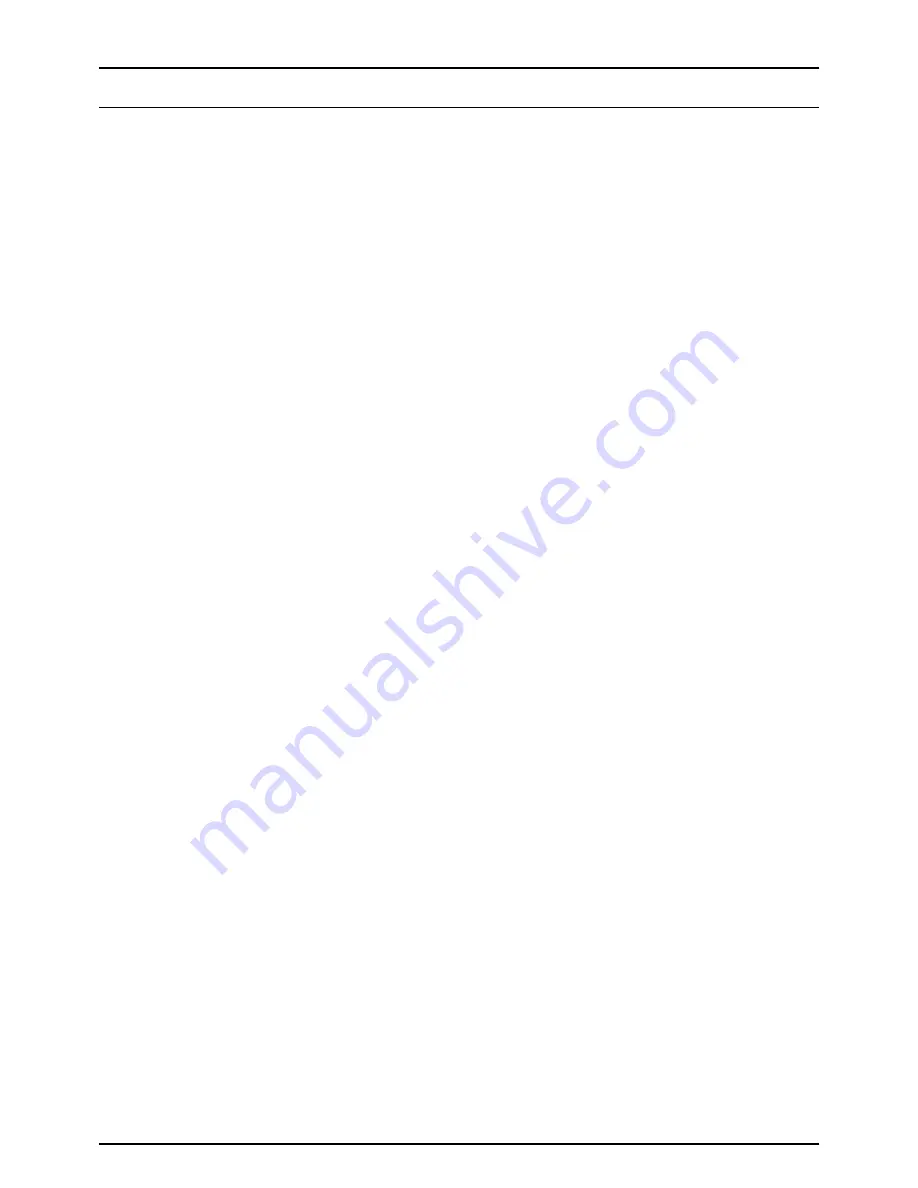
97
7 - Fault finding
Operational Problems
General Info
Operational incidents are often due to the same reasons:
•
A suction leakage reduces the pump pressure and may interrupt suction completely.
•
A clogged suction filter may damage suction or interrupt and prevent the pump from running normally.
•
A clogged pressure filter increases pressure in the fluid system in front of the pressure filter. This may blow the safety
valve.
•
Clogged in-line filters or nozzle filters increase pressure in the pressure gauge, but it decreases pressure at the nozzles.
•
Impurities sucked in by the pump may prevent the valves from closing correctly, thus reducing the pump flow.
•
A bad reassembly of the pump elements, especially the diaphragm covers, causes air intakes or leaks and reduces the
pump flow.
•
Rusted or dirty hydraulic components cause bad connections and early wears.
•
A poorly charged or faulty battery causes failure and misbehaviour in the electrical system.
Therefore ALWAYS check that
•
Suction and pressure filters, as well as nozzles, are clean.
•
Hoses are free of leaks and cracks, especially suction hoses.
•
Gaskets and O-rings are present and in good condition.
•
Pressure gauges are in good working order. Dosage accuracy depends on it.
•
Operating unit functions properly. Use clean water to check.
•
Hydraulic components are clean.
•
The tractor battery and its connectors are in good condition.
Summary of Contents for NAVIGATOR FORCE
Page 4: ...1 EU Declaration 4 ...
Page 12: ...2 Safety Notes 12 ...
Page 54: ...4 Sprayer setup 54 ...
Page 76: ...6 Maintenance 76 Boom lubrication oiling plan ...
Page 112: ...8 Technical specifications 112 ...
Page 116: ...Index 116 ...
Page 118: ...HARDI INTERNATIONAL A S Herthadalvej 10 DK 4840 Nørre Alslev DENMARK ...