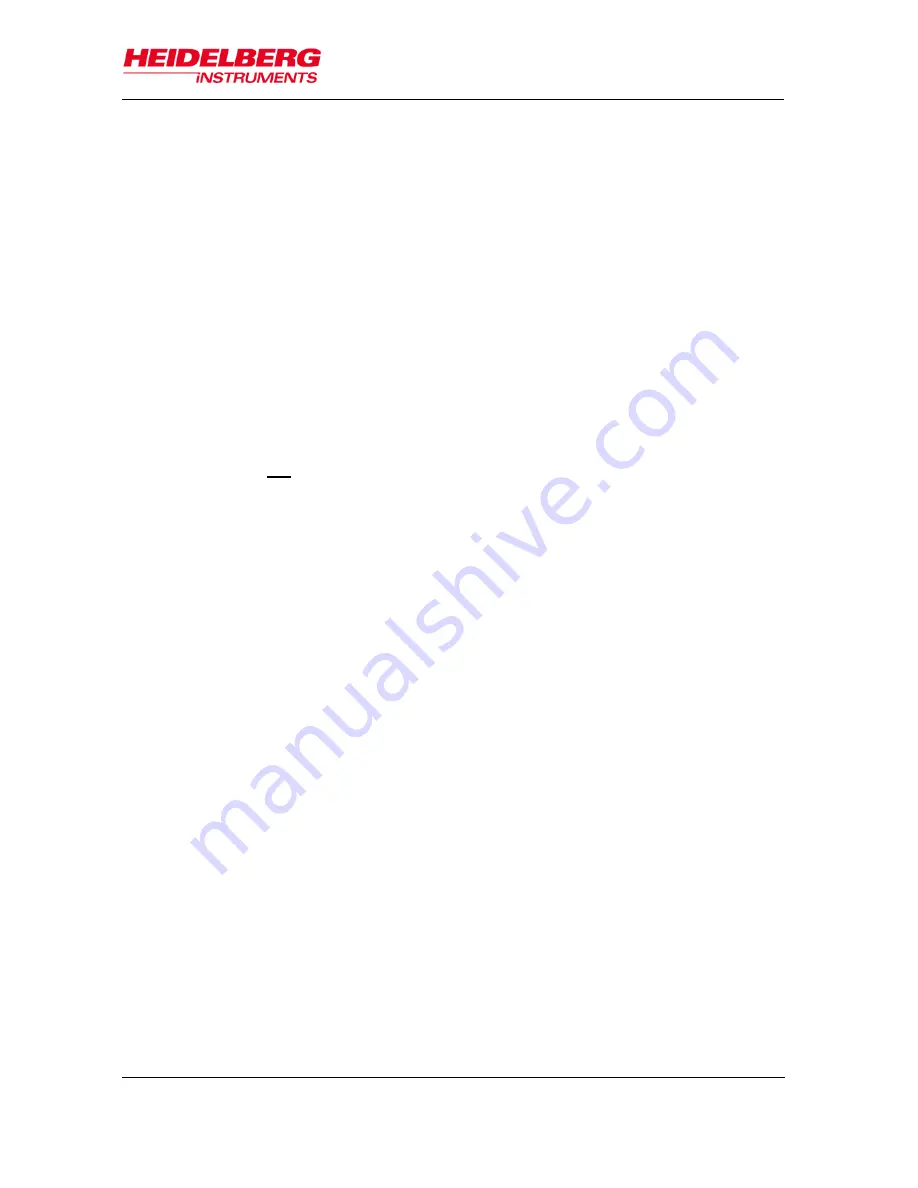
µPG 501
26
User Guide
SUBSTRATE PROCESSING
The steps of processing of a substrate are:
•
Post exposure bake:
Depending on application and resist type, a post exposure
bake of the exposed substrate on a hot plate or in an oven may be required.
Refer to the resist manufacturer’s documentation for specific information on this.
The resists recommended here for standard purposes do not need a post
exposure bake.
•
Developing:
The exposed parts of the resist have been chemically altered by
the light and can now be washed out of the resist layer by use of specific
developer chemicals. If the energy dose was sufficient to enable the reaction
through the complete layer, after developing, the surface of the coated substrate
is accessible wherever the resist was exposed with full intensity. In regions
where the energy dose was below the limit, only a part of the layer is removed,
thus allowing for three dimensional structuring of sufficiently thick resist layers.
Note
: In negative resist such as SU8, the developer removes the parts which
were not exposed.
Developing times depend on resist type, resist thickness, and developer type, as
well as the energy dose used during exposure. Typical developing times are 1 –
1.5 minutes for thin resists, and around 0.5 minutes/µm for thick resists. The
combination of energy and developing technique can influence the quality of an
exposure result strongly. Using too high energy during exposure or using too
strong developer makes the developing time very critical, leading to plate-to-
plate structure size variations. On the other hand, too low energy or too diluted
developer can lead to angled and irregular resist walls, causing bad linewidth
stability and rough pattern edges. The best combination of exposure parameters
and processing procedure for a specific application has to be found by series of
test exposures.
•
Hardbake:
A hardbake can serve to better prepare the remaining resist layer for
the next processing step by hardening it. On the down side, it can round sharp
resist edges and lead to rifts in the resist layer. Again, it depends on application
and resist if a hardbake is required and recommendable, and how it should be
done. Please refer to the resist manufacturer’s documentation concerning this.
•
Etching:
In 2D masks, the next step is to etch away the metal layer wherever it
is accessible. This copies the design from the resist layer into the metal layer,
creating a mask for further copies of the design onto other substrates with the
help of e.g., flashes from a mercury vapor lamp. There are different methods of
etching. The most common one is wet etching, where the developed substrate,
after thorough rinsing, is put into a bath of etch. Etching time depends on the
metal layer thickness and the etchant age (etch usually can be reused many
times until it is saturated). If etching is done too short, small structures are not
opened, or have irregular edges. If the substrate stays in the etcher too long, the
so called ‘under-etching’ can happen, where the etch reaches under the resist,
causing irregular edges and bad linewidth stability.
Summary of Contents for mPG 501
Page 1: ...User Guide PG 501...
Page 4: ......
Page 40: ...PG 501 36 User Guide Notes...
Page 41: ...PG 501 User Guide 37 Notes...
Page 42: ...PG 501 38 User Guide Notes...