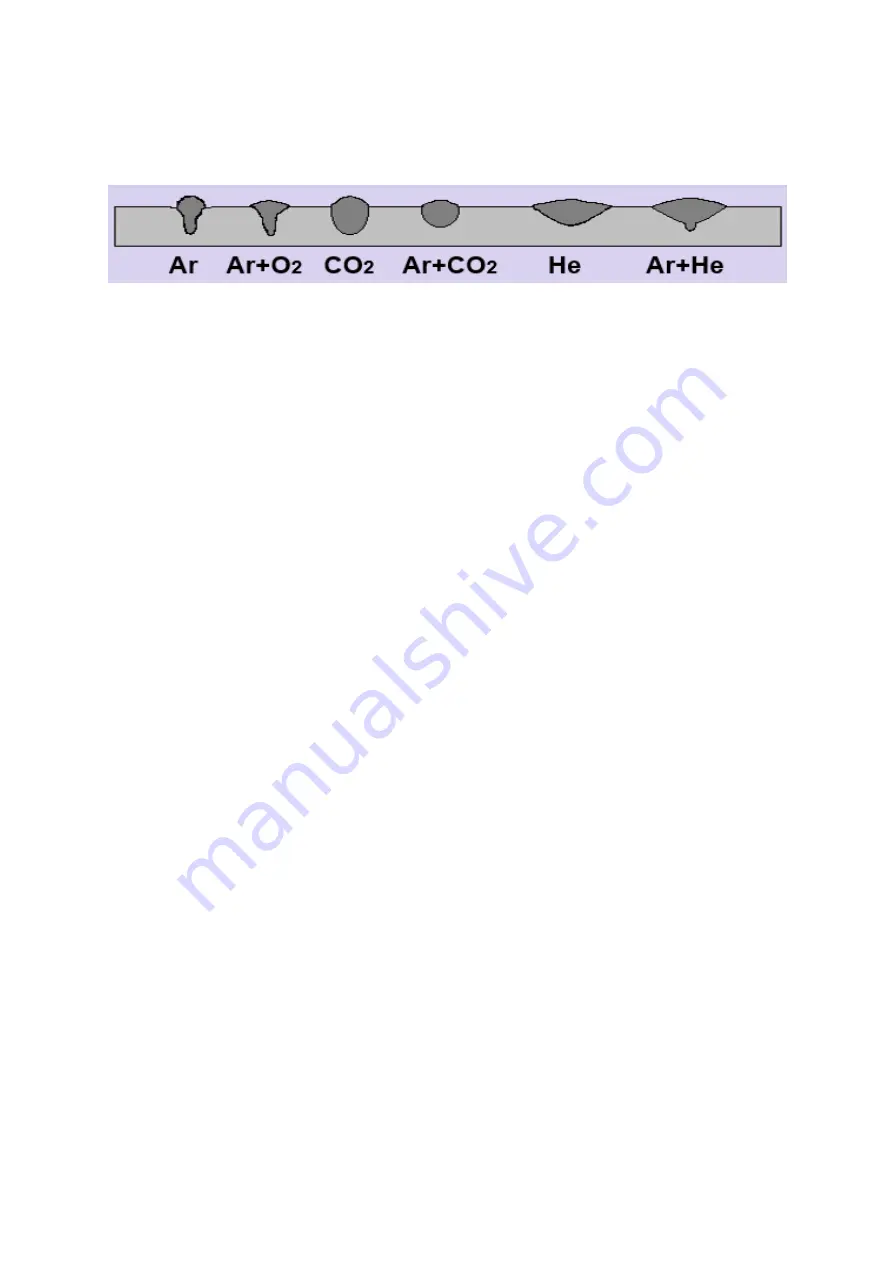
TitanMig Pulse 270/3500/5000 Operators Manual
Issue. A 0516
29
Penetration Profiles
Different shielding gas formulations produce quite different and significant changes to the
penetration
profile
of the weld.
Selecting the Correct Shielding Gas
Base Material considerations
Base material type or classification
Base material thickness
Joint design
Welding position
Metal transfer mode
Spray transfer
Globular transfer
Dip transfer
Pulsed current transfer
Quality aspect of the finished weld
Mechanical and chemical requirement
Surface finish
Penetration
Economics of the weld
Clean up costs (acceptable level of spatter)
Welding travel speed
Flow rate of shielding gas
Cost of shielding gas
Carbon Steel - Low content CO2 Mixtures
Most shielding gases are based on the argon/carbon dioxide/oxygen system for welding carbon steels.
Low content CO2 mixture (1-7% CO2) produce welds with a “Wine Glass” penetration profile similar to
that produced by pure argon, along with a very stable arc and low spatter levels.
Due to these mixtures having a relatively low heat input, fusion defects and porosity can occur when
welding heavy sections due to the penetration profile, low fluidity and the rapid freezing of the weld
pool.
Carbon Steel – Intermediate content CO2 mixtures
Intermediate content CO2 mixtures (8-15% CO2) produce a higher heat input giving improved
characteristics and broader penetration profile.
These mixtures are more versatile than the low content CO2 mixtures and sound welds can be
produced over a wide range of material thickness.
These mixtures usually produce the most stable welding arc characteristics and are normally the best
general purpose shielding gases for Mild, Carbon and Low Alloy Steels.
High content CO2 mixtures
High content CO2 mixtures (16-23% CO2) allow for further improvements in the fusion characteristics
and the penetration profiles of the weld.
These mixtures are ideally suited for welding heavy sections especially in multi pass situations.
The stiff weld pools cool relatively slowly which aids welding and complete fusion to the weld side
walls.
Any entrapped gas has time to disperse before freezing of the weld pool occurs.
The arc is less stable than with the low content CO2 mixtures which may result in increased spatter
levels.
Summary of Contents for TitanMig Pulse 2700
Page 2: ...TitanMig Pulse 2700 3500 5000 Operators Manual Issue A 0516 ...
Page 36: ...TitanMig Pulse 270 3500 5000 Operators Manual Issue A 0516 32 4T Special 2T ...
Page 53: ...TitanMig Pulse 2700 3500 5000 Operators Manual Issue A 0516 49 ...
Page 65: ...TitanMig Pulse 2700 3500 5000 Operators Manual Issue A 0516 61 6 0 Electrical Diagram ...
Page 70: ...TitanMig Pulse 2700 3500 5000 Operators Manual Issue A 0516 66 ...
Page 71: ...TitanMig Pulse 2700 3500 5000 Operators Manual Issue A 0516 67 ...