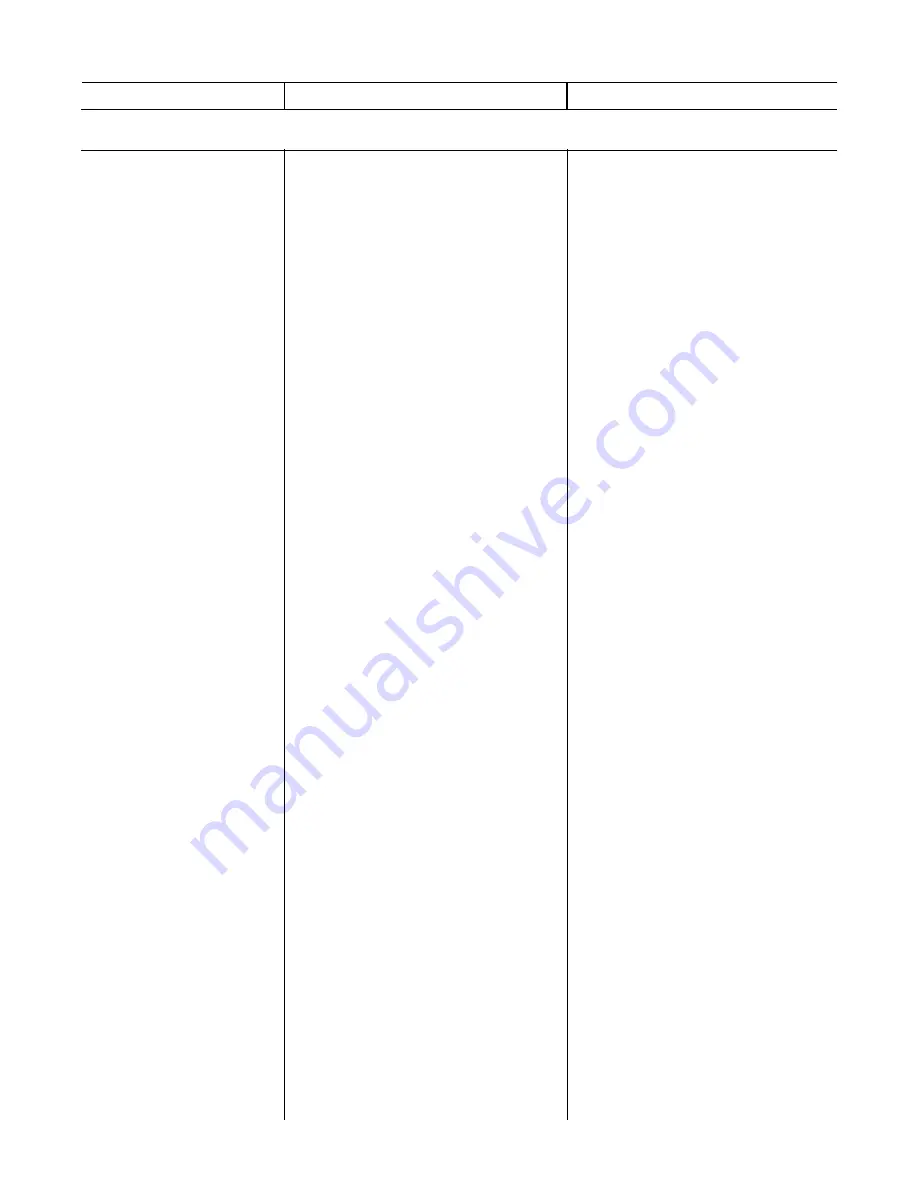
Henny Penny
Chick-fil-A Controls
Problem
Cause
Correction
COOKING SECTION (Continued)
Product not done
• Cook cycle aborted before alarm,
• See Diagnostic Mode
D 7
, page
and
“DONE”
flashes.
5-20, to see how many times
the cook cycle was stopped
before the end of the cycle.
• Frozen product placed in
• Use fresh or thawed product.
peanut oil
See Diagnostic Mode
D 5
, page
5-17, and if the controls sensed
frozen or overloaded batches.
• Wrong cook button pushed.
• If fryer hasn’t been used since
problem batch, see Information
Mode
4 B,
page 5-27
to see
what product was selected.
• Temperature programmed too low
• See Diagnostic Mode
D 10
,
or not prorammed properly.
page 5-24. If temperature
settings have been changed,
have the controls reintialized.
• Temperature probe out of
• Check temperature probe
calibration.
calibration. See section 4-6.
a.If less than 5° off, see Diagnos-
tic Mode
D 1
, page 5-11.
b.If between 5 and 15 degrees off,
calibrate probe. If more than 15
degrees off, replace probe.
• Slow fryer heat-up/recovery.
• See Diagnostic Mode
D 4,
page 5-15
for present day’s
performance.
Or see Informa-
tion Modes 5, 6, 7, 8, and 9 for
more information on this prob-
lem, pages 5-28 to 5-32.
•
Low voltage. See Diagnostic
Mode
D 3,
page 5-13
for
present day’s voltage perfor-
mance. See Information Modes
4, 5, 6, 7, 8, 9, and 14 for more
information on this problem,
pages 5-27 to 5-32, and 5-35.
• Low gas pressure. Have gas
pressure checked going to
burners, on gas fryers.
• Product too thick.
• Make sure chicken filets have
been fileted.
602
3-5