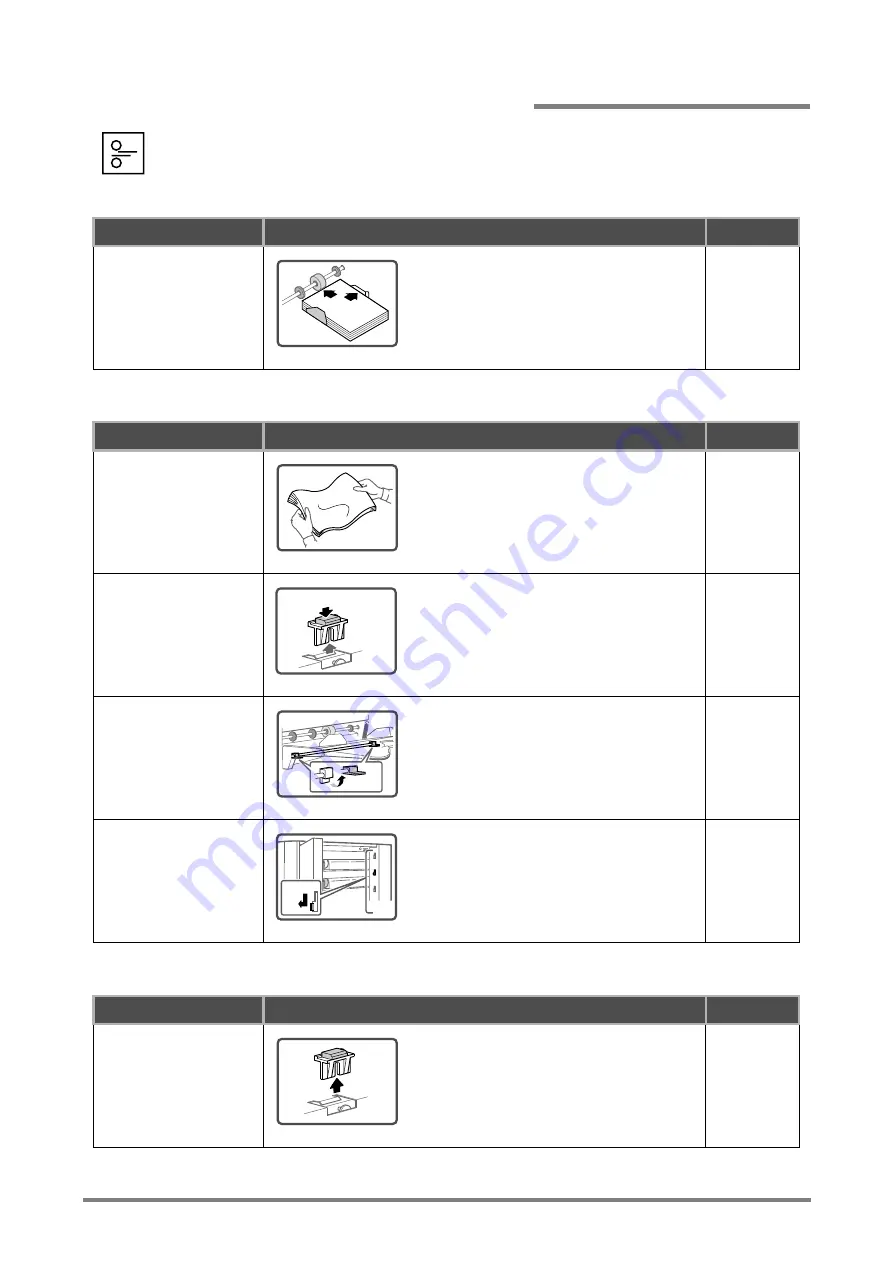
27
Double Feed: Two or more sheets are fed at a time.
The sheets are not loaded in the bins correctly:
If the collating error occurs frequently even though the sheets are loaded correctly:
If double feeding occurs after you have cleaned the friction pad:
Check
Causes and Remedies
Page
Check whether the
sheets are loaded cor-
rectly.
Load the sheets correctly.
Page 5,6
Check
Causes and Remedies
Page
Check whether the
sheets are held together
by static electricity.
Fan the sheets completely or let the sheets sit
for a while before collating them.
Page 5
Check whether the fric-
tion pad is stained with
ink.
Clean the friction pad.
Page 37
Check the setting of the
feed pressure adjusting
block under each bin.
If a block is set to the strong position, reset it to
the normal position.
-
Check the setting of the
pad pressure adjusting
lever on the left side of
the collator.
Open the transport door and check the setting
of the pad pressure adjusting lever.
If the lever is set to the normal (upper) position,
reset it to the strong (lower) position.
-
Check
Causes and Remedies
Page
Check whether the sur-
face of the friction pad is
worn.
Replace the friction pad.
Page 37
2109640101A1
2109640101B1
2109640101C1
Clean
2109640101D1
Normal
2109640101E1
Strong
2109640101F1
Error Icon Appears: Double Feed