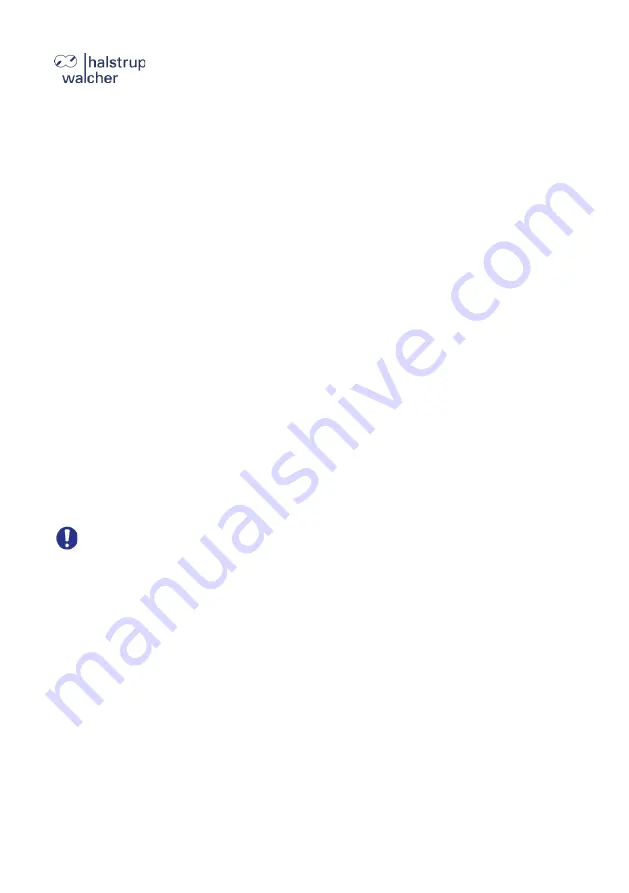
Functions
7100.006514_Bus description_PSD4xx_EC_F_EN
34
2022-12-12
7)
If the user wants to avoid any automatic adjustment of values when setting the parameters
for the drive, the optimum order for sending the parameters is as follows:
a)
Direction of rotation (SDO #202C)
Positioning scaling, numerator (SDO #2010)
Positioning scaling, denominator (SDO #2011)
b)
Reference value (SDO #2004)
c)
Upper mapping end (SDO #2028)
d)
Positioning window (SDO #2006)
Length of loop (SDO #201F)
8)
To save the settings permanently in EEPROM write a 1 in SDO #204F.
Saving can take up to 1 second.
Reference value (SDO
#2004):
The referencing process affects all transferred values, i.e., the target value, actual value, upper
mapping end and upper and lower limits.
There are two ways of setting the referencing value:
1)
Directly
– by writing the referencing value in SDO #2004.
2)
Indirectly
– by writing an actual value to SDO #2003. This makes it possible to assign any
“true” actual value to the current, physical actual value. The resulting difference is then the
referencing value. This value will immediately be included in calculations for each transferred
value and can also be read under SDO #2004.
If the reference value is changed, the target value, actual value, upper mapping end and the
upper and lower limits will be recalculated.
Note:
Removal of the supply voltage to the
motor
has no effect on the internal
measurement system.