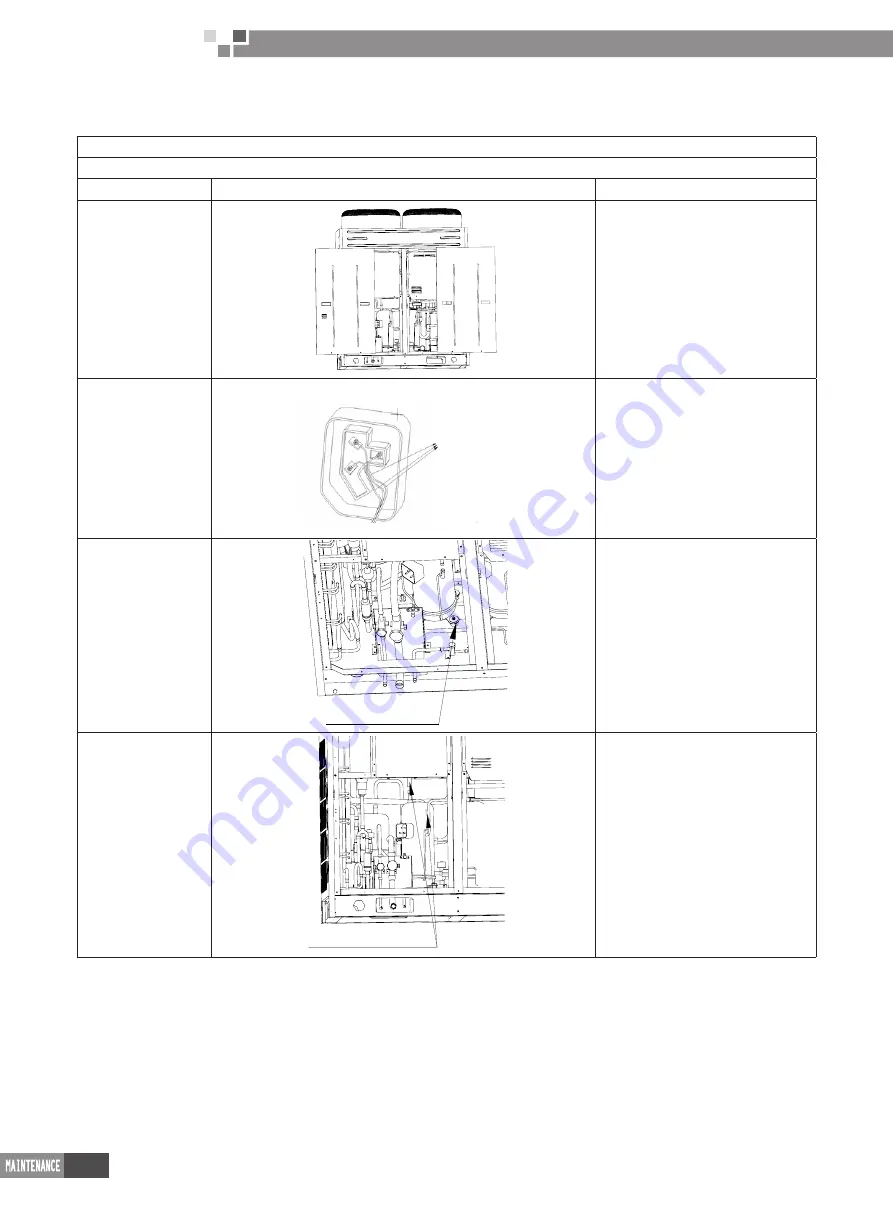
206
DC Inverter Multi
VRF Service Manual
7 DISASSEMBLY AND ASSEMBLY PROCEDURE OF MAIN PARTS
7� 1 Outdoor Unit
Removal and Installation of Compressor
Remark: Before removing the compressor, make sure that there is no refrigerant inside the pipe system and that the power has been cut off.
Step
Illustration
Handling Instruction
1. Remove front panel
● Loosen the 4 screws on the front panel.
● Lift the front panel to remove it.
Note: there are two buckles for the
left and right front panel. Do not
pull the front panel directly. It is
necessary to lift it before pull it.
2. Remove power
cord, electric heater
and discharge
temperature sensor
Mark the power
cable color and
corresponding
terminal,
● Loosen the screw fixing the power cord.
● Disconnect the power cord.
● Pull out the elelctric heater and
discharge temperature sensor
Note: mark the color of the power
cord and corresponding terminal.
3. Remove the fixng
screw of compressor
loosen the four screws
● Loosen the 4 screws
fixing the compressor.
4. Remove the
suction pipe
pull out the exhaust pipe
● Heat the suction and discharge
pipe by gas welding. Then
remove the compressor.
● It is necessary to charge nitrogen for
welding. The pressure of nitrogen is
0.5±0.1kgf/cm2 (abosilute pressure)
● Do not burn the surrounding
matters when heating.
Summary of Contents for CN851W1000
Page 1: ...DCINVERTERMULTIVRFSERVICEMANUAL T1 R410A 50Hz GC201107 CENTRAL AIR CONDITIONERS ...
Page 6: ...DC Inverter Multi VRF Service Manual 1 PRODUCT PRODUCT ...
Page 24: ...DC Inverter Multi VRF Service Manual 19 CONTROL CONTROL ...
Page 92: ...DC Inverter Multi VRF Service Manual 87 INSTALLATION ...
Page 146: ...DC Inverter Multi VRF Service Manual 141 ENGINEERING DEBUGGING ...
Page 171: ...166 DC Inverter Multi VRF Service Manual MAINTENANCE ...
Page 233: ...JF00300207 ...