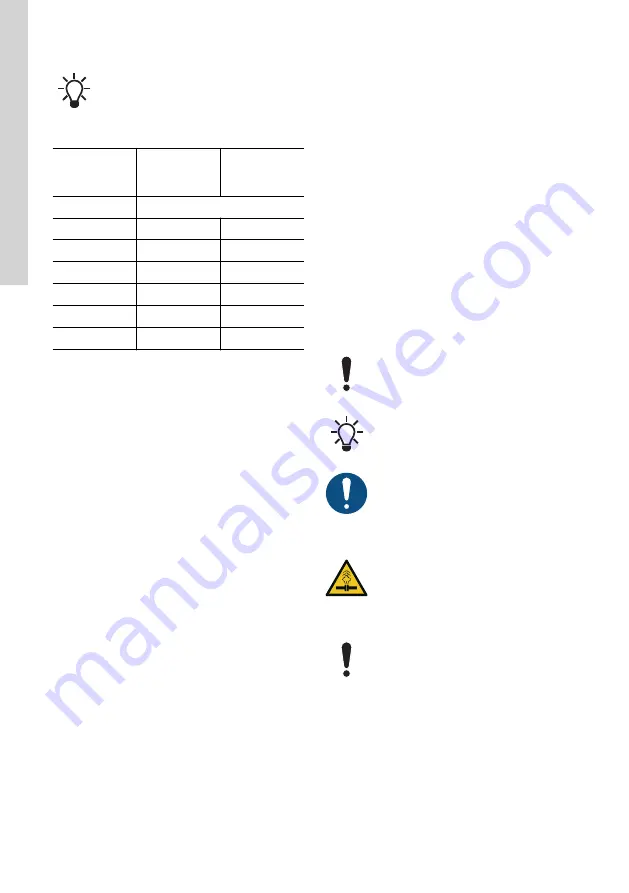
If the pump is used in highly abrasive or
corrosive matter, the maintenance
intervals should be reduced.
Tightening torques
A2/A4,
Hardness
class 70
A2/A4,
Hardness
class 80
DIN912 / DIN933
M6
7 Nm
11.8 Nm
M8
17 Nm
28.7 Nm
M10
33 Nm
58 Nm
M12
57 Nm
100 Nm
M16
140 Nm
245 Nm
M20
273 Nm
494 Nm
8.2 Test insulation resistance
To check the insulation resistance, proceed as
follows:
1.
Disconnect the power supply cable.
2.
Measure the resistance with an insulation tester.
Measuring DC voltage is 1000 V.
During commissioning, the insulation resistance of 20
MΩ must be met or exceeded. For additional
measurements, the value must be larger than 2 MΩ.
Low insulation resistance indicates that moisture may
have penetrated to the cable and/or the motor
insulation. Do not connect the pump, contact
Grundfos.
8.3 Replacing the impeller
The stationary wear ring determines the gap between
the impeller and the inlet. If this gap is too big, the
pump performance decreases and may lead to
impeller jams. The wear ring can be replaced, which
reduces the wear on the inlet and the
impeller, and consequently the expense for spare
parts.
1.
Loosen and remove the screws on the seal
housing.
2.
Remove the pump housing from the seal
housing.
3.
Place the pump housing on a secure base.
4.
Hold the impeller steady with a suitable tool, and
remove the impeller fastener.
5.
Remove the impeller from the shaft.
6.
Clean the shaft.
7.
Attach a new impeller to the shaft. Make sure the
sliding surfaces remain undamaged.
8.
Hold the impeller steady with a suitable tool, then
insert a new impeller fastener and tighten it.
9.
Assemble the pump housing with the seal
housing.
10. After the assembly is finished, check that the
impeller can be turned by hand.
8.4 Ball bearing maintenance
Check the shaft for noisy or heavy operation by
turning the shaft by hand. Replace defective ball
bearings.
A general overhaul of the pump is usually required in
case of defective ball bearings or poor motor function.
This work must be carried out by Grundfos or an
authorised service workshop.
8.5 Oil check and change
Only use original parts.
Use Shell Ondina X420 oil or equivalent
type.
Dispose of used oil must comply with local
regulations
CAUTION
Pressurised system
Minor or moderate personal injury
‐
The oil chamber may be under
pressure. Loosen the screws carefully
and do not remove them until the
pressure has been completely relieved.
After 3000 operating hours or at least once
a year, change the oil in the oil chamber as
described below. If the shaft seal has been
replaced, the oil must be changed.
When the pump is new or the shaft seal is replaced,
check the oil level and water content after one week
of operation. If there is more than 20 % extra liquid
(water) in the oil chamber, the shaft seal is defective.
The table below states the quantity of oil in the oil
chamber:
16
English (GB)
Summary of Contents for AP100 Series
Page 2: ......