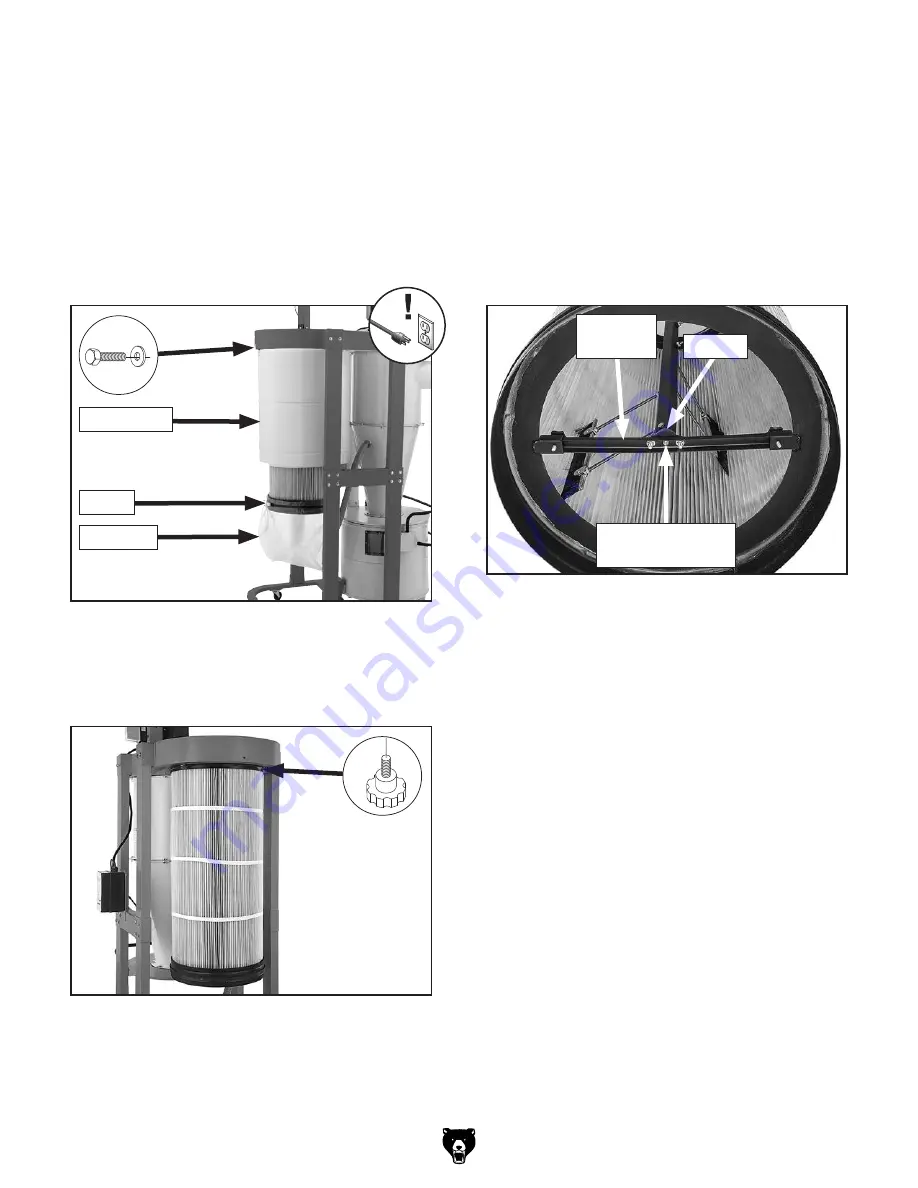
Model G0849 (Mfd. Since 01/19)
-45-
Figure 78. Location of filter bag and filter cover.
Filter Bag
Filter Cover
x 3
Clamp
6. Twist canister counterclockwise, then lower it
past filter brush assembly to remove.
7. Vacuum loose dust from inside impeller
housing and on machine.
8. To install canister filter, lift it around filter
brush assembly. While lifting canister filter,
have assistant work below to align filter brush
assembly spindle with bearing in mounting
bar (see
Figure 80).
Figure 80. Alignment points for filter brush
assembly and canister filter.
Mounting
Bar
Filter Brush
Assembly Spindle
Bearing
9. With canister filter sitting flush against impel-
ler housing, twist canister filter clockwise onto
knob bolt threads.
10. Tighten (3)
5
⁄
16
"-18 x 1" knurled knob bolts to
secure canister filter.
11. With help from assistant, place filter cover
under canister filter, then lift cover and attach
to impeller housing with (3)
5
⁄
16
"-18 x
3
⁄
4
" hex
bolts and (3)
5
⁄
16
" fender washers.
12. Attach new filter bag to bottom of canister
and secure bag with clamp.
5. Loosen (3)
5
⁄
16
"-18 x 1" knurled knob bolts
that secure canister filter to impeller housing
(see
Figure 79).
Figure 79. Canister filter fasteners.
x 3
3. Release clamp, then remove filter bag (see
Figure 78).
IMPORTANT: To contain wood dust and
minimize risk of exposure, firmly tie bag
closed for disposal.
4. With help from an assistant, remove (3)
5
⁄
16
"-
18 x
3
⁄
4
" hex bolts and (3)
5
⁄
16
" fender washers
securing filter cover to impeller housing, then
lower and remove cover (see
Figure 78).
Summary of Contents for G0849
Page 54: ...52 Model G0849 Mfd Since 01 19...
Page 56: ......