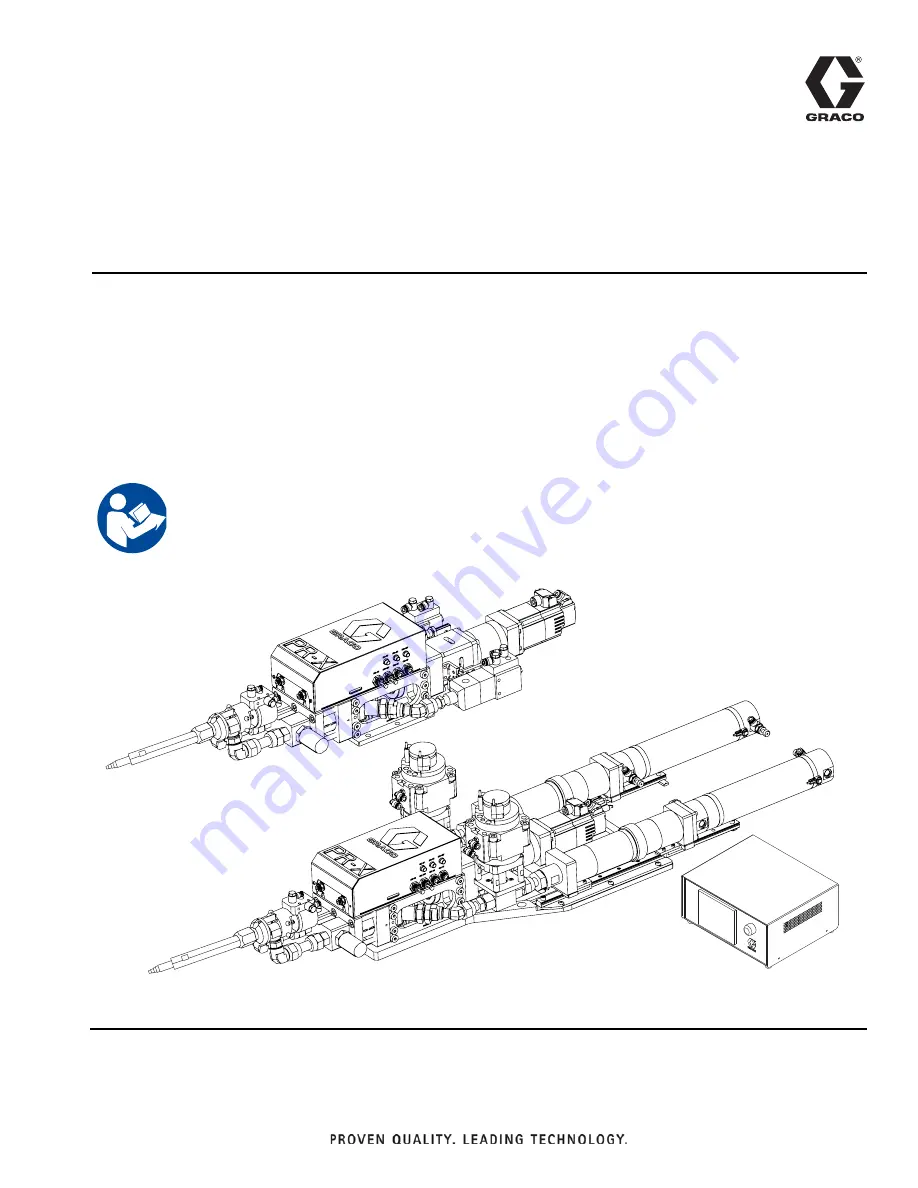
3A7526B
EN
Setup - Operation - Repair
PR-X
Fixed Ratio System
For accurate metering, mixing, and dispensing of two-component materials. For
professional use only.
Not approved for use in explosive atmospheres or hazardous (classified) locations.
1200 psi (8.3 MPa, 83 bar) Maximum Working Pressure
100 psi (0.7 MPa, 7 bar) Maximum Air Inlet Pressure
Important Safety Instructions
Read all warnings and instructions in this
manual before using the equipment.
Save these instructions.
PR-X Machine, Supply
Pump Feed, MD2 Dispense
Valve Direct Shown
PR-X Machine, Cartridge
Feed, MD2 Dispense
Valve Direct Shown
PR-X Control Box
Summary of Contents for 25R128
Page 77: ...Parts 3A7526B 77...