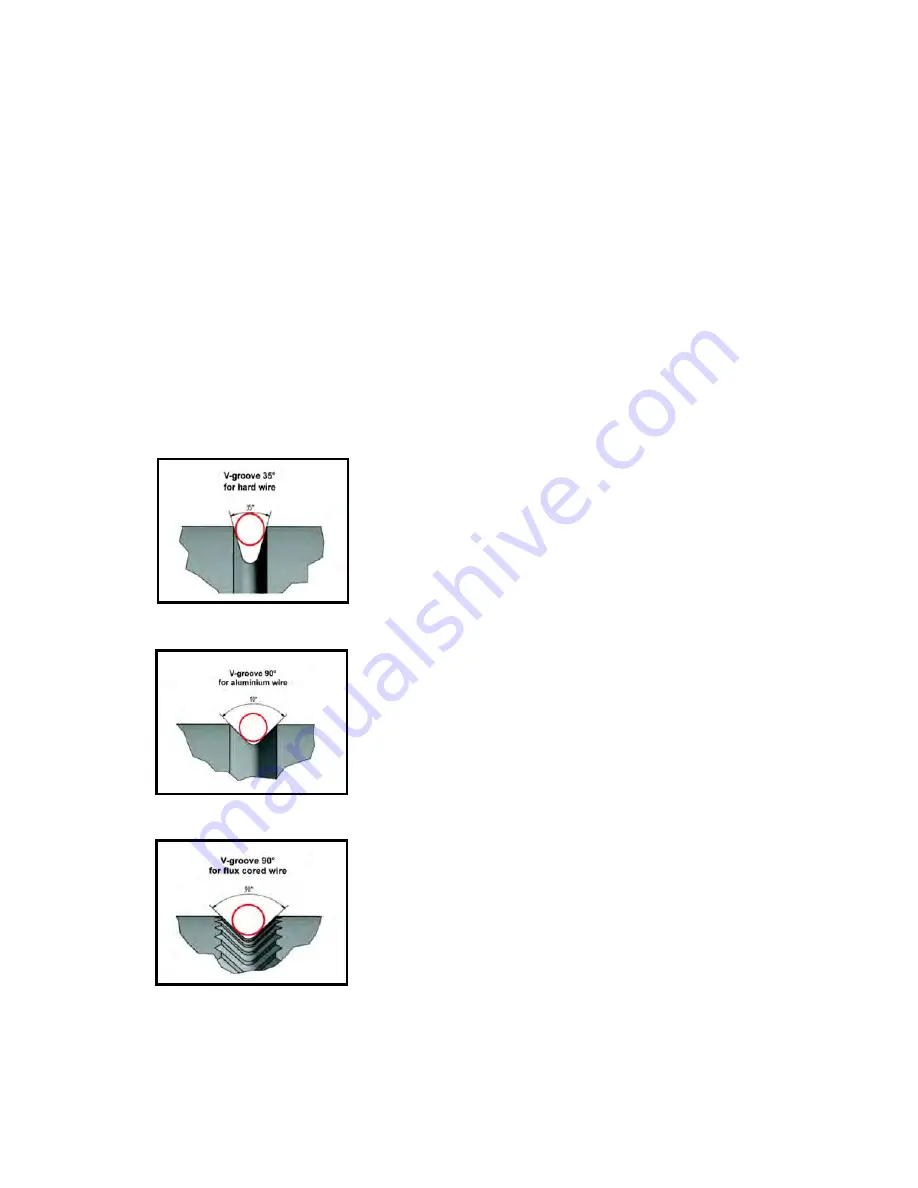
19
Use drive rolls with a groove that matches the wire
diameter chosen. There are different sizes and
shapes of drive rolls. For .023”, .024”, and .025”
diameter wire, use a drive roll marked 0.6; for .030”
wire, use a drive roll marked 0.8; for .035” wire, use
a drive roll marked 0.9 or 1.0; for .045”, .047”, and
3/64” wire, use a drive roll marked 1.2. (
Note:
Some
drive rolls are reversible, meaning there are two
different size grooves on the same drive roll—
simply flip the drive roll so that the marking for the
size you need faces you.)
Also, different materials require different drive roll
shapes. For instance, mild steel wire, stainless steel
wire, and silicon bronze wire typically use a
standard V-shaped drive roll (
Fig. 17
). Softer
aluminum wire uses a U-shaped, or V90 degree,
drive roll (
Fig. 18
). Flux-cored wire, whether used
with or without gas, and most hard surfacing wires,
require the use of a knurled drive roll—the little
teeth provide extra traction on these wires (
Fig. 19
).
Fig. 17
Fig. 18
Fig. 19
Use the proper wire tension. When welding with
mild steel or stainless steel, feed tension is important
but a little forgiving. Generally, the wire tension
should be set around 3. If that does not give you
good results, there is most likely a problem
unrelated to wire tension present. For example, a
bad contact tip, a bad liner, a defective welding gun,
etc. can cause the wire to not feed smoothly.
When welding flux-cored wire, then tension should
be set lower than 2. If flux-cored wire is being fed
through a wire feeder with too much tension, the
tubular flux-cored wire will deform and its shape
will change; the wire will become oblong and too
big to fit through the contact tip. Improper electrical
contact, poor weld quality, burned contact tips, and
other issues will follow. Also, over-tightened drive
roll tension and deformed wire will cause metal
particles to separate from the wire. Those particles
will, over time (sometimes a very short time, such as
after welding only several pounds of wire), deposit
themselves in the liner as the wire is transported
through the gun, ultimately clogging the liner and
rendering it useless.
When welding aluminum, the drive roll tension
should be less than, or much less than, 1! Please
make sure that both pressure adjusters are backed
way off. This minimizes the chances of the wire
birds nesting (
Note:
If there is burn back or another
issue that jams the wire feed, the setting should be
so low that the drive rolls slip on the wire rather than
continue to feed—continued feeding results in birds
nesting).
Use the correct polarity. Most MIG wires are welded
DCEP (electrode positive), and there are very few
exceptions to this rule (gasless flux-cored wire and
some specialty hard-surfacing wires are exceptions).
If in doubt, please consult the data sheet that came
with the wire, the box the wire came in, or contact
the distributor you purchased the wire from.
Use the correct welding gun. For welding stainless
steel wire or aluminum wire, a cylindrical gas nozzle
provides better gas coverage.
If welding in synergic or pulse mode, select the
correct material thickness (reduce the material
thickness if you need to fill big gaps or if the
material you are welding is very hot) and observe
the wire manufacturer’s recommended CTDW.
Summary of Contents for Pro Pulse 300
Page 6: ...6 Fig 1...
Page 8: ...8...
Page 31: ...31 Pro Pulse 300 Wiring Diagram...
Page 32: ...32 Pro Pulse 300 Parts Diagram...