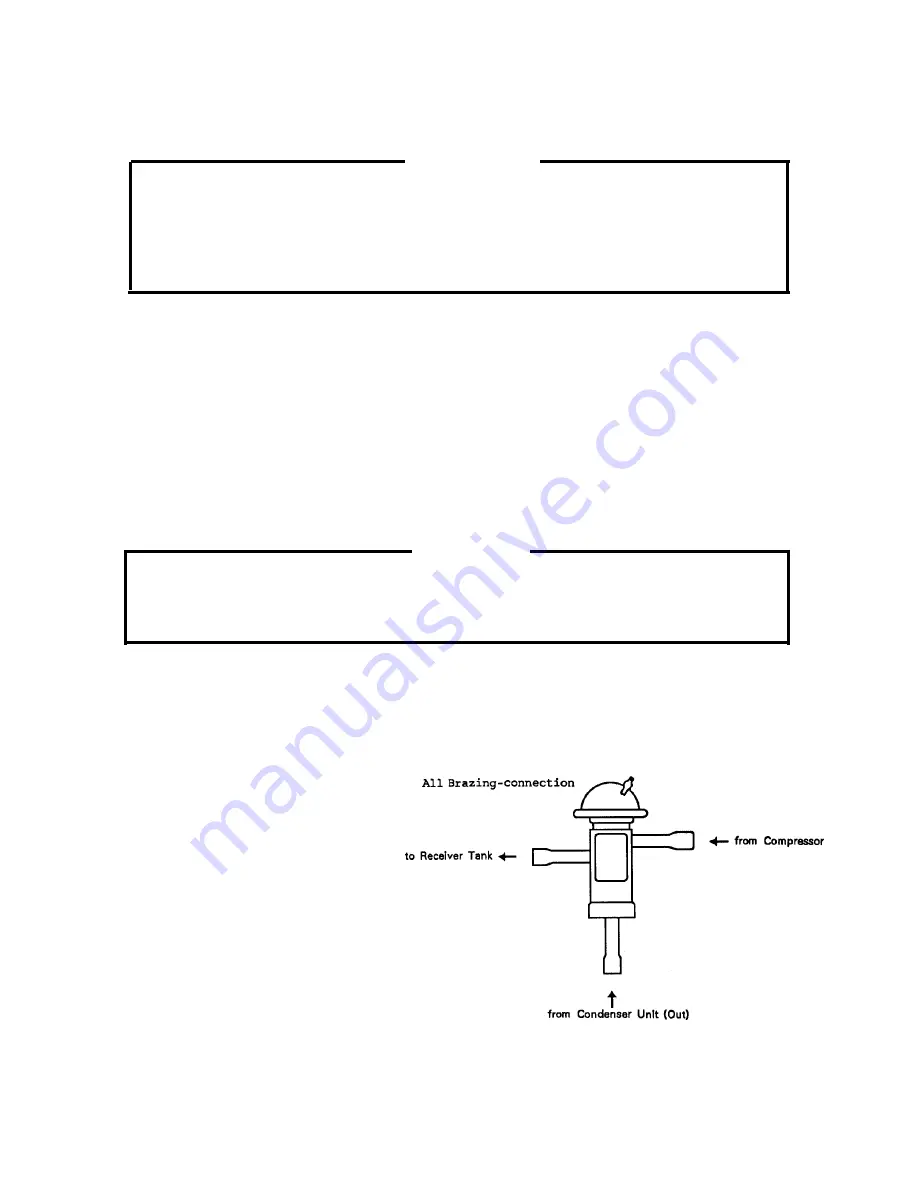
65
7. REMOVAL AND REPLACEMENT OF CONDENSING PRESSURE
REGULATOR (C.P.R.) - REMOTE AIR-COOLED MODELS ONLY
IMPORTANT
Always install a new Drier every time the sealed refrigeration system is
opened. Do not replace the Drier until after all other repairs or replacements
have been made.
1) Turn off the power supply.
2) Remove the panels from the remote condenser unit.
3) Recover the refrigerant and store it in an approved container.
4) Remove the C.P.R. using brazing equipment.
6) Braze the new C.P.R. with nitrogen gas flowing at the pressure of 3 - 4 PSIG.
WARNING
Always protect the valve body by using a damp cloth to prevent the valve
from overheating. Do not braze with the valve body exceeding 250°F.
7) Install the new Drier in the icemaker.
8) Check for leaks using nitrogen gas (140 PSIG) and soap bubbles.
9) Evacuate the system. Charge
it with refrigerant. See the
label on the Control Box in
the icemaker.
9) Replace the panels in their
correct position.
10) Turn on the power supply
Summary of Contents for F-2000MLF
Page 14: ...14 2 CONDENSER UNIT URC 20F...
Page 16: ...16 II GENERAL INFORMATION 1 CONSTRUCTION F 2000MLF C...
Page 17: ...17 F 2000MRF3 C F 2000MRF C...
Page 18: ...18 F 2000MWF C...
Page 20: ...20 F 2000MWF F 2000MRF C...
Page 21: ...21 F 2000MLF C...
Page 22: ...22 III TECHNICAL INFORMATION 1 WATER CIRCUIT AND REFRIGERATION CIRCUIT F 2000MLF C...
Page 23: ...23 F 2000MRF3 C...
Page 24: ...24 F 2000MWF C...
Page 25: ...25 2 WIRING DIAGRAMS F 2000MLF C...
Page 26: ...26 F 2000MRF3 C...
Page 27: ...27 F 2000MWF C...
Page 28: ...28 F 2000MRF C...
Page 30: ...30 b When Reservoir has been filled Gear Motor starts immediately...
Page 33: ...33 e Low Water Except Water cooled Model where Compressor will operate intermittently...
Page 39: ...39...
Page 69: ...69...