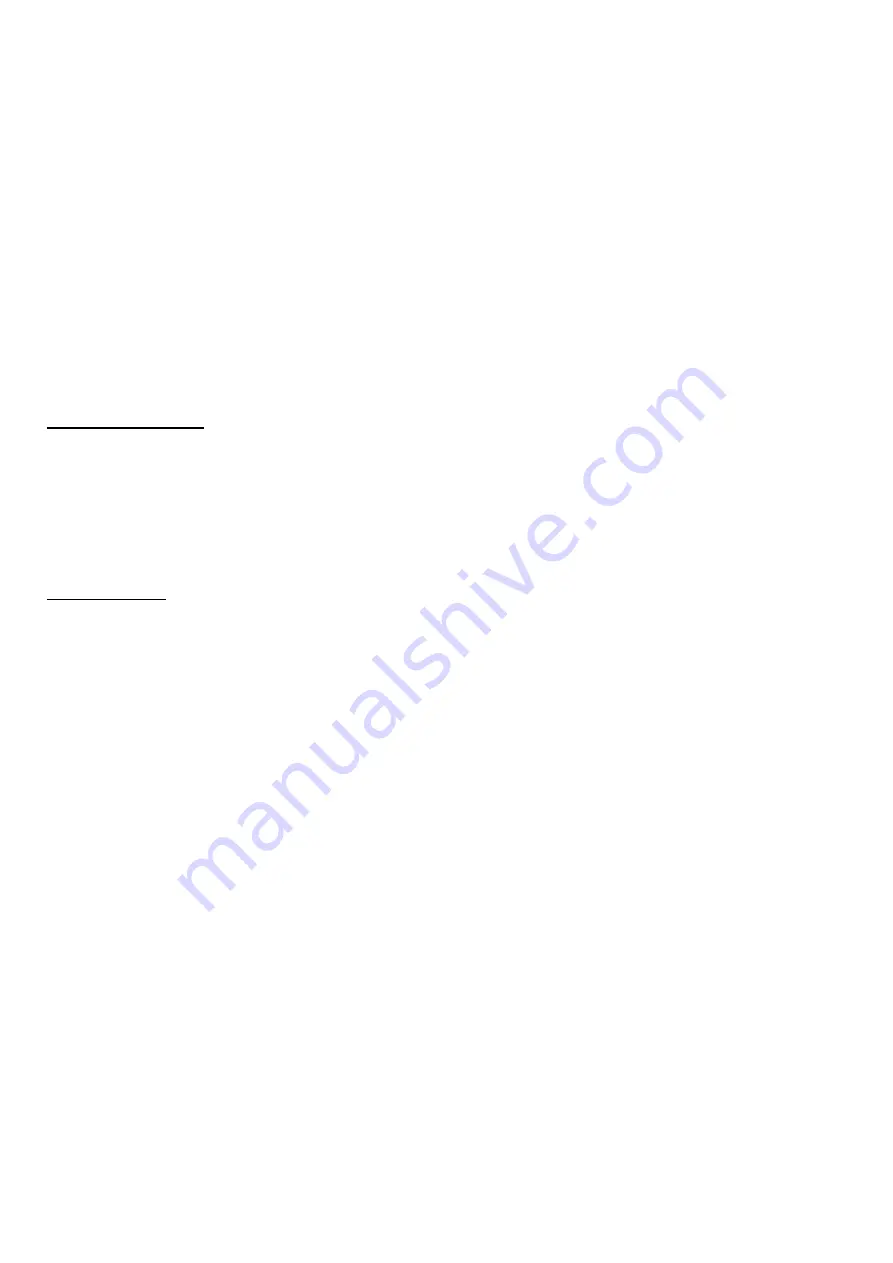
HAMWORTHY HEATING LTD
24
SHAFTESBURY HE
500001049/N
11.6 Installation Noise
In order to avoid the possibility of noise from the
installation, care should be taken to follow the
manufacturer’s instructions. Particular attention should
be paid to minimum water flow rates. If acoustic
insulation is added to the boiler, care must be taken not
to impede combustion or ventilation air flow. If in doubt
contact the manufacturer.
11.7 User Instructions
When the above is complete, the boiler owner or their
representative should be made aware of the lighting
and operating instructions . A practical demonstration
should be given describing each functional step. This
Installer's Guide and burner Operating Instructions
should then be handed over and kept in a safe place for
easy reference.
12.0 FAULT
FINDING
12.1 Fault
Finding
Fault finding on the burner control system is detailed
in the burner manufacturers instructions. If the boiler
still cannot be operated satisfactorily after following
these instructions, consult Hamworthy Heating for
assistance.
13.0 SERVICING
A qualified engineer registered for working on non
domestic gas or oil appliances should check and ensure
that the flue, its support and terminal, the ventilation to
the boiler house, safety valve, drain, water filter if fitted,
pressure gauge, etc.; are in a serviceable and working
condition and still comply with the relevant standards
and codes of practice - see
Section 3.1
The boiler should be serviced at regular intervals,
not exceeding SIX months for oil fired boilers, or
TWELVE months for gas fired boilers.
When carrying out boiler servicing always consider
both your own safety and that of others. The use of
protective equipment (e.g. eye protection, face
mask, protective gloves, etc.) is recommended
where necessary.
13.1Initial Inspection
a.
Operate boiler and check for any signs of
unsatisfactory operation, water leaks, gas leaks, oil
leaks or unusual noise from burner oil pump or
motor.
b.
After allowing burner to reach stable firing
conditions for approximately 15 minutes, carry out
combustion gas check.
Measure CO
2
, CO, flue gas temperature, smoke
number (for oil) and water temperature rise across
the boiler. The readings obtained should be noted
for reference upon completion of the servicing
procedure.
c.
Measure either gas pressure at burner head, or
oil pressure at burner pump, as applicable, and
check value is correct for size of boiler in question.
d.
Check operation of both boiler and heating
system controls, then set boiler control thermostat
to OFF.
Allow the boiler/burner to cool.
13.2 Burner Service Procedure.
SWITCH OFF ELECTRICAL SUPPLY TO
BOILER AT ISOLATOR AND SHUT OFF FUEL
SUPPLY TO BOILER.
Clean and service the burner in accordance with
the burner manufacturers instructions.
a.
Disconnect electrical and fuel connections to
burner, as necessary.
b.
Disconnect burner from mounting flange and
remove from front of boiler.
13.3 Boiler Service Procedure
a
. After removing burner, remove boiler casing,
control panel (taking care to remove thermostat
bulbs) and front insulation to gain access to front
section of boiler. The power supply to the control
panel and additional control cables, if used, can be
disconnected by removing upper front panel,
lowering fascia after removing thermostat knobs,
pulling out the top half of the terminal block and
removing the gland plate.
b
. Remove heat exchanger access plates (11,12
and 15 referring to Fig. 15.1), and corresponding
insulation panels, from boiler front section.
Boiler combustion chamber and heat exchanger
flueways are now accessible for cleaning with
suitable brushes and a vacuum cleaner.
c
. Access to rear of heat exchanger flueways and
combustion chamber can be obtained by removing
rear insulation wrap, flue box (31), cover plate (32),
insulation and fire brick (28) from rear of boiler.
The refractory fire brick (28), located at the rear of
the boiler, should be checked at least once every
two years and replaced if necessary.
N.B.
Removal of flue box requires disconnection
of flue.
d
. Replace all access/cover plates, ensuring that
all gaskets and insulation panels are correctly
fitted.
Refit securing studs/nuts and tighten evenly.
e
. Refit boiler insulation, casing and control panel
(ensure thermostat bulbs are correctly located in
pocket). For guidance, refer to
Section 10.
f
. Refit burner. Reconnect fuel and electrical
supplies.
g
. Turn on fuel supply and check soundness of
fuel supply pipework.
h
. Check all flue joints for integrity.
i
. Check ventilation ducts/grilles to boiler room
and ensure they are clear.
j
. Re-commission boiler as detailed in relevant
parts of
Section 11.0: COMMISSIONING &
TESTING