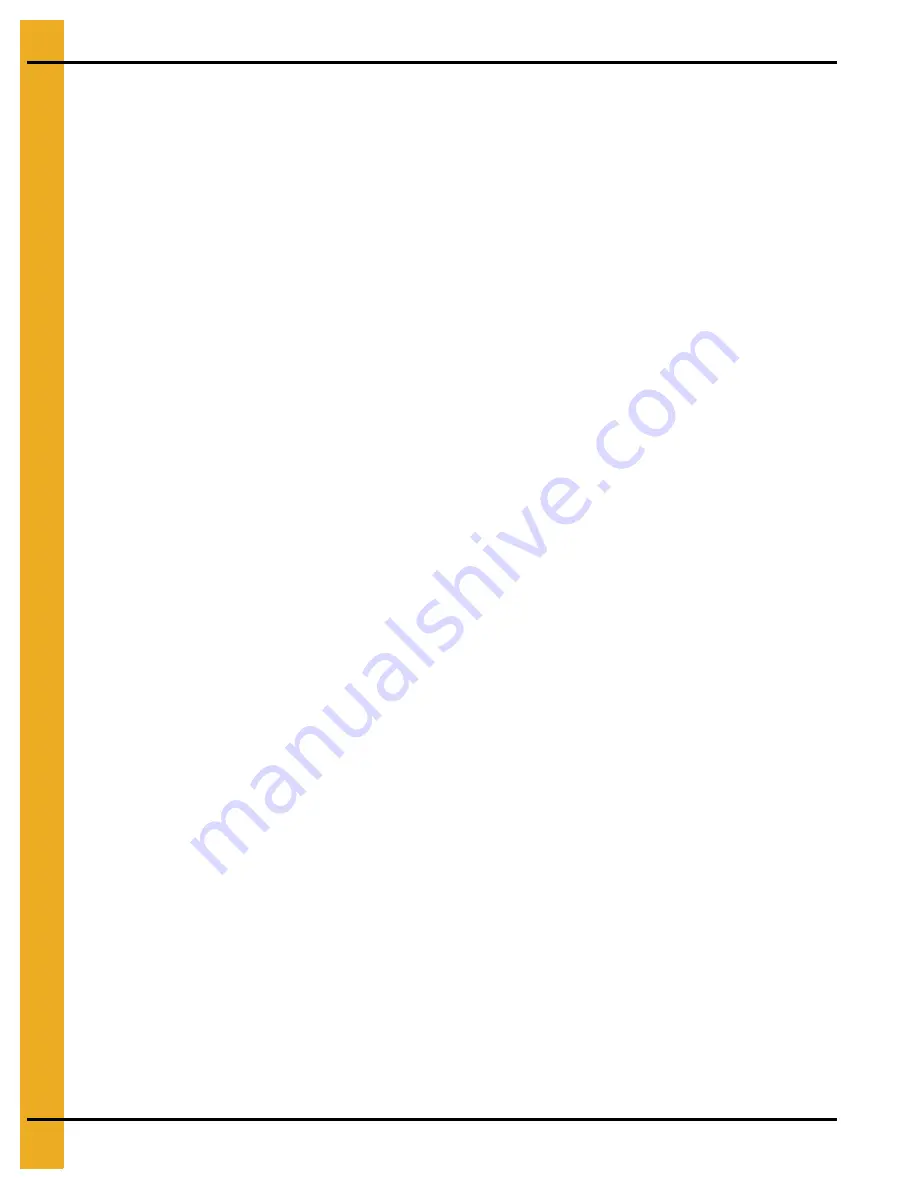
4. Control Panel
14
PNEG-696
TopDry Series 2000 Autoflow
Fan Switch
This switch controls the operation of the main drying fan(s). The switch illuminates when the Air switch
located in the sidewall next to the master drying fan senses an increase in static pressure and closes.
In the Autobatch mode, the main drying fan(s) shut off automatically in the dump cycle. When placed in
the “OFF” position, the main drying fan(s) will not run. When placed in the “ON” position, the main drying
fan(s) come ON and stay ON when the dryer is running.
Heater Switch
This switch controls the operation of the burner(s). The switch illuminates when the burner is ON. When
the burner is on small lights above and below the Heater switch indicate if the burner(s) are in high-fire or
low-fire. In the Autobatch mode, the burner(s) shut off automatically in the cool and dump cycle. When
placed in the “OFF” position, the burner(s) will not fire. When placed in the “ON” position, the burner(s) fire
anytime the main drying fan(s) are running.
Dump Switch
This switch controls the operation of the linear actuator housed in the actuator control box. The switch
illuminates when the linear actuator is moving. When placed in the “MANUAL CLOSE POSITION” the
linear actuator in the actuator control box retracts-raising the dump chutes. When placed in the “AUTO”
position, the linear actuator extends at the beginning of the dump cycle-lowering the dump chutes and
retracts at the end of the dump cycle-raising the dump chutes. When placed in the “MANUAL OPEN”
position the linear actuator extends lowering the dump chutes.
Dry and Hold Switch
When placed in the “ON” position, the grain in the drying chamber will not be dumped into the storage
chamber at the end of the dry cycle and the dryer will stop and cool for as long as the cool timer is set.
If no cooling is desired set to 0. This switch can be used to hold the last batch of grain in the drying
chamber and stop the dryer. When placed in the “OFF” position, the dryer will operate normally. The switch
illuminates when placed in the “ON” position.
Dryer Power Start Switch
This switch starts and operates the dryer based on switch settings. The switch illuminates when the dryer
is running. The Dump switch is disabled after this switch has been pushed.
Dryer Power Stop Switch
This switch stops all dryer functions. If an automatic dryer shut down occurs, first determine and correct
the cause of the shut down. Then, press the Dryer Power Stop switch to reset the dryer before starting.