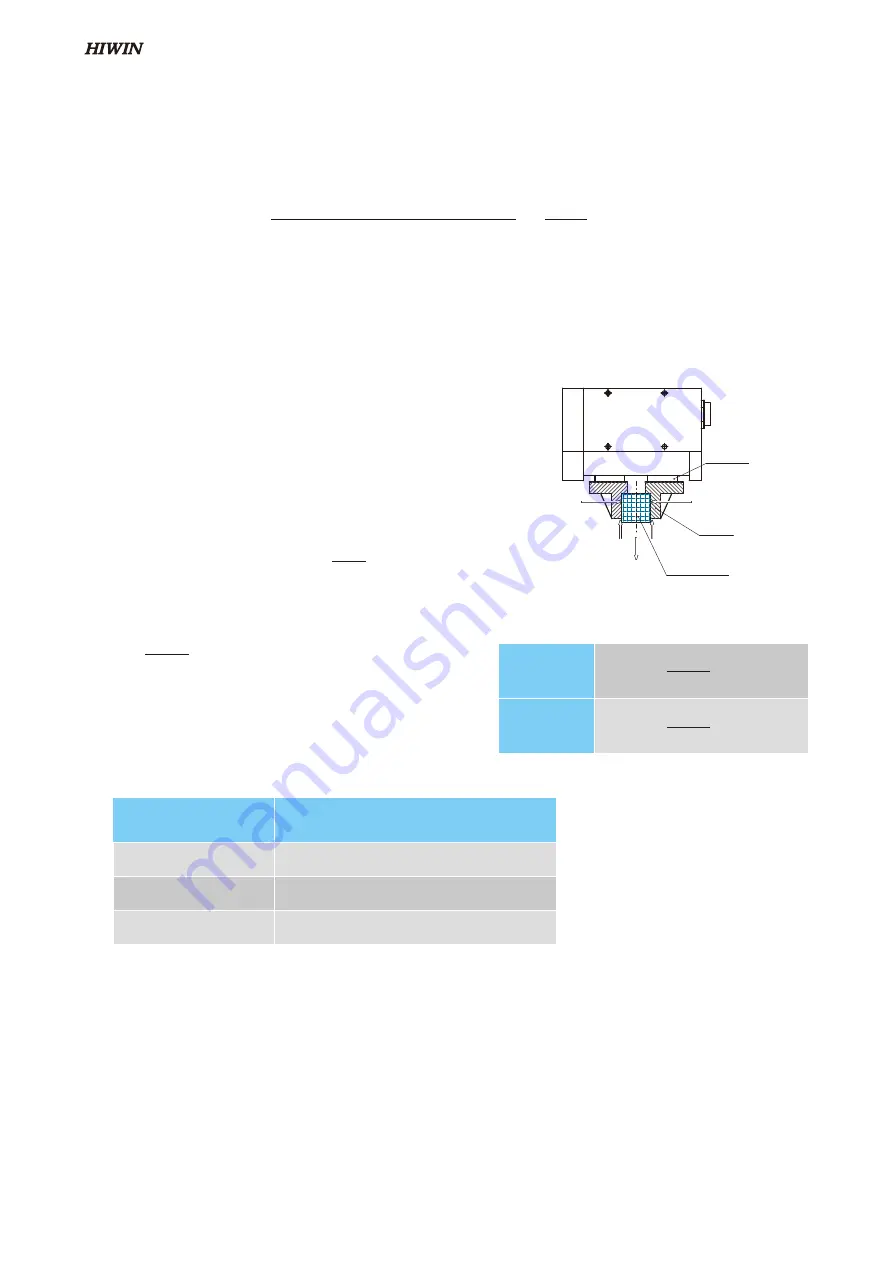
4.2 Calculation of Gripping Force
(Gripping force at least 10 to 20 times of the workspace weight)
When gripping a workpiece as in the figure:
F
:
Gripping force (N)
W
:
Workpiece weight (N)
μ
:
Coefficient of friction
The conditions under which the workpiece will not drop are:
2×μF>W
(Number of jaws)
→
F >
With
“
Sc
”
representing the extra margin,
“
F
”
is
determined by the following formula
:
F=
The
“
10 to 20 times or more of the workpiece weight
”
is calculated with a safety margin of
Sc
= 4, which allows for
impacts that occur during normal transportation.
〈
Reference
〉
Coefficient of friction
μ
According to Section 4.6, the pitch moment (Mp) of XEG-32 is 7.72 (N-m). Based on the following
calculation result, the allowable external load that can be withstood is 220(N). Therefore, it can be applied.
•
Step 4: Confirm external load (Section 4.6)
容許荷重
F(N) =
靜態容許力矩
M(N-m)
L(m)
=
7.72
0.035
= 220
>
10 (
外力
)
許容荷重
F(N) =
静的許容ピッチング
モーメントM(N-m)
L(m)
=
7.72
0.035
= 220
>
10 (
外部負荷
)
Allowable Load F(N) =
Static Allowable Moment M(N-m)
L(m)
=
7.72
0.035
= 220
>
10 (External Load)
F
工作物
F
μF
μF
W
夾具
夾爪
F
ワーク
F
μF
μF
W
指
グリッパ
F
Workpiece
F
μF
μF
W
Jaws
Gripper
W
2 x
μ
Sc×W
(2 x
μ)
[Note 1] Mass of a workpiece that the jaws can grip depends on the operating environment, contact
pressure, etc.
[Note 2] Even in cases where the coefficient of friction is greater than
μ
= 0.2, for reasons of safety,
select a gripping force which is at least 10~20 times greater than the workspace weight.
[Note 3] If high acceleration or impact forces are encouraged during motion, a further margin of safety
should be considered.
When
μ
=0.1
F=4
×
=20
×
W
When
μ
=0.2
F=4
×
=10
×
W
W
2 x 0.1
W
2 x 0.2
Coefficient of friction
μ
Fingers-Material of workpiece
(guideline)
0.1
Metal(surface roughness Rz3.2 or less)
0.2
Metal
over 0.2
Rubber, Resin, etc.
C02UE03-2007
32