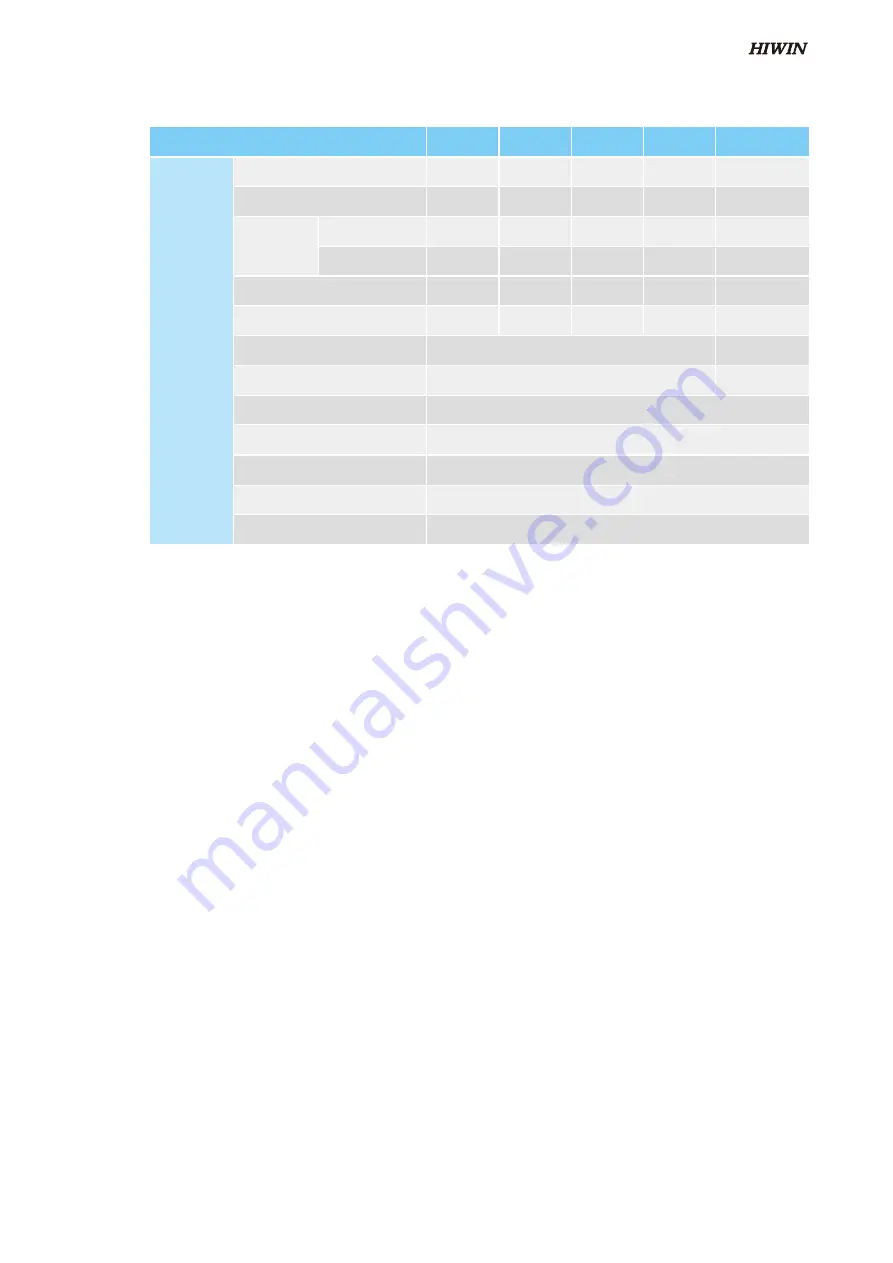
2.3 Specifications
[Note 1] The weight of workpiece(kg) * acceleration of gravity 9.81(m/s2) should be 1/10~1/20 of the gripping force(N).If the
gripper holding a workpiece moves or turns with high-acceleration/deceleration, choose the model with higher
force allowance.
[Note 2] Set the parameters and operation mode to avoid application of excessive impact force to the attachments (fingers)
during operation.
[Note 3] Apply proper amount of grease to the grease hole of single axis robot by a grease supply device or on the surface of
ball screws with brushes, XEG-32-PR clean and oil the drive guide shafts regularly.
[Note 4] Mass of a workpiece that the attachments (fingers) can grip greatly differs depending on the material quality, shape,
and gripping surface condition of the attachments (fingers). Design the attachments (fingers) to be lightweight and
minimum length.
[Note 5] The gripping force of the specification sheet is measured at a speed of 2mm/s and a gripping point(L) of 20mm.
The accuracy of the maximum gripping force is XEG-16
:±
30%
、
XEG-32
:±
16.6%
、
XEG-48
:±
15%
、
XEG-64
:
±
13.3%
、
XEG-32-PR
:±
20%.
Model
XEG-16
XEG-32
XEG-48
XEG-64
XEG-32-PR
Electric
Gripper
Stroke [both sides] (mm)
16
±
0.5
32
±
0.5
48
±
0.5
64
±
0.5
32
±
0.5
Gripping Force (N)
25~50
60~150
135~270
180~450
75~150
Speed (mm/s)
Motion
1~60
1~80
1~80
1~100
1~60
Gripping [Note 2]
1~10
1~20
1~20
1~20
1~10
Repeatability (mm)
±
0.01
±
0.01
±
0.02
±
0.02
±
0.01
Weight (kg)
0.4
0.7
1.5
1.9
1.1
IP Class
IP20
IP65
Cleanroom Class
ISO Class 5 (Class 100)
ISO Class 3
(Class 1)
Drive Device
Single-Axis Robot
Grease Supply of Drive Device
[Note 3]
500,000 cycles or 6 months
Impact
/
Vibration Resistance
(m/s
2
)
150 / 30
Operating Temperature Range
(
。
C)
5 ~ 45
Operating Humidity Range (%)
RH 35~85
(No condensing)
C02UE03-2007
7