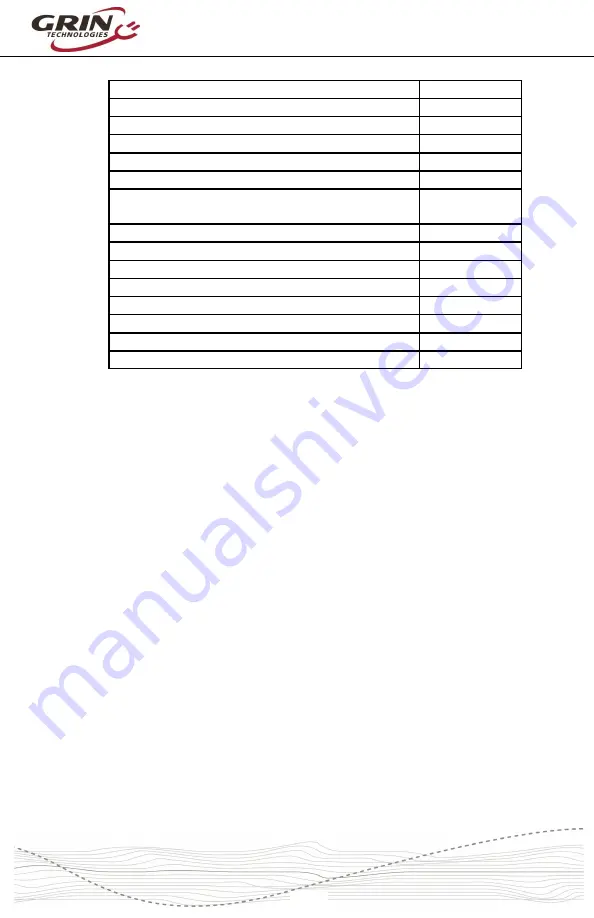
Frankenrunner User Manual
Rev 1.0
Table 1: Effective Pole Pairs of Common DD and Geared Hub Motors
Motor Family
# Pole Pairs
Crystalyte 400, Wilderness Energy
8
BionX PL350
11
Crystalyte 5300, 5400
12
TDCM IGH
16
Crysatlyte NSM, SAW
20
Grin All Axle, Crysatlyte H, Nine Continent,
MXUS and Other 205mm DD Motors
23
Magic Pie 3, Other 273mm DD Motors, RH212
26
Bafang BPM, Bafang CST
40
Bafang G01, MXUS XF07
44
Bafang G02, G60, G62
50
Shengyi SX1/SX2
72
eZee, BMC, MAC, Puma, GMAC
80
Bafang G310, G311
88
Bafang G370
112
For motors not listed, either open the motor to count the magnets pairs (and gear
ratio), or count the number of Hall cycles that take place when you manually turn
the wheel one revolution. You can monitor the number of Hall transitions via the
“Dashboard” tab of the software suite.
Once the “kV” and the “Number of Pole Pair” values are entered, launch the
“Static Test.” This test will produce three short buzzing sounds, and determine
the inductance and resistance of the motor windings. The resulting values will be
shown on the screen.
Next, launch the “Spinning Motor Test” which will cause the motor to rotate at
about half speed for 15 seconds. During this test, the controller will determine the
actual kV winding constant for the hub, as well as the pinout and timing advance
of the Hall sensors if they are present. If the motor spins backwards during this
test, check the box “Flip Motor Spin Direction on Next Autotuning?” and relaunch
the “Spinning Motor Test.”
During the spinning test, the
Frankenrunner
will start the motor in sensorless
mode. If the motor fails to spin and just starts and stutters a few times, adjust the
sensorless starting parameters as described in section 5.5, “Tuning the
Sensorless Self Start,” until the motor is spinning steadily. If the spinning test
detects a valid Hall sequence, the final screen will show the hall offset, and that
the “Position Sensor Type” is “Hall sensor start and sensorless run.”
-11-