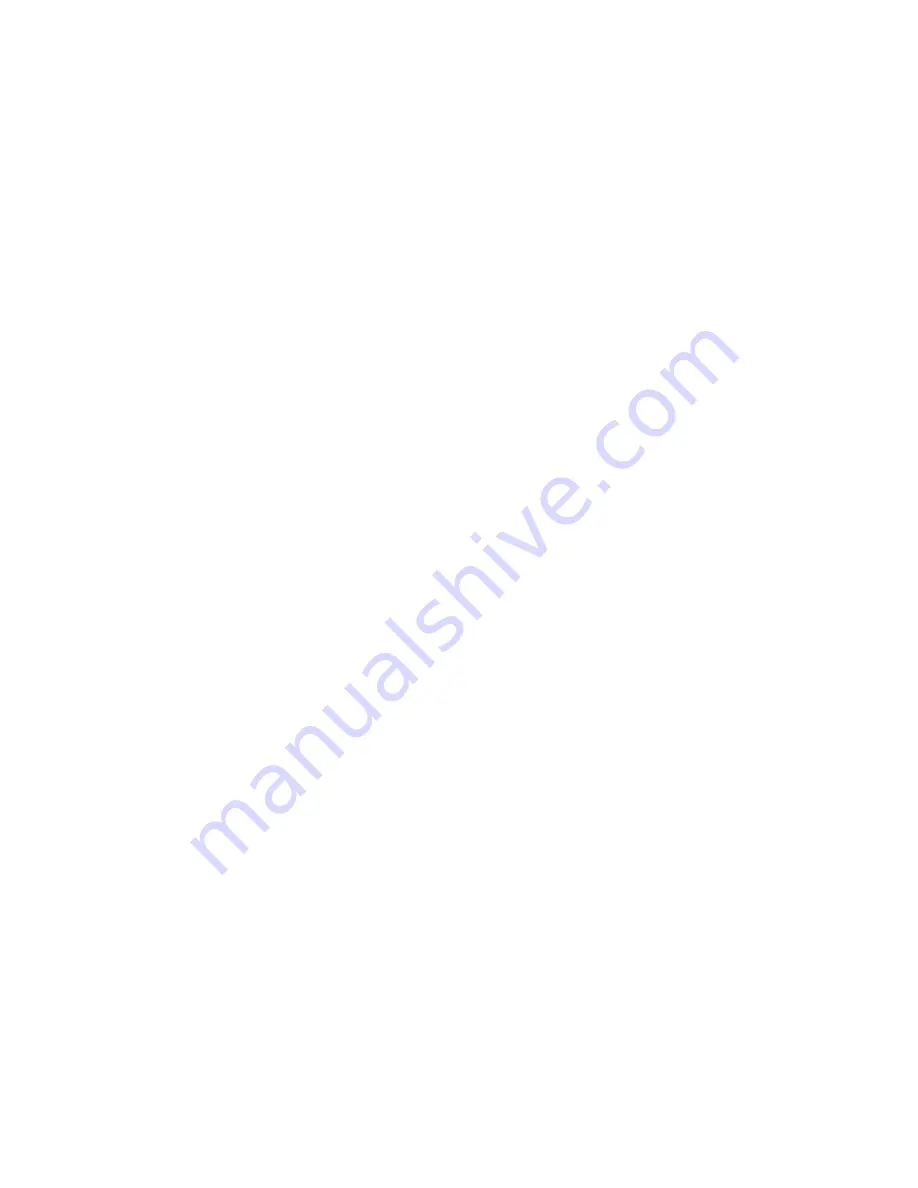
13
The Programs—Overview
The Pro Pulse 300 offers 32 synergic programs, both with and without pulse, as well as a manual mode. The manual
mode operates just like a classic MIG machine with wire speed adjustment in IPM, from 55 to 709, and voltage
adjustment, from 13.0 to 35.0. Manual mode can be used for wire types not included in the synergic programs list (e.g.,
cast iron wire). Please obtain the correct wire speed, voltage, and CTWD settings from your wire distributor or
manufacturer.
The synergic, non-pulse programs sound very similar to classic MIG welding. These programs offer inductance
adjustments, which makes the arc crisp or soft. The ability to change arc characteristics is a desired feature, and these
features are not offered on classic transformer-based machines. The pulse programs are also synergic, but they sound
different than classic MIG welding; the sound when pulse welding changes based on the material thickness (wire feed
speed). These programs offer a slop down function, which can be used to fill craters at the end of aluminum welds.
Both pulse and non-pulse programs offer adjustments in start-speed (wire run-in), speed and duration, as well as burn
back and pinch. The start-speed feature offers the ability to set a crisp arc ignition without a “machine gun” start. Burn
back determines how long the wire sticks out of the contact tip when you complete a weld; the lower the burn back
number, the longer the stick out
(ATTENTION: High numbers can cause the wire to burn back into the contact tip, which
destroys the contact tip)
. Pinch refer s to the shape of the wire; when MIG welding (classic), a ball usually forms at
the end of the wire upon completion of the weld. Then, you typically trim off the ball with a pair of pliers. However, the
Pro Pulse 300 can trim off the ball for you electrically by setting the pinch. The higher the pinch number, the more the
wire gets trimmed electrically
(ATTENTION: The number required will change based on the type and the diameter of the
wire used. Also, numbers higher than 75 can cause burn back into the contact tip, which destroys the contact tip,
when welding with aluminum)
.
Regardless of whether you run a synergic or a pulsed program, you can also adjust the pre- and post-flow gas. Pre-flow
ensures shielding gas is already in place when you strike an arc, which minimizes or eliminates porosity, discoloration,
and/or peppering. Post-flow shields hot, glowing wire from contamination through ambient air and also protects the weld
(as long as you keep the torch in place for the post-flow duration after you complete the weld). This function is extremely
helpful when welding stainless steel and aluminum.
Welding Aluminum with the Pro Pulse 300
(Hot Start and Crater Fill Functions Explained)
The Pro Pulse 300 offers several different programs for welding aluminum. All of the programs are designed to get the
best results using 100% Argon gas. Helium mixtures are NOT recommended. Welding aluminum requires the use of a U-
shaped drive roll, and the tension of the wire feed unit must be properly adjusted. Aluminum wire requires very little
tension. A setting just at, or even much less than, 1 will be absolutely sufficient. If you select a higher tension, wire feed
issues, such as deformation of the wire, wire getting stuck in the contact tip, burn backs, and birds nesting, will arise.
Aluminum shavings will also be deposited in and clog the liner; you will then need to replace the liner.
The use of CuCrZr contact tips is strongly recommended when welding aluminum with a water-cooled MIG welding gun
and ABSOLUTELY necessary when welding aluminum with an air-cooled MIG welding gun, a push-pull gun, or a spool
gun. The contact tips used can be size-on-size when welding at a low amperage with low duty-cycle, but needs to
be .005” larger than normal (e.g., .040” tips for .035” wire) when welding at a high amperage. Regular copper tips are not
designed to withstand the extreme heat of pulsed spray arc aluminum MIG welding.
Aluminum wire should be fed through a designated gun if cross-contamination is a concern. Generally speaking, 5356
and 5554 alloy aluminum wire, due to their stiffer nature, feed better than 4043 alloy aluminum wire, but large diameter
wire also feeds better than small diameter wire. A graphite liner is highly recommended for all aluminum welding
applications. If a graphite liner is unavailable, a nylon or Teflon liner can be used in place of a graphite liner; however,
you must expect reduced or severely reduced performance when not using a graphite liner. Given all of these variables,
we offer 8’, 10’, and 12’ MIG welding guns with graphite liners.
Flush tips or slightly recessed tips (tip holders) can be used for aluminum welding or stainless steel welding. To improve
shielding gas coverage, we suggest the use of a cylindrical nozzle.
Summary of Contents for Pro Pulse 300
Page 6: ...6 Fig 1...
Page 8: ...8...
Page 31: ...31 Pro Pulse 300 Wiring Diagram...
Page 32: ...32 Pro Pulse 300 Parts Diagram...