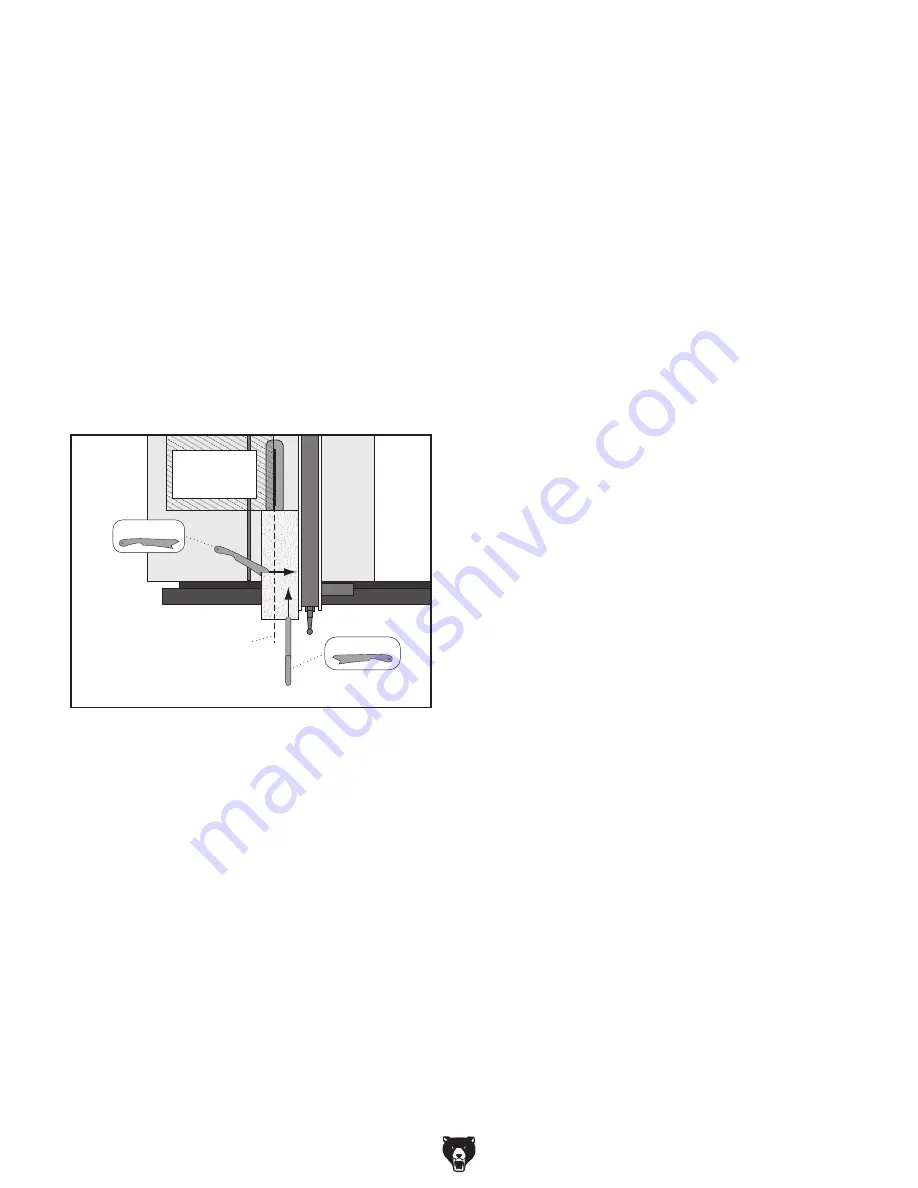
-62-
Model G0699 (Mfd. Since 5/15)
Figure 119. Example of shop-made push stick
used to rip narrow stock.
Feeding
Supporting
Blade
Path
Push Stick
Push Stick
Push Stick
Prohibition
Zone
Feeding: Place the notched end of the push stick
against the end of the workpiece and out of the
blade path. Use steady downward and forward
pressure to push the workpiece into the blade.
Supporting: A second push stick may also
be used with the other hand to apply sideways
pressure on the workpiece to keep it held firmly
against the fence while starting the cut. When
using a push stick in this manner, do not apply
pressure to the workpiece against or behind
the blade (see "Push Stick Prohibition Zone" in
Figure 119). Otherwise, pressure from the push
stick will increase the risk of kickback.
Push sticks should be made of plywood or hard
wood and can be made in a variety of shapes
and sizes. Avoid making push sticks out of mate-
rial that may break under pressure (soft wood or
particle board) or out of material that may damage
the blade during accidental contact (metal).
The push stick must be at least 15
3
⁄
4
" long. The
pattern for making a basic push stick, such as
the one shown in
Figure 118, can be laid out on
a piece of wood and cut out using a bandsaw,
jig saw, or scroll saw. Sand the handle area and
edges to increase comfort and safety.
Using a Push Stick
Figure 119 shows an example of push sticks used
to feed and support a workpiece.
Summary of Contents for G0699
Page 21: ...Model G0699 Mfd Since 5 15 19 5mm Hardware Recognition Chart...
Page 108: ......