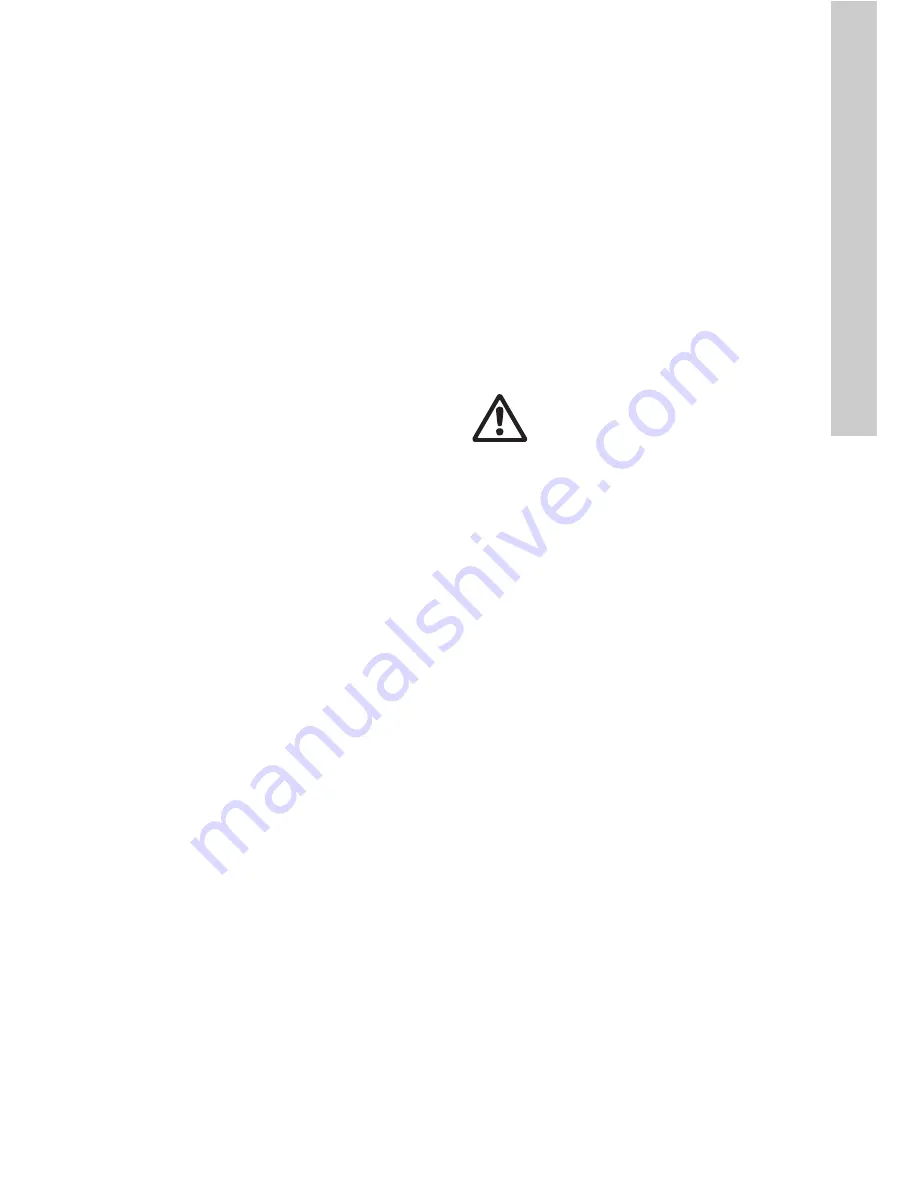
English (GB)
13
2.3 Qualification and training of personnel
The personnel responsible for the operation,
maintenance, inspection and installation must be
appropriately qualified for these tasks. Areas of
responsibility, levels of authority and the supervision
of the personnel must be precisely defined by the
operator.
If the personnel do not have the necessary
knowledge, the necessary training and instruction
must be given. If necessary, training can be
performed by the manufacturer/supplier at the
request of the operator of the pump. It is the
responsibility of the operator to make sure that the
contents of this manual are understood by the
personnel.
2.4 Risks when safety instructions are not
observed
Non-observance of the safety instructions may have
dangerous consequences for the personnel, the
environment and the pump. If the safety instructions
are not observed, all rights to claims for damages
may be lost.
Non-observance of the safety instructions may lead
to the following hazards:
•
failure of important functions of the pump/system
•
failure of specified methods for maintenance
•
harm to humans from exposure to electrical,
mechanical and chemical influences
•
damage to the environment from leakage of
harmful substances.
2.5 Safety-conscious working
The safety instructions in this manual, applicable
national health and safety regulations and any
operator internal working, operating and safety
regulations must be observed.
2.6 Safety instructions for the
operator/user
Hazardous hot or cold parts on the pump must be
protected to prevent accidental contact.
Leakages of dangerous substances (e.g. hot, toxic)
must be disposed of in a way that is not harmful to
the personnel or the environment. Legal regulations
must be observed.
Damage caused by electrical energy must be
prevented (for more details, see for example the
regulations of the VDE and the local electricity
supply company).
2.7 Safety instructions for maintenance,
inspection and installation work
The operator must ensure that all maintenance,
inspection and installation work is carried out by
authorised and qualified personnel, who have been
adequately trained by reading this manual.
All work on the pump should only be carried out
when the pump is stopped. The procedure described
in this manual for stopping the pump must be
observed.
Pumps or pump units which are used for media that
are harmful to health must be decontaminated.
All safety and protective equipment must be
immediately restarted or put into operation once
work is complete.
Observe the points described in the initial start-up
section prior to subsequent start-up.
2.8 Unauthorised modification and
manufacture of spare parts
Modification or changes to the pump are only
permitted following agreement with the
manufacturer. Original spare parts and accessories
authorised by the manufacturer are safe to use.
Using other parts can result in liability for any
resulting consequences.
2.9 Improper operating methods
The operational safety of the supplied pump is only
ensured if it is used in accordance with
section
1. General information
. The specified limit
values must under no circumstances be exceeded.
2.10 Safety of the system in the event of
a failure in the dosing system
DDI 209 dosing pumps are designed according to
the latest technologies and are carefully
manufactured and tested. However, a failure may
occur in the dosing system. Systems in which dosing
pumps are installed must be designed in such a way
that the safety of the entire system is still ensured
following a failure of the dosing pump. Provide the
relevant monitoring and control functions for this.
Warning
Electrical connections must only be
carried out by qualified personnel!
The pump housing must only be
opened by personnel authorised by
Grundfos!