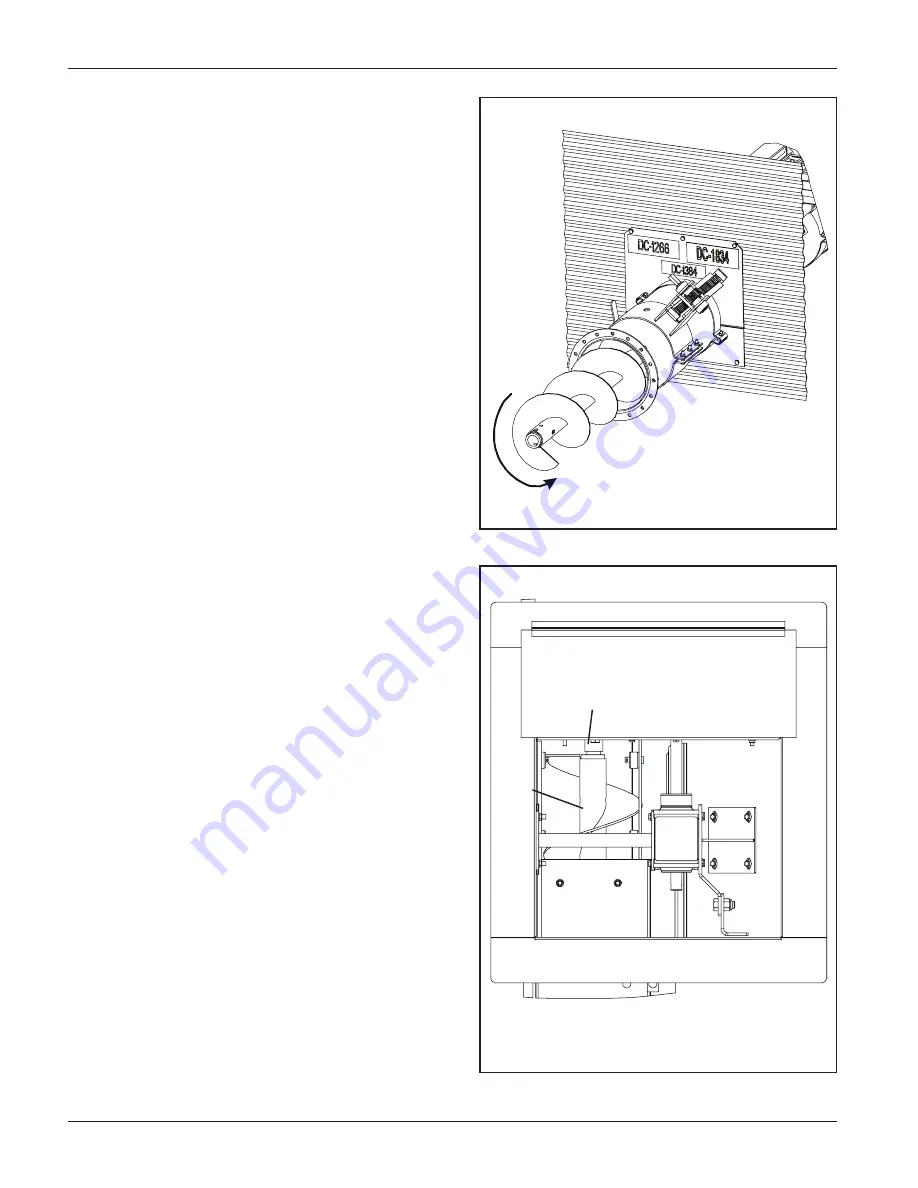
22
PNEG-1421
Direct Gear Drive Bin Sweep Auger
INSTALLATION
9. Installing the Unload Tube
Flight
A. Begin by removing the tube end cap if you have not
already done so.
B. Insert the Flight into the tube with the square bushing
end facing the center well and the round bushing end
facing the discharge end of the tube. (See Figure 9-A)
C. When the flight is approaching the clutch shaft it will be
necessary to rotate flighting counter-clockwise in order
to get it to seat properly on the squared clutch shaft.
When the flight is properly seated the flight should be
entirely inside the unload tube. It may be necessary to
pull the flight out a small amount and attempt this step
multiple times in order to seat the flight properly. (See
Figure 9-B)
D. On the initial install with an empty bin, the installer
might want to open the center well and enter the bin to
check and see that the flight is seated. Once they have
seen that it has seated they will know the proper
position the flight is in on the discharge end when it has
seated properly. (See Figure 9-A)
Fig. 9-A
Fig. 9-B
Clutch Shaft
Flight
Summary of Contents for PNEG-1421
Page 37: ...37 PNEG 1421 Direct Gear Drive Bin Sweep Auger PART LISTS PARTS SECTION...
Page 39: ...39 PNEG 1421 Direct Gear Drive Bin Sweep Auger PART LISTS Center Well Parts...
Page 45: ...45 PNEG 1421 Direct Gear Drive Bin Sweep Auger PART LISTS 8 Rack Pinion 10 Rack Pinion 3...
Page 49: ...49 PNEG 1421 Direct Gear Drive Bin Sweep Auger PART LISTS Reduction Wheel Parts...
Page 50: ...50 PNEG 1421 Direct Gear Drive Bin SweepAuger NOTES...