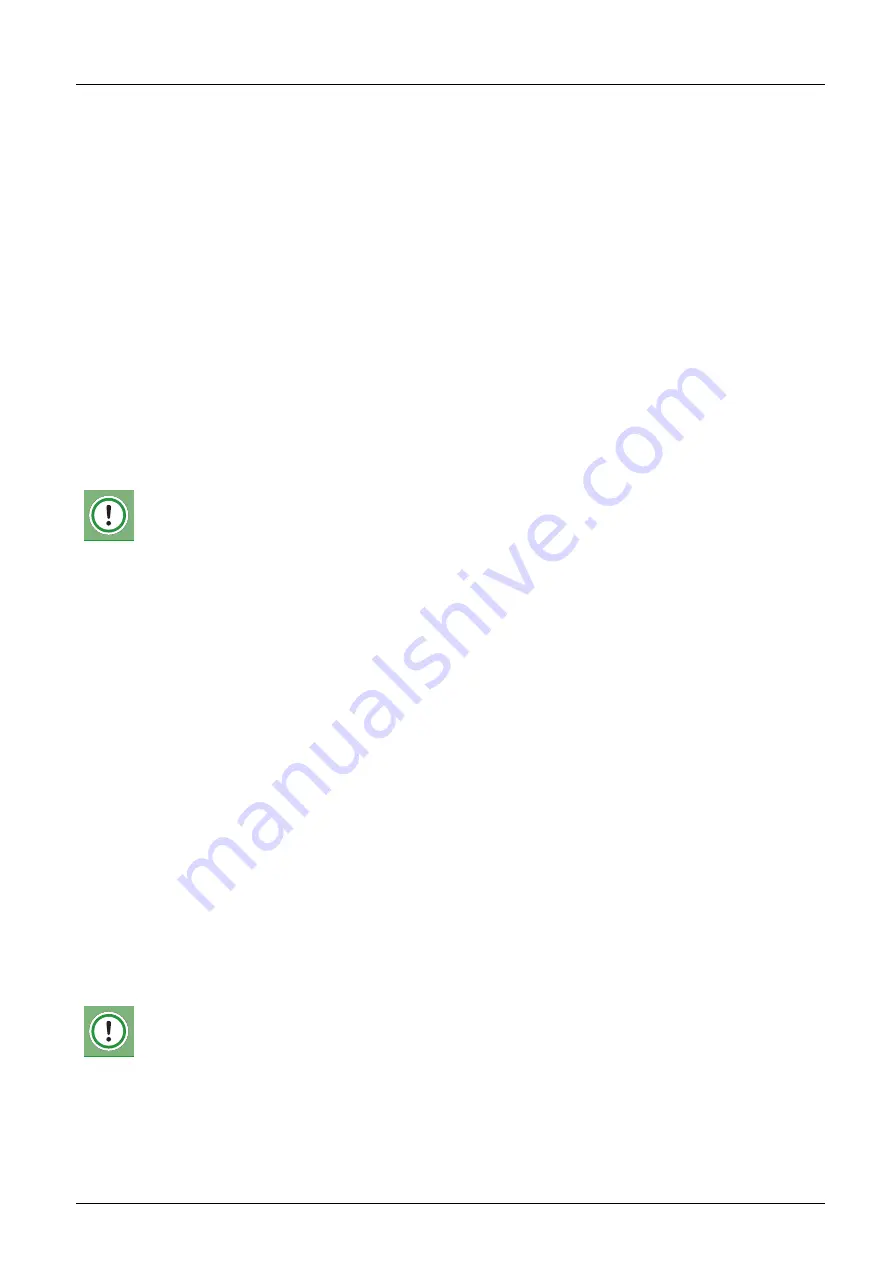
Automatic Greasing System
TriPlus Trailer
Installation
45
Date of
is
sue :
Sept
e
m
ber
2
012
F212157R02
Removable couplings:
a. Clamp the sleeve in a bench vice.
b. Turn the line into the sleeve, to end of the sleeve (counter-clockwise!).
c. Turn the line backward 1/4 to 1/2 turn.
d. Apply oil or grease to the pillar, the sleeve and the inside of the line.
e. Turn (clockwise) the grease line pillar in the sleeve, untill it is in position without tension.
f. Mount the coupling at the other end of the grease line in a similar way.
Press couplings (applied with a simple hand-operated press) for high-pressure line
DN4 (F115307):
a. Slide the press sleeve completely over the end of the grease line, so that the line fills the
sleeve completely.
b. Slide, use some oil if necessary, the pillar or the required coupling pin into the end of the
grease line untill the pillar is completely in the grease line.
c. Place the assembly in the press in such a manner that a little piece of the sleeve remains
visible at both sides. Apply pressure until the lever of the hand-operated press reaches its
end-stop.
d. Mount the coupling at the other end of the grease line in a similar way.
Press couplings (applied with a hydraulic press) for high-pressure grease line DN6
(F113422):
a. Check that the press is fitted with the correct type of press blocks, and the set press
diameter. The correct press diameter for this type of grease line is 14,6 mm.
b. Slide the sleeve over the end of the grease line, until it covers the line completely.
c. Slide, use some oil if necessary, the pillar or the required coupling pin into the end of the
grease line until the pillar is completely in the grease line.
d. Pull the sleeve back slightly until it touches the outside edge of the coupling pin. While
doing this, ensure that the pillar remains in place and is not pressed out of the grease line.
e. Place the assembly into the press and press the sleeve to the required diameter (14,6 mm).
f. Check the resulting diameter by measuring it (between ridges that may have formed).
g. Mount the coupling at the other end of the grease line in a similar way.
3.
Remove any burrs and other remnants produced by cutting the line, and clean the grease line
by blowing it through. Check that the line is free of obstructions and check it for internal
damage behind the couplings (the inner lining may have been upset).
4.
Fill the line with grease. Either use a pneumatic or hand-operated grease gun.
5.
Install the grease line and fix it in place with tie-wraps or clamps. Do not yet connect the
primary grease line(s) to the output port(s) of the pump unit, if you want to use the
pneumatic or hand-operated grease gun to de-aerate the system.
ATTENTION
A simple hand-operated press that can be placed in a bench vice is used with DN4 high-pressure
lines. The thin-walled sleeve of the couplings for this type of grease line must be pressed exactly
in the middle, so that small pieces of unpressed sleeve remain on both sides. This note of attention
does not apply to sleeves meant for use with a hydraulic press. Those types of sleeves must be
pressed over their whole length.
ATTENTION
Always use steel cutting rings when using metal grease lines and couplings.
Summary of Contents for TriPlus Trailer
Page 57: ......