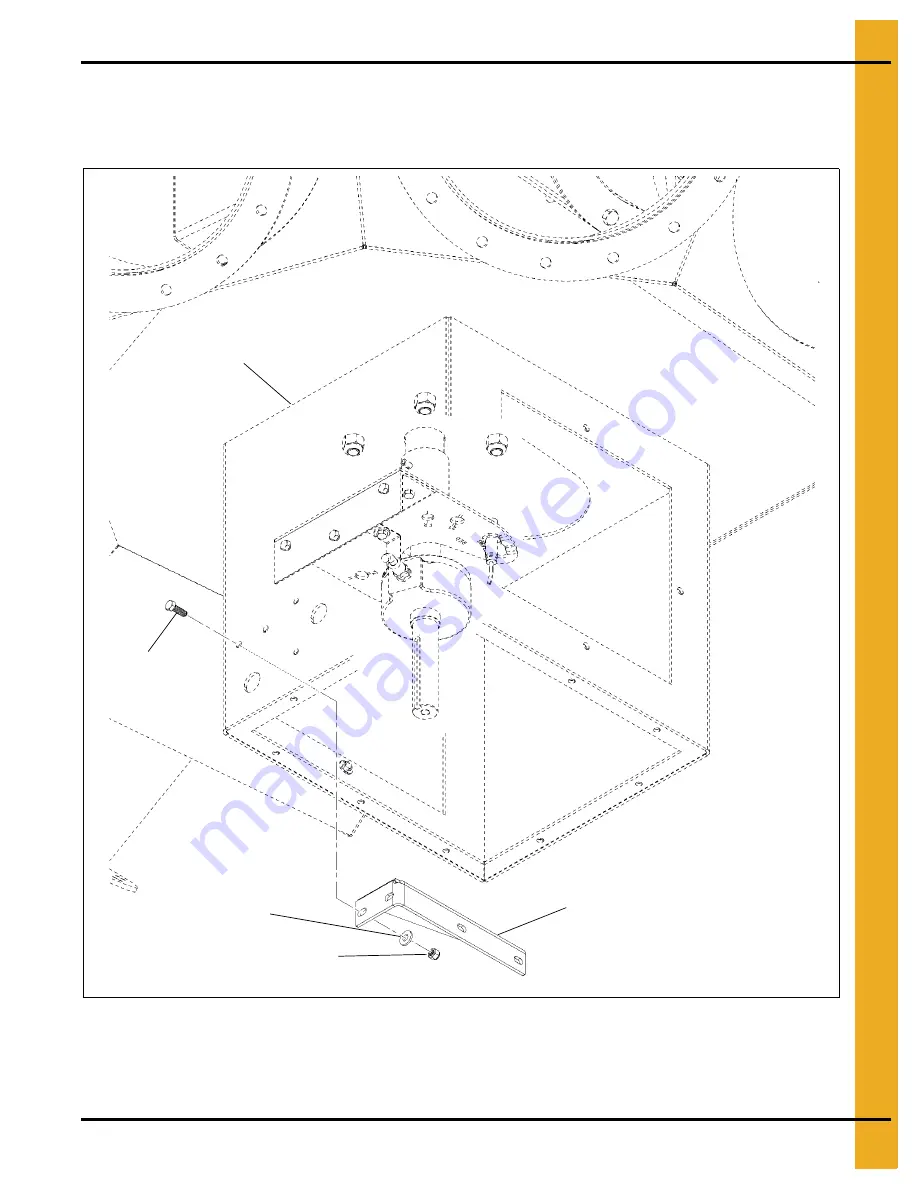
2. Installation
PNEG-1813
Electronic Distributor Control
19
Motor Mounting Bracket Installation
Install the motor mounting bracket (DEC0003) to the enclosure (DEC0005) using two 1/4”-20 x 3/4” HHCS
bolts (S-1429), 1/4” washers (S-2126), and 1/4”-20 nylock nuts (S-7025) as shown in
Figure 2K
Motor Mounting Bracket
1/4” Washer (S-2126)
1/4”-20 Nylock nut
(S-7025)
1/4”-20 x 3/4” HHCS
Bolt (S-1429)
Motor mounting
bracket (DEC0003)
Enclosure (DEC0005)
Summary of Contents for PNEG-1813
Page 2: ...2 PNEG 1813 Electronic Distributor Control ...
Page 4: ...Table of Contents 4 PNEG 1813 Electronic Distributor Control ...
Page 46: ...3 Operation Procedures 46 PNEG 1813 Electronic Distributor Control NOTES ...
Page 47: ...PNEG 1813 Electronic Distributor Control 47 4 Parts Distributor Assembly ...
Page 48: ...4 Parts 48 PNEG 1813 Electronic Distributor Control NOTES ...
Page 52: ...5 Troubleshooting 52 PNEG 1813 Electronic Distributor Control NOTES ...
Page 56: ...6 Schematic and Wiring Diagrams 56 PNEG 1813 Electronic Distributor Control NOTES ...