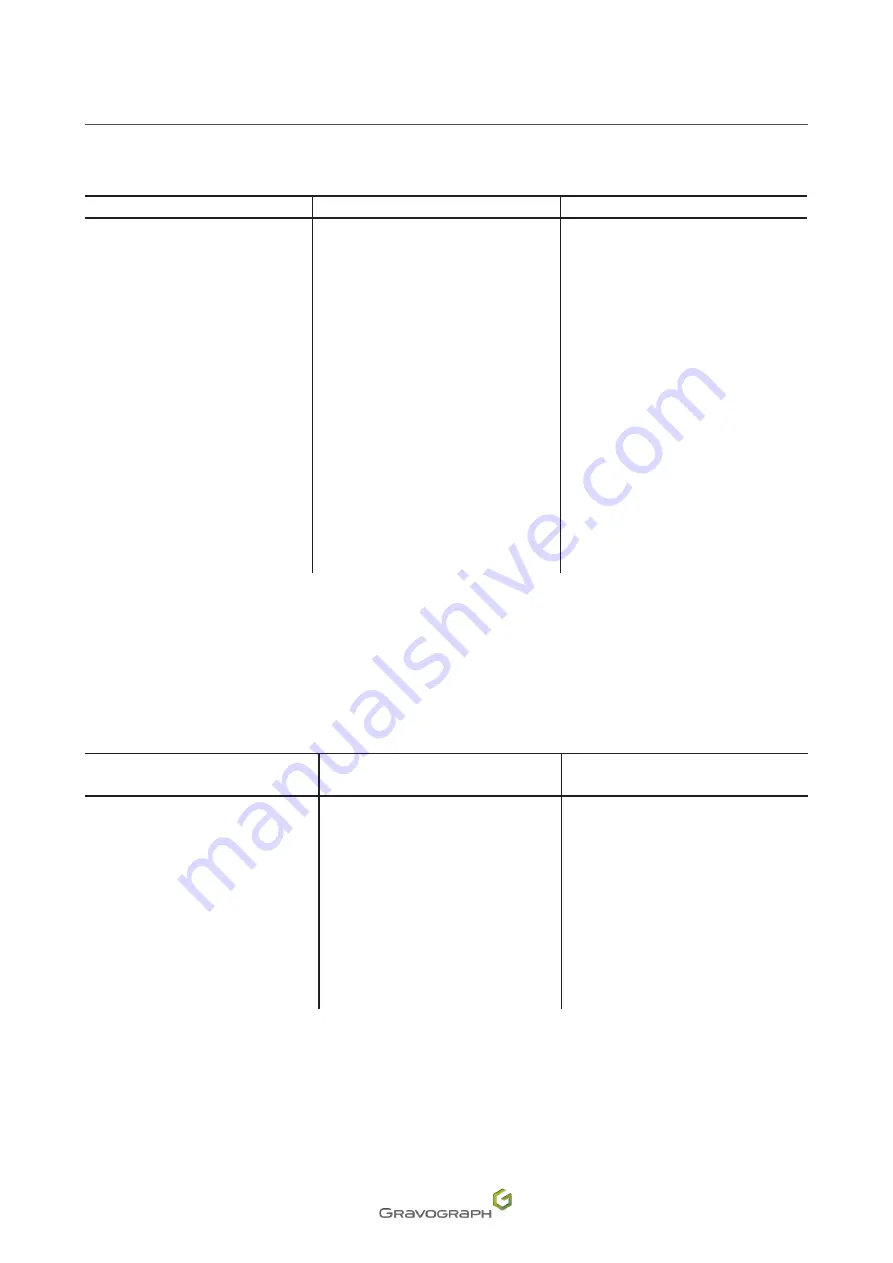
28
M_LS900 Fibre - LS900 Edge_EN_C
Recommendations for installation
4. IT requirements
Hardware
Minimum configuration of the PC
Recommended configuration
Microprocessor
Dual Core
Quad Core
Frequency
2.7 GHz
2.4 GHz
RAM
2 Go / GB
4 Go / GB
Hard disk
3 Go / GB available
6 Go / GB available
DVD: internal drive
16X DVD-ROM
16X DVD-ROM
Mouse
2 button(s)
Windows®-compatible
2 button(s) + thumbwheel -
Windows®-compatible
Keyboard
Windows®-compatible
Windows®-compatible
Port(s)
2 USB port(s) available:
- protection key
- machine
4 USB port(s) available:
- protection key
- machine 1
- machine 2
- machine 3
Graphics card
NVIDIA or ATI Radeon
512 Mo / MB
NVIDIA or ATI Radeon
DX10-compatible - 1 Go / GB
Monitor
17" - 1024 * 768 pixels
22" - 1280 * 1024 pixels
Peripheral(s)
Printer
Twain scanner
The machine is an output peripheral, like a printer.
5.
Software compatibility
Program Laserstyle:
Operating system
Version 32 bits
Version 64 bits
Windows
®
7 SP1 - 8 - 10
Compatible
Compatible
Windows
®
Vista SP2
Compatible
Ccompatible
Windows
®
XP SP3
Compatible
Not compatible
Windows
®
2000
Not compatible
Non-existent
Windows
®
98
Not compatible
Non-existent