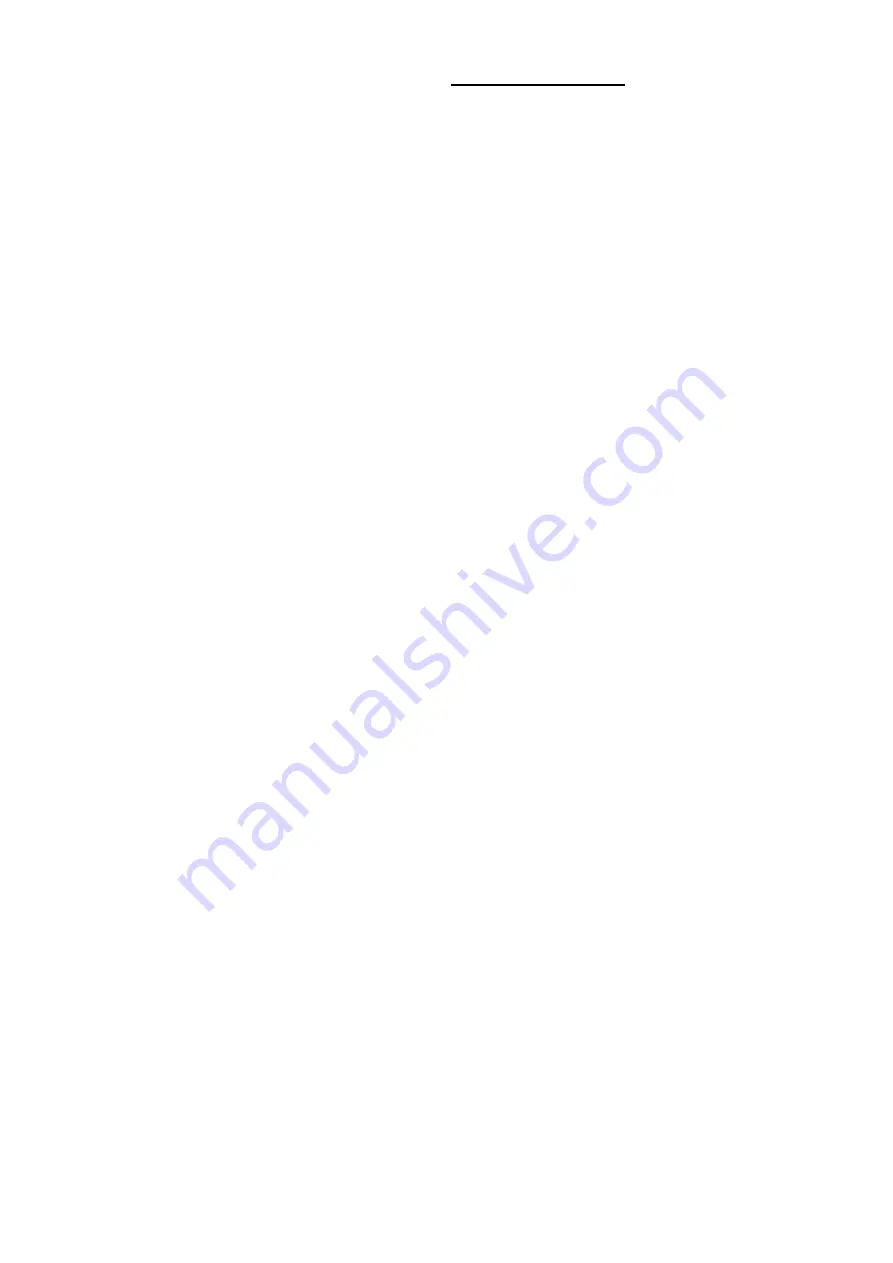
HAMWORTHY HEATING LTD
8
SHAFTESBURY HE
500001049/N
Where the system is operating on a DT of 20°C, care
should be taken to ensure that the return temperature
does not fall below 50°C.
8.9.2 Water Flow Controls
Any external mixing valve/shunt pump or similar
controls should
ALWAYS ENSURE
that the minimum
water flow rate as shown in Figure 3.1. is maintained.
8.9.3 Frost Protection
Consideration should be given to fitting a frost
thermostat set at approximately 4°C.
8.10 Unvented Systems
See Figure 16.1 for typical layout of a Unvented
(Pressurised) Hot Water System. For system design
refer to
BS 7074 Part 2.
In order to correctly size a pressurisation unit for any
heating system certain parameters are required. These
are:-
1)
Static height of highest component in system
(metres).
2)
System volume - if it is not known a general rule of
thumb of 10 litres/kW of installed boiler power can be
used.
3)
Maximum flow temperature (°C).
4)
Maximum system hot working pressure, generally
given in bar g.
From the above information Hamworthy Heating can
size the pressurization unit and also the expansion
vessel required. Care must be taken in sizing expansion
vessels to ensure maximum acceptance factors are not
exceeded. Normally manufacturers of vessels impose
a limit of 0.5. This value must not be exceeded at any
time during the operation of the boiler: this includes the
over pressure condition should a safety valve lift.
Consideration should also be given to sizing of the
safety valve(s) in the system. See
BS 6759
: Part 1, for
information. See also
BS 6880
: Part 1 for design
considerations.
8.11 Modular Boiler Control Schemes
For modular boiler installations, Hamworthy Heating
can supply a unique boiler management control system
called the ‘Marshall HE’. This system comprises: a wall
mounted master control unit, which houses the main
interface processor and will control upto 8 stages. For
further information, contact Hamworthy Heating for
details.
9.0
ELECTRICAL SUPPLY
WARNING: THIS APPLIANCE MUST BE EARTHED
9.1 Site Wiring
Wiring external to the boiler must be installed in
accordance with the I.E.E Regulations and any local
regulations which apply. Wiring must be completed in
heat resistant cable. (For size, refer to the Technical
Instructions supplied by the burner manufacturer). The
boiler control panel requires a 230V, single phase 50
Hz supply.
The burner requires either a single or 3 phase
supply dependant upon model type and size, and
should be wired in accordance with the instructions
provided by the burner manufacturer.
Fuse ratings for individual boilers are marked on the
appliance data plate. The control panel is supplied
with flying lead and plugs for direct connection to
corresponding sockets supplied with the burner.
Should non-standard connecting wiring be
necessary due to particular burners or contract
conditions, space is provided in Appendix C of
these instructions for a wiring diagram to be
included.
The method of connection to the mains electricity
supply must facilitate complete electrical isolation of the
single boiler/battery with a contact separation of at least
3 mm in all poles.
The appliance must be isolated from the mains
electricity supply in the event of electric arc welding
being carried out on any connecting pipework.
A mains isolator must be provided adjacent to the boiler
in a readily accessible position. The supply should only
serve the boiler.
NOTE!
Volt free contact electrical
supplies must also be isolatable where fitted (see note
in control panel). Further details regarding connection
to the electricity supply are given in
BS EN 60335, Part
1 or BS 3456, Part 201
.
9.2 Indication Signals and Volt Free Contacts
Optional control panels are available with v.f.c. contacts
to enable external indicator lights or alarms to derive
signals for normal run, overheat and lockout.
Note:-
These external circuits
MUST
be isolated before
any service or maintenance procedures are carried out.