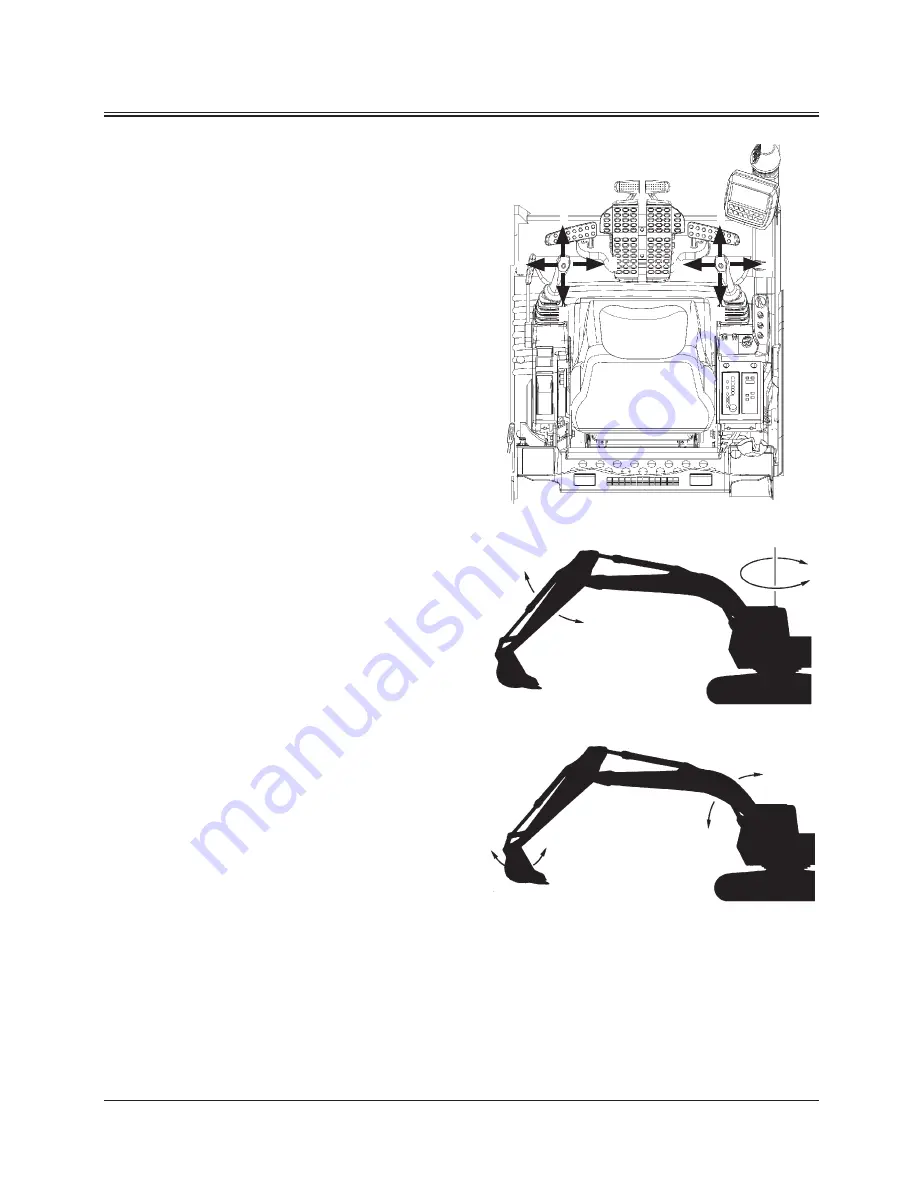
OPERATING THE MACHINE
5-2
M1J1-01-022
1
3
2
4
5
8
6
7
M104-05-001
M104-05-002
4
3
1
2
6
5
8
7
CONTROL LEVER (HITACHI PATTERN)
d
WARNING: Never place any part of body beyond
window frame. It could be crushed by the boom
if boom control lever is accidentally bumped or
otherwise engaged. If window is missing or broken,
replace immediately.
Prevent possible injury from unexpected machine
movement.
Make sure you know the location and function of
each control before operating.
The machine is equipped with a label showing the control
patterns of the levers and pedals.
IMPORTANT: When digging, avoid hitting tracks with
boom cylinders.
When digging over the end of the tracks,
travel motors should be at the rear to
maximize machine stability and lift
capacity.
When a lever is released, it will automatically return to neutral,
and that machine function will stop.
1- Swing Right
2- Swing Left
3- Arm Roll-In
4- Arm Roll-Out
5- Boom Lower
6- Boom Raise
7- Bucket Roll-In
8- Bucket Roll-Out
Summary of Contents for ZAXIS 450LC-3
Page 1: ...Serial No 020001 and up Hydraulic Excavator PART NO EM1J3 NA1 2 450LC 3 650LC 3 850LC 3 ...
Page 2: ... ...
Page 4: ......
Page 45: ...SAFETY SIGNS S 33 SS 862 SS 863 SS 859 1 2 3 ...
Page 46: ...SAFETY SIGNS S 34 SS3106039 SS3092349 SS 408 4 5 6 ...
Page 48: ...SAFETY SIGNS S 36 SS 024 SS 710 SS3089713 10 11 12 ...
Page 136: ...OPERATOR S STATION 1 88 MEMO ...
Page 138: ...BREAK IN 2 MEMO ...
Page 150: ...OPERATING THE ENGINE 3 12 MEMO ...
Page 270: ...TRANSPORTING 6 78 MEMO ...
Page 406: ...MAINTENANCE 7 136 M1J1 07 083 33 Retighten air compressor mounting bolts ...
Page 408: ...MAINTENANCE 7 138 MEMO ...
Page 410: ...MAINTENANCE UNDER SPECIAL ENVIRONMENTAL CONDITIONS 9 MEMO ...
Page 438: ...SPECIFICATIONS 12 14 MEMO ...
Page 470: ...OPTIONAL ATTACHMENTS AND DEVICES 13 32 MEMO ...
Page 474: ...INDEX 14 MEMO ...