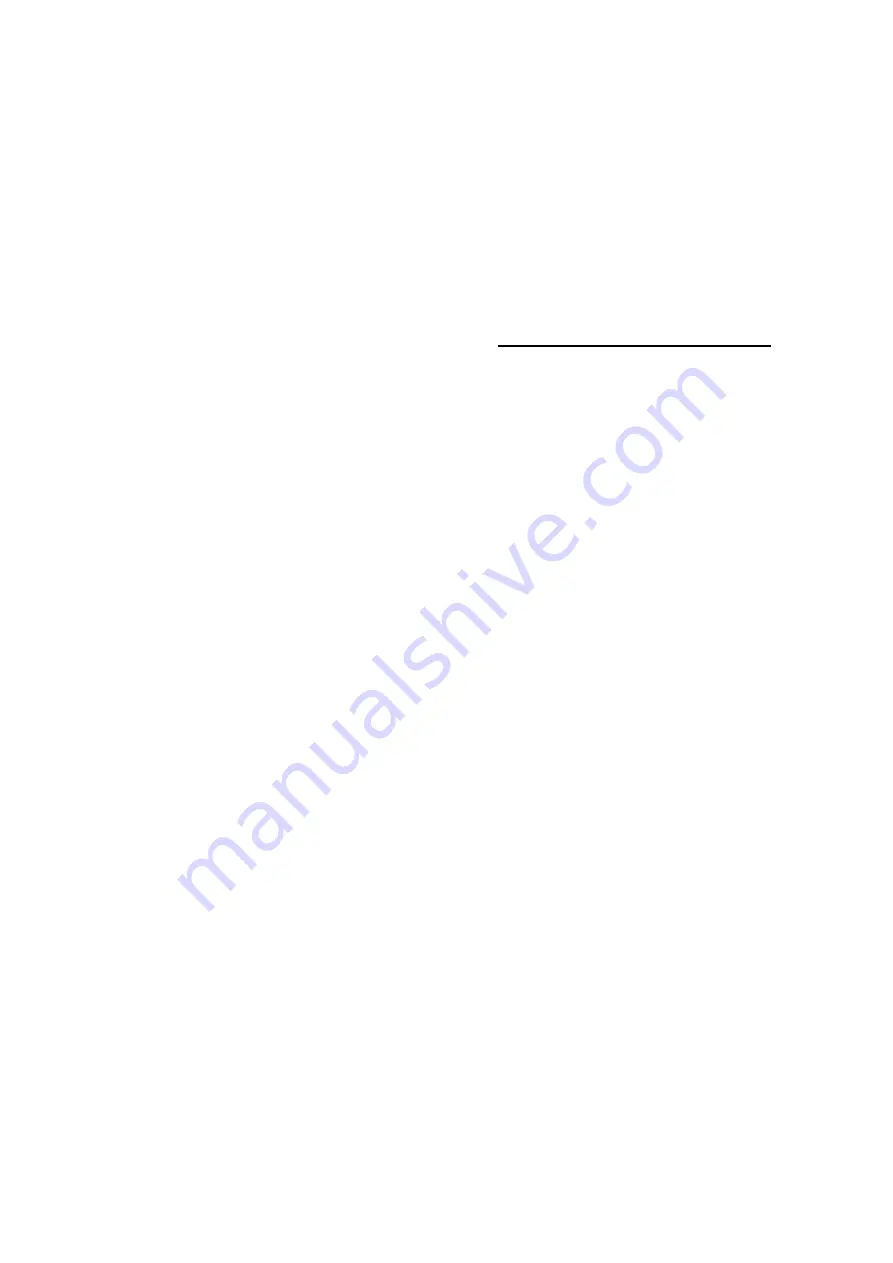
HAMWORTHY HEATING LTD
21
SHAFTESBURY HE
500001049/N
10.6 Control Panel (Refer to Figs. 9.1 & 9.2)
When fully assembled, access to the control panel
for wiring purposes is gained by firstly removing the
upper front casing panel. Turn the two latches a
quarter turn using a screwdriver or coin and lift off.
The fascia can then be hinged downwards by
unlatching the catch on the top right hand using a
screwdriver.
NOTE:
before attempting to hinge the
fascia down, the thermostat knobs must be pulled
off and the temperature limiter (high limit) cover
knob unscrewed and removed.
With the fascia hinged down, the terminals are
exposed and the power supply can be connected to
the appropriate terminals via the glands in a
removable plate at the bottom right hand side. The
upper front casing panel has a cut out appropriately
positioned beneath the gland plate to allow the
power supply cables to enter the casing and to allow
the flying leads to the burner to exit.
A powered lock-out terminal and a remote control
link C1-C2 are also provided together with an
optional volt free contact kit (see Figs. 9.1,9.2 &
15.3) the terminals being adjacent to the power
supply, and cables for these functions should be run
in a similar manner. For remote control remove the
wire link between C1-C2 and replace with control
cables. If the panel is for High/Low burners an
additional link C3-C4 is also supplied, removal of
which holds the burner on low fire. This link can
also be replaced by control cables if remote high/low
operation is required. For ease of disconnection,
the terminals used are of the plug and socket type
and hence all external wiring can be easily removed
by pulling the top half of the terminal rail upwards
and threading cables through the gland plate once
removed.
Depending on the type of burner fitted, the panel will
provide a single flying lead terminating in a seven
pin plug for connection to an on/off burner, or an
additional flying lead terminating in a four pin plug
for connection to a high/low burner. The panel for a
high/low burner will also have an additional
thermostat, hours run meter and run lamp.
Two fuses are provided for the fuse holder on the
panel rated at 5A and 6.3A. The correct fuse must
be selected for the burner supplied -refer to burner
instructions supplied separately.
When wiring is complete, raise hinged fascia and
click into position by pushing on latch screw.
Replace thermostat knobs and front casing panel
allowing cabling to exit from the cut out.
It should be noted that if a 3 phase burner be
supplied, the 3 phase supply should be wired direct
to the burner and a separate 230V single phase
supply wired to the panel.
NOTE:
- All cables must exit the boiler casing via
the cutout in the bottom right hand edge of the
upper front door and must not be routed adjacent to
the burner mounting plate.
THE CABLES MUST
NOT BE ROUTED ACROSS THE BURNER OR
ITS MOUNTING PLATE.
10.7 Bracket kit for use on modulating burner
A bracket kit, HHL Part No. 563605242, for
repositioning the regulator box RWF40 on Riello
modulating burner R40G20D, is provided with fitting
instructions. The fitting of this bracket ensures that
the regulator box does not foul the boiler front panel
when the modulating burner is fitted.
11.0 COMMISSIONING
AND
TESTING
11.1 Electrical Installation
Wiring
MUST
be checked by a suitably competent
person. An isolator correctly fused should be sited close
to the boiler. Refer to the burner instructions.
It should be noted that if a 3 phase supply is
required, it should be wired direct to the burner and
a separate 230V single phase supply wired to the
panel.
The boiler is supplied with a remote stop/start circuit for
time clock operation.
Any other interlocks, i.e.
Pressurisation unit, BEM System should be wired in
series with the remote stop/start loop.
11.2 Gas Installation
For design see
Section 5: GAS SUPPLY.
The whole of the gas installation including the meter
must be inspected and tested for soundness and
purged in accordance with the recommendations of
IGE/UP/1
or
IGE/UP/1A
as appropriate.
11.3 Water Circulation System
For design see
Section 8: WATER SYSTEM.
The system should be thoroughly flushed out with cold
water without the pump in position. Ensure all the
valves are open.
With the pump fitted the system should be filled and air
locks cleared. Vent the radiators and check for leaks.
If the system is unvented the pressurisation unit should
not be utilised for the initial filling. This should be carried
out using a WRC approved double check valve and
temporary filling loop. In order to comply with local
Water Authority Regulations, this loop must be
disconnected when filling is complete. Water treatments
should not be fed through the pressurisation unit unless
permitted by the manufacturer. Check the expansion
vessel cushion pressure as detailed by the
manufacturer's Installer's Guide.
11.4 Commissioning The Boiler
Only competent persons registered for working on
non domestic gas appliances should attempt the