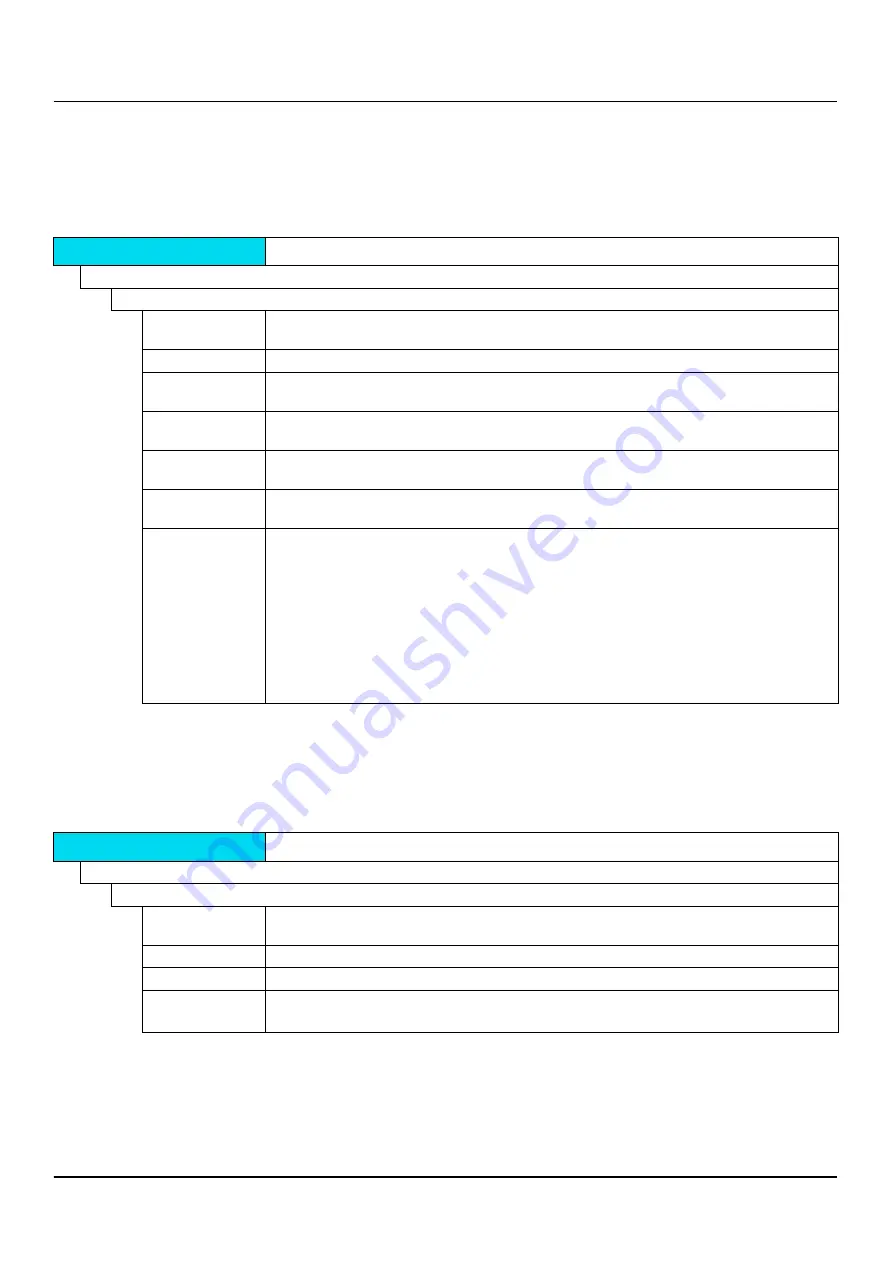
Operation
39
5.7 Output signals
The controller has two independent analogue current outputs (current output 1
and current output 2). The following table provides an overview of all possible
settings to suit your requirements.
Example:
Output range 0.000-2.00 FNU on current output 1 from 4-20 mA
SYSTEM SETUP
OUTPUT SETUP
SELECT OUTPUT 1 or 2
SELECT
SOURCE
Using the Enter key open a list with all the sensors connected and choose the sensor with the
measured values that are to be output.
PARAMETER
Mark one of the parameters listed and press Enter.
SET FUNCTION
The current measured value is output using LINEAR; using PID CONTROL the SC100
operates like a PID controller.
SET TRANSFER
Substitute value to be output instead of the actual measured value during a calibration, fault or
when the Maint. Proc. menu is open.
RESPONSE TIME
Measured value taken over an adjustable interval from 0-120 s to apply damping to the current
output (factory setting: 0 s)
0 / 4...20 mA
Output of the measured values from 0-20 mA or from 4-20 mA (definition of the measuring
range limits using ACTIVATION)
ACTIVATION
If you have selected LINEAR under SET FUNCTION, you can define the upper and lower value
for the output range for the current output.
You can configure the PID CONTROL:
1. Choose either AUTO or MANUAL for SET MODE
2. Set the PHASE to DIRECT or REVERSE.
3. SET SETPOINT that is to be used for the control.
4. Enter the PROP. BAND
5. Enter the integration time (in min) under INTEGRAL.
6. Enter the differentiation time (in min) under DERIVATIVE.
SYSTEM SETUP
OUTPUT SETUP
SELECT OUTPUT 1 or 2: OUTPUT 1
SELECT
SOURCE
ULTRATURB (Sensor 1 or Sensor 2 depending on configuration)
SET FUNCTION
LINEAR
0 / 4...20 mA
4-20 mA
ACTIVATION
0 mA = 0.000 FNU (lower value for the output range)
20 mA = 2.00 FNU (upper value for the output range)
客服:400 688 9809