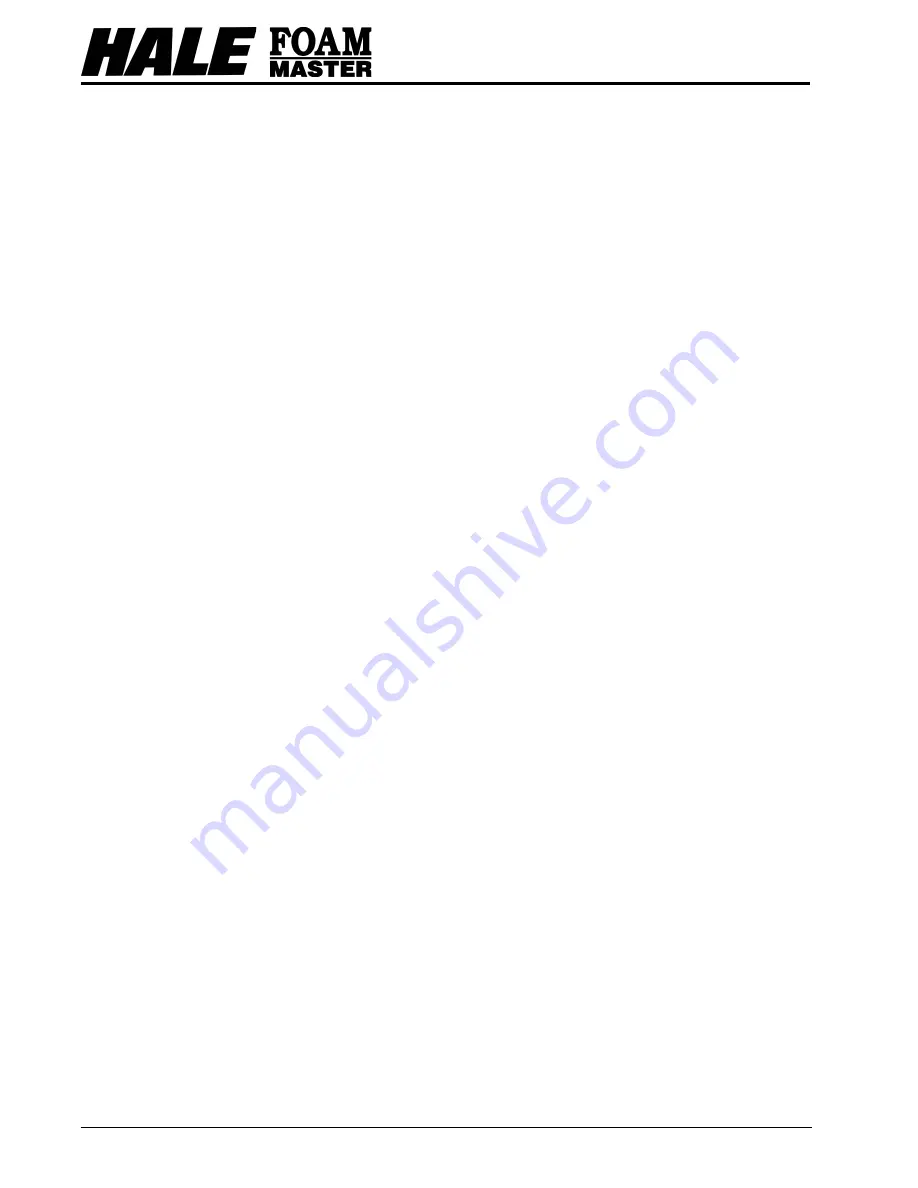
ΙΙ
-48
ROTARY GEAR PUMP
ELECTRONIC FOAM PROPORTIONING SYSTEM
Section
ΙΙ
ΙΙΙΙ
ΙΙ
ΙΙ
: Installation
10. Drain water from foam tanks and
concentrate lines and return the bypass
valve to the
INJECT
position.
11. Verify operation of and calibrate
flowsensor(s) as required using
flowsensor calibration procedures in the
user calibration section.
This completes the Hale FoamMaster system
operation checks that can be
accomplished at the system installer facility.
Foam pump feedback calibration along
with setting of user specified default
simulated flow and concentrate injection
rates should be accomplished upon
delivery to the end user using actual end
user specified foam concentrates and
default values.