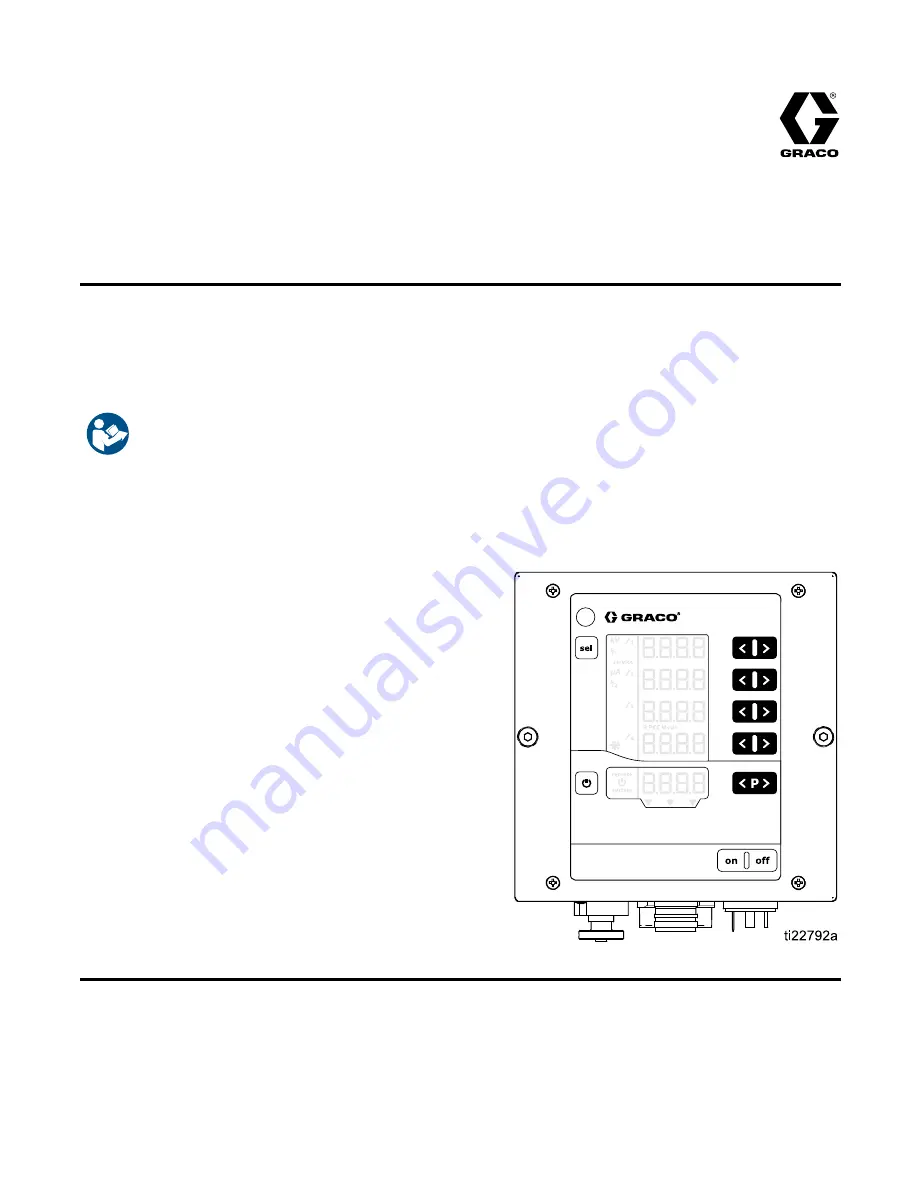
Instructions and Parts
ProBell® Electrostatic Controller
3A3657C
EN
For controlling a ProBell rotary applicator as part of a paint coating system. For professional use only.
Not approved for use in explosive atmospheres or hazardous locations.
Important Safety Instructions
Read all warnings and instructions in this manual and in your
ProBell® Rotary Applicator manual. Save these instructions.
PROVEN QUALITY. LEADING TECHNOLOGY.