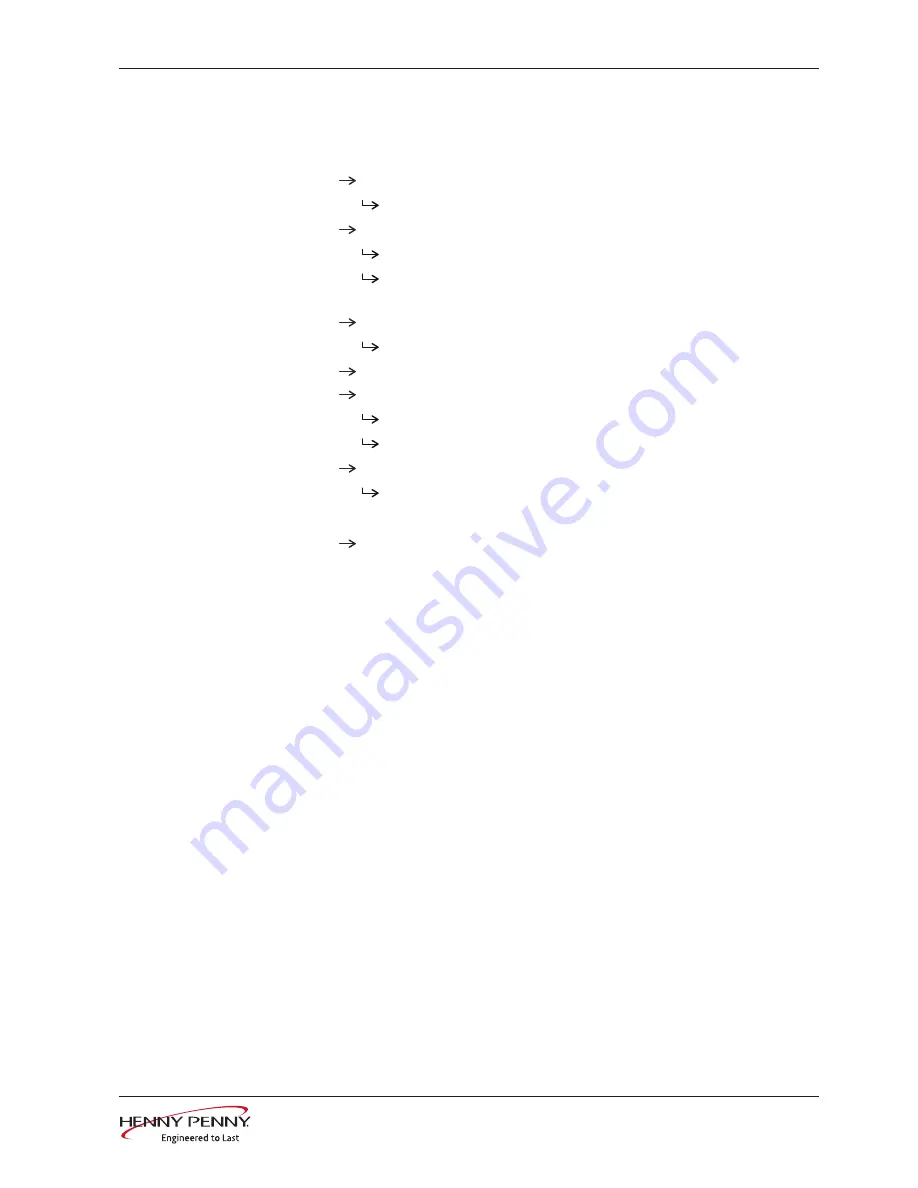
Service menu - appliance test
19
Service instructions
5.7.2 Calibrate cooking chamber sensor
Prerequisite Execute
Check calibration
and do not switch appliance off.
(see „5.7.1 Check calibration‟, Page 18)
Temperature display on the touch screen indicates 100°C.
Calibration
Adjust offset value by adjusting the roller.
Let 10 minutes adjustment time elapse.
The external measurement device must display a temperature
between 99°C – 99.5°C.
If necessary, adjust offset value again.
Let 10 minutes adjustment time elapse.
If the value is within the range, save calibration.
Saving the calibration
Touch "Save offset" field.
Saving of set value.
Automatic calibration of core temperature sensor.
Canceling the calibration
Touch the "STOP" field.
The calibration ends.
Exiting the calibration Touch the
Back
field.
Storing the calibration on
SD card
Also save data on internal SD card
(see „5.18 Backing up data‟,
Page 26)
.
10015160-0ASAE-A