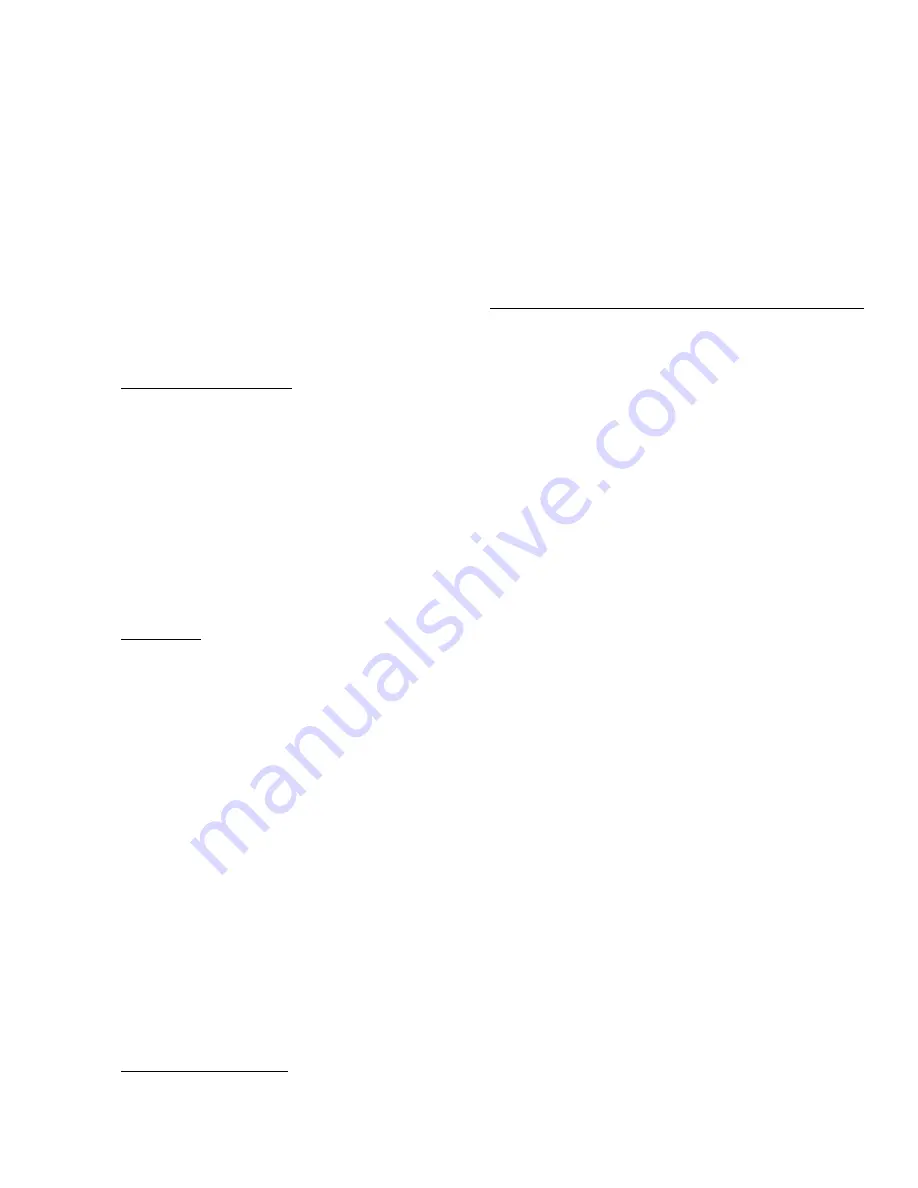
c. Adjust R145 for 1.0 V at TP20.
d. Set the exciter meter to EXC VIS and observe the reading.
e. Using jumper JP13 and/or JP14 to set in the attenuation
necessary to bring the drive level from the exciter to 0.300
watts as near as practical for 2000 watts transmitter out-
put.
f. Move jumper JP12 to position 1-2 to enable the AGC.
g. Adjust R156 such that the transmitter output power drops
from 2000 watts to 1200 watts (60% of full power or -2.2
dB).
h. Increase the drive until the transmitter output is once again
2000 watts.
The exciter drive level should normally be in the range of 0.500
to 0.600 watts.
5.8.2
Visual Power Reduction
If one of the two power supplies in the power module should fail
this circuit will adjust the drive such that the transmitter will
continue to operate at a reduced power with the remaining power
supply.
a. Preset R175 fully CW.
b. Turn OFF the AC circuit breaker for one of the power
supplies.
c. Adjust R175 for a visual power output of 150 watts peak
of sync.
d. Turn ON the AC circuit breaker and the visual power
should return to 2000 watts.
5.8.3
Aural AGC
a. Preset the following:
1. JP3 to position 2-3 AGC out
2. JP11 to positions 1-2 and 3-4 3 dB Attenuator out
3. JP6 to positions 1-2 and 3-4 2 dB Attenuator out
b. Turn on the transmitter ON and increase the aural drive
for 200 watts.
c. Adjust R143 for 1.0 V at TP3.
d. Set the exciter meter to AURAL VIS and observe the
reading.
e. Using jumper JP11 and/or JP6, set in the attenuation
necessary to bring the drive level from the exciter to 0.300
watts as near as practical for 200 watts transmitter output.
f. Move jumper JP3 to position 1-2 to enable the AGC.
g. Adjust R44 such that the transmitter output power drops
from 200 watts to 120 watts (60% of full power or -2.2
dB).
h. Increase the drive until the transmitter output is once again
200 watts.
The exciter drive level should normally be in the range of 0.500
to 0.600 watts.
5.8.4
Aural Power Reduction
If one of the two power supplies in the power module should fail
this circuit will adjust the drive such that the transmitter will
continue to operate at a reduced power with the remaining power
supply.
a. Preset R176 fully CW.
b. Turn OFF the AC circuit breaker for one of the power
supplies.
c. Adjust R176 for a AURAL power output of 15 watts peak
of sync.
d. Turn ON the AC circuit breaker and the aural power
should return to 200 watts.5.1
5.9
Component Replacement On Circuit
Boards
The circuit boards used in the VHF TV exciter are double-sided
circuit boards with plated through-holes. Soldering on this circuit
board is possible with conventional tools if care is observed.
For repair, a de-soldering station is suggested such as an Air-Vac
PVSG-60E De-Soldering System made by Air-Vac Engineering
Co., Inc., 100 Gulf St, Milford, CT 06460 (203-874-2541). This
de-soldering system utilizes a venturi to develop the suction and
therefore requires an air pressure source of approximately 35 PSI.
It is relatively inexpensive for such a system and works well.
Techniques must be developed using the de-soldering station.
Sometimes, it may be necessary to add solder to the connection to
assist heat flow to the connection several times until the solder can
be removed in steps. Possibly, removing solder from both sides of
the circuit board will assist in clearing the through-holes.
The circuit board used in the VHF TV exciter utilizes plated through-
holes. Because of these through-holes, solder fills the holes by
capillary action. This condition requires that defective components
be removed carefully to avoid damage to the circuit board.
On all circuit boards, the adhesive securing the copper track to
the circuit board melts at almost the same temperature at which
solder melts. A circuit-board track can be destroyed by excessive
heat or lateral movement during soldering. Use of a heat source
no larger than necessary with steady pressure is required for
circuit board repair.
To remove a component from a circuit board such as the type
used in the VHF TV exciter, cut the leads from the body of the
defective component while the device is still soldered to the
circuit board.
Carefully grasp each component lead, one at a time with mini-
ature long-nose pliers. Heat each lead independently. When the
solder begins to melt, carefully pull the lead from each hole. The
holes may then be cleared of solder with vacuum.
Install the new component and solder the component in place.
Section V - Maintenance
888-2457-001
5-5
WARNING: Disconnect primary power prior to servicing.
Summary of Contents for Platinum HT EL 2000LS
Page 4: ...This page left blank intentionally...
Page 6: ......
Page 8: ...ii...
Page 12: ...This page left blank intentionally...
Page 38: ...This page left blank intentionally...
Page 46: ...This page left blank intentionally...
Page 54: ...This page left blank intentionally...