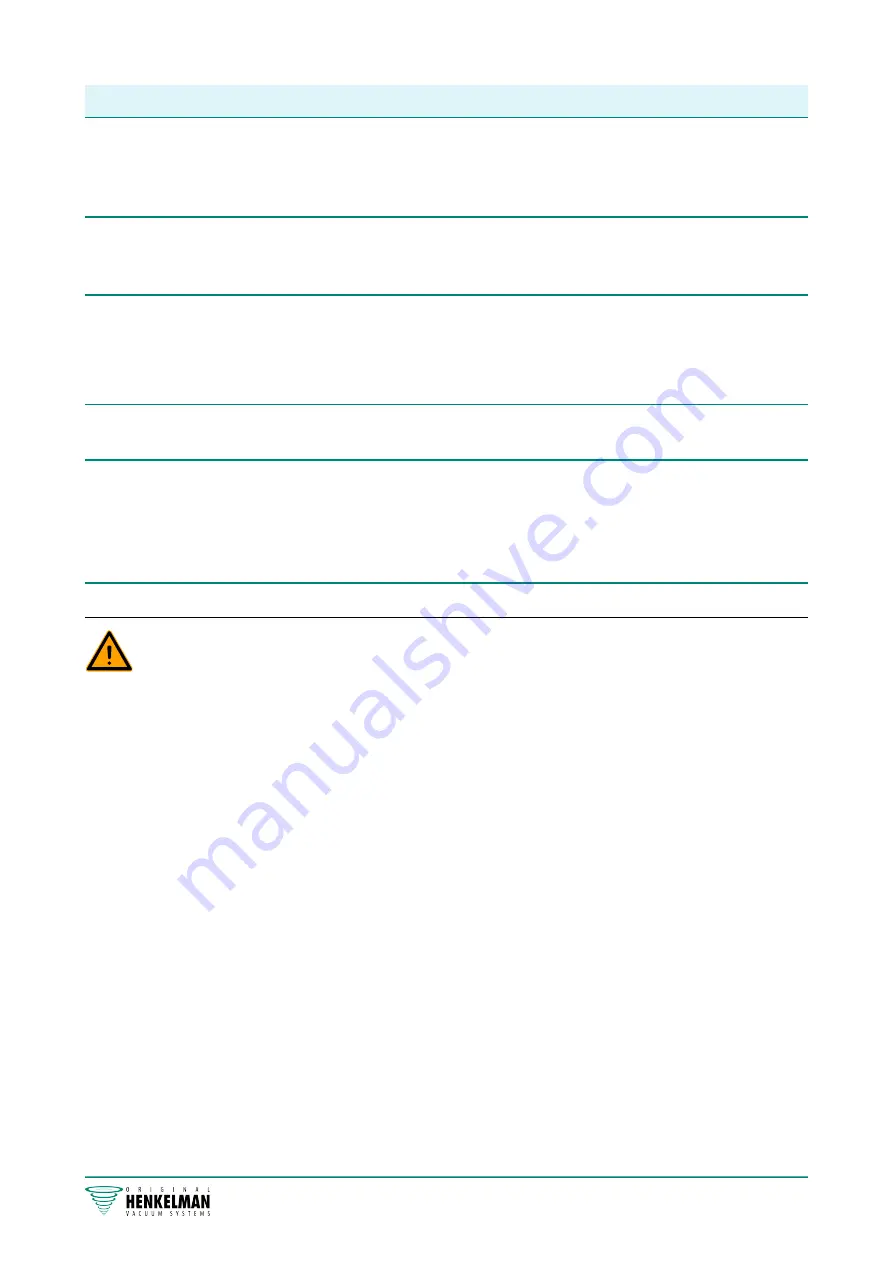
Operation 48
Function
Range
Conditions
Tenderising
30 – 99.8%
Time: 0 – 30
minutes
Only in case of ACS control. This is the value at
which the tenderising takes place. The duration of the
tenderising process can also be set.
Seal time
1-2 cutting time
0.1 – 4.0 seconds
This is the time that the sealing wire and/or the cut-off
wire are heated. The longer the time, the more heat is
transferred to the bag.
Soft-air
0 – 99 seconds
(for 10-prog control)
0 – 20 seconds
(for ACS)
This is the time that air is softly released into the
chamber after sealing has taken place. The best way to
determine the right time is trial and error.
Cleaning of the
pump
15 minutes
Fixed value.
Sleeper option
1 – 100 minutes
(for 10-prog control)
1 – 59 minutes
(for ACS)
This is the time the pump will continue running after
running a cycle. This maintains the pump at operating
temperature and prevents unnecessary starting and
stopping of the pump, which causes additional wear of
the pump.
The vacuum in the chamber must be at least 30% at the moment of sealing.
If the pressure is reduced, the boiling point of liquids will be decreased; see Figure 16: Vapour
Pressure Curve of Water on page 49. As a result of this law of nature, a product may start
boiling. In addition to contamination of the machine, this will reduce the weight and quality of the
product to be packaged.
When packaging moisture-containing products, such as soups and sauces, it is important to
closely monitor the vacuuming process. The moment bubbles are formed or the product starts to
bubble, you should immediately proceed to the next step in the cycle. See Proceeding to the Next
Step in the Cycle on page 32.
By letting products cool down sufficiently prior to starting the vacuuming process, a higher vacuum
can be achieved.
If the machine is equipped with the Liquid Control option, the control will automatically proceed to
the next step if the product starts boiling.
When packaging moisture-containing products, it is important to run the pump cleaning program
at least once a week. When moisture-containing products are vacuumed on a daily basis, it is
recommended to run the pump cleaning program at the end of the day.