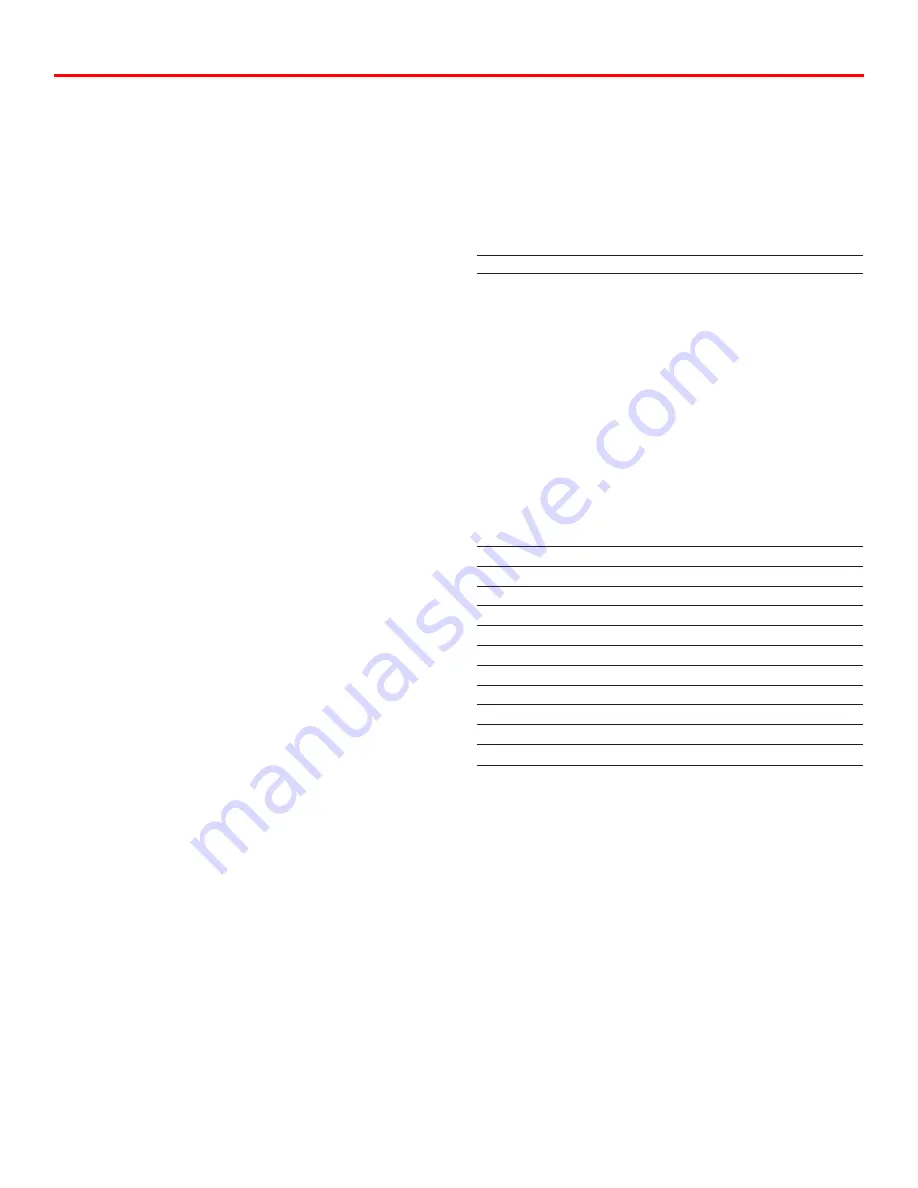
WELDING WIRE
HTP has a wide variety of welding wire available. For
autobody repair, we strongly recommend the following wires:
Application
Part #
Description
Steel
21023
.023" E70S-6 Steel wire
Aluminum
40230
.030" 5356 Alloy Aluminum Wire
We are typically finding body panels being made from 22 gauge
(.0299" thick), 24 gauge (.0239" thick) and 26 gauge (.0179"
thick) steel. When welding this thin metal, the secret to
minimizing distortion and burn-through is by using a wire
which will require the least amount of heat to melt. This would
be the thinnest wire available, .023" diameter in steel and .030"
diameter in aluminum.
For muffler work and general repair welding, we are generally
working on thicker materials. We therefore recommend using
part #21030, .030" steel wire. This wire will give greater
penetration and less feeding problems.
Application
Part #
Description
Steel (30 ga -1/8")
21023
.023" E70S-6 Steel Wire
Steel (16 ga - 1/4")
21030
.030" E70S-6 Steel Wire
Steel (14 ga -1/2")
21035
.035" E70S-6 Steel Wire
Aluminum (24 ga -1/8")
40230
.030" 5356 Alloy Aluminum Wire
Aluminum (16 ga - 1/4")
40235
.035" 5356 Alloy Aluminum Wire
Stainless Steel (24 ga -1/8")
38223
.023" Stainless Steel Wire
Stainless Steel (18 ga -1/4")
38230
.030" Stainless Steel Wire
Cast Iron
50235
.035" Cast Iron Wire
Brazing
50230
.030" Silicon Bronze Wire
Steel W/O Gas (16 ga -1/4") 61030
.030" Flux cored Wire
Steel W/O Gas (16 ga -1/4") 61035
.035" Flux Cored Wire
For other applications, use the following chart as a guide:
All HTP steel welding wires are AWS grade E70S-6. This is a
high quality welding wire with additives to reduce spatter and
offer better wetting characteristics on rusty material. Also, this
is the only grade of welding wire that is compatible with the
High Strength Low Alloy steels found in today’s unibody
vehicles.
20
MONTHLY MAINTENANCE
Your HTP MTS 160 is a very hardworking piece of equipment
and is very simple to maintain. However, your HTP MTS 160
is more complicated than other types of welding equipment.
It is very important that these simple maintenance procedures
be followed to keep your welder operating trouble free.
1.
Wire Drive System
– The guide tube and inlet wire guide
should be check periodically to ensure that they are in correct
alignment with the drive rolls. Misalignment will result in
the copper plating of the wire being rubbed off. This copper
dust will be carried into the liner resulting in increased
friction causing wire feed problems.
2.
Welding Cable
– You should not allow heavy equipment to
run over the welding cable. Avoid pulling the machine by
the cable.
Do not pull the welding cable over sharp edges.
3. Transformer and Internal Components
Your MIG Welder is equipped with a thermoswitch to protect
the internal components of you welder should the duty cycle
be exceeded. The thermoswitch is placed in the low voltage
circuit, so that when the duty cycle is exceeded, the main
relay will not operate, preventing power from going to the
main transformer. The indicator light will remain on, the
wire will not feed, and on the machines equipped with
cooling fans, the fans will remain on. When the machine
cools down (approximately 20 minutes) the thermoswitch
will automatically reset itself and the machine will be ready
for use.
To keep the cooling system of your welder operating at peak
performance, it is necessary to remove the side panel and
blow this area out with dry, compressed air. This will
remove dirt and dust from the internal components.
Summary of Contents for MTS 160
Page 21: ...21 Wiring Diagram MTS 160...
Page 22: ...Parts Breakdown MTS 160 22...