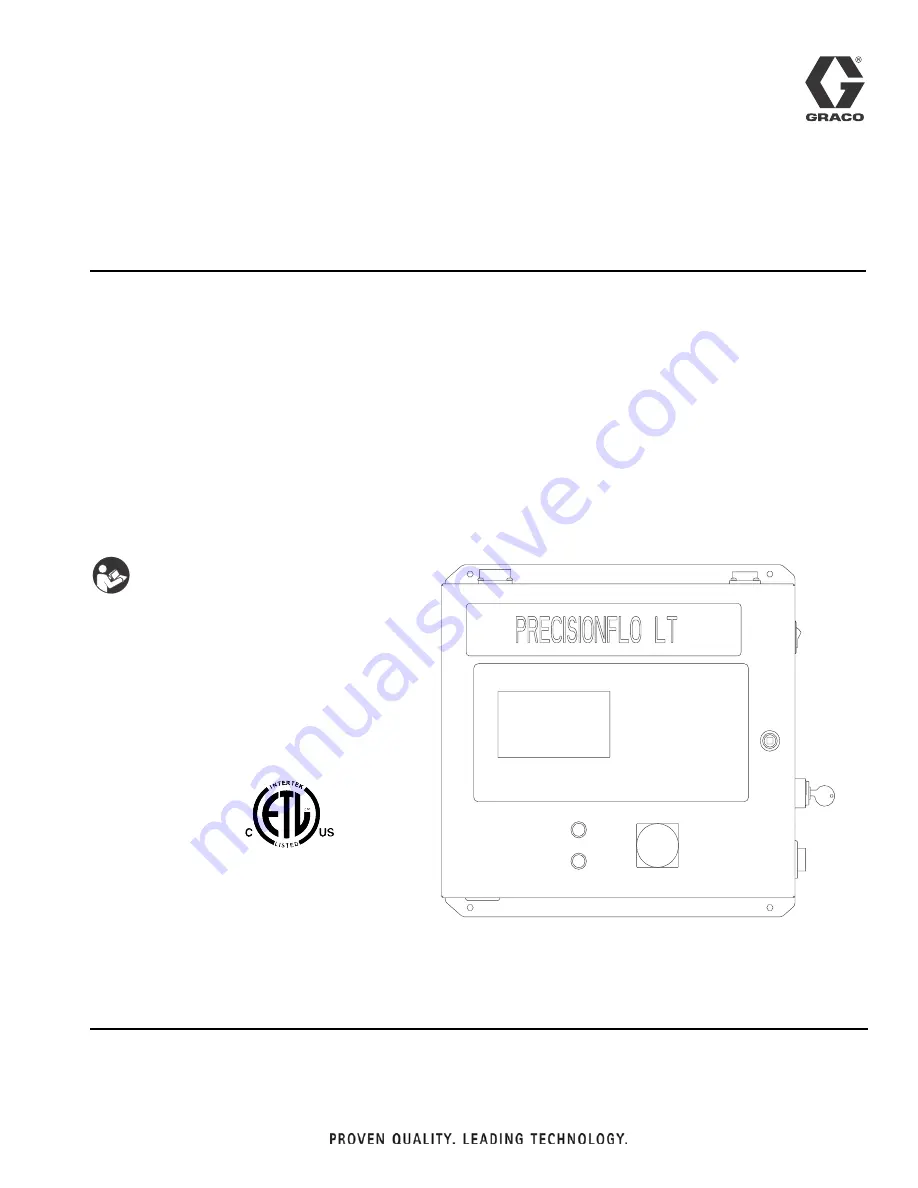
Instructions
PrecisionFlo LT
™
Standard, Series B
Electronically controlled fluid dispensing packages. For professional use
only.
• Pneumatically operated fluid regulators
• EasyKey keypad interface
Not for use in explosive atmospheres.
See page 2 for a list of models and maximum working pressures.
See page 4 for Table of Contents.
Important Safety Instructions
Read all warnings and instructions in this manual.
Save these instructions.
9902471
Certified to CAN/CSA C22.2 No. 1010
Conforms to
UL 3121-1
309738L
ENG