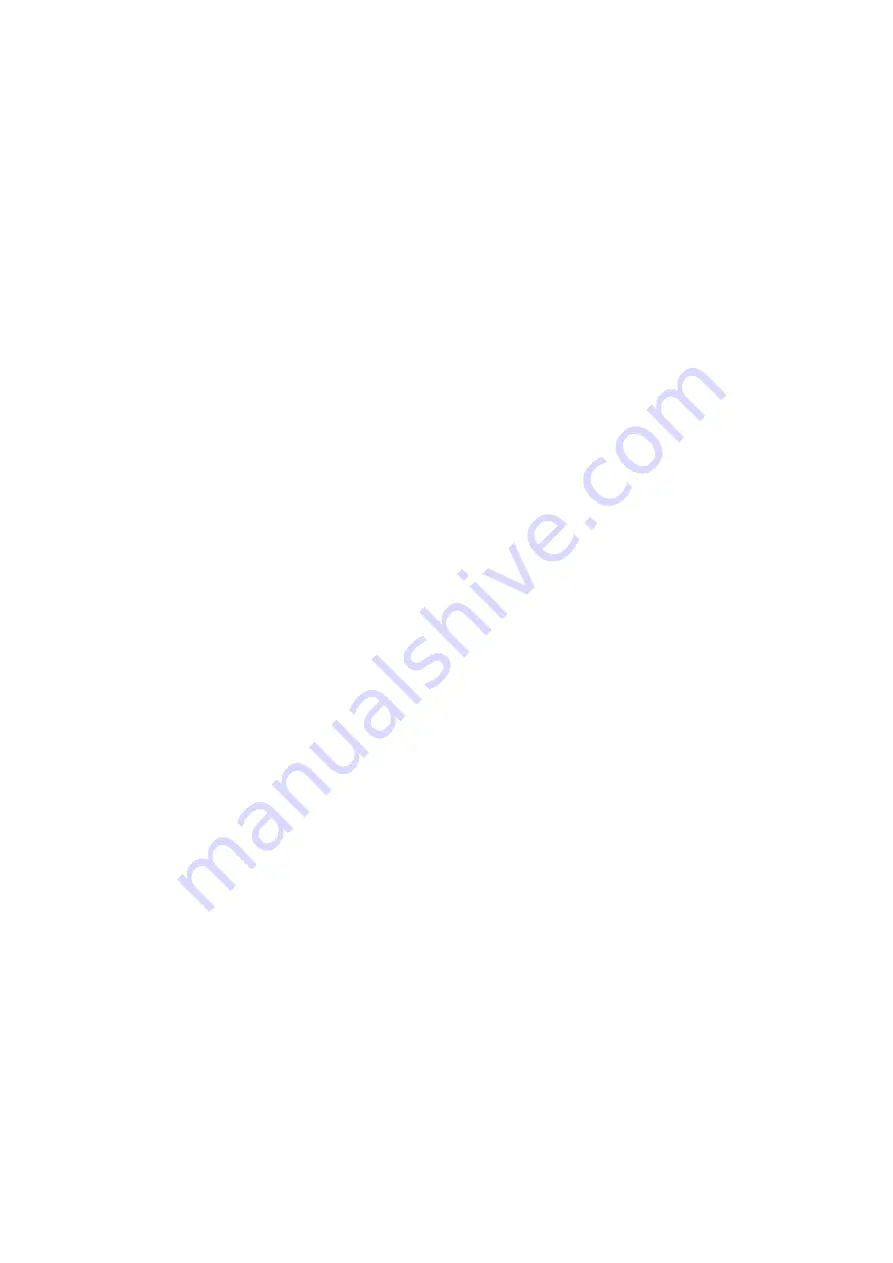
34
11.Leak detection methods.
The following leak detection methods are deemed acceptable for systems
containing flammable refrigerants. Electronic leak detectors shall be used to
detect flammable refrigerants, but the sensitivity may not be adequate, or may
need re-calibration. (Detection equipment shall be calibrated in a refrigerant-free
area.) Ensure that the detector is not a potential source of ignition and is suitable
for the refrigerant used. Leak detection equipment shall be set at a percentage
of the LFL of the refrigerant and shall be calibrated to the refrigerant employed
and the appropriate percentage of gas (25 % maximum) is confirmed. Leak
detection fluids are suitable for use with most refrigerants but the use of
detergents containing chlorine shall be avoided as the chlorine may react with
the refrigerant and corrode the copper pipe-work. If a leak is suspected, all
naked flames shall be removed/ extinguished. If a leakage of refrigerant is found
which requires brazing, all of the refrigerant shall be recovered from the system,
or isolated (by means of shut off valves) in a part of the system remote from the
leak. Oxygen free nitrogen (OFN) shall then be purged through the system both
before and during the brazing process.
12.Removal and evacuation.
When breaking into the refrigerant circuit to make repairs or for any other
purpose conventional procedures shall be used. However, it is important that
best practice is followed since flammability is a consideration. The following
procedure shall be adhered to:
Remove refrigerant;
Purge the circuit with inert gas;
Evacuate;
Purge again with inert gas;
Open the circuit by cutting or brazing.
The refrigerant charge shall be recovered into the correct recovery cylinders.
The system shall be flushed with OFN to render the unit safe. This process may
need to be repeated several times. Compressed air or oxygen shall not be used
for this task.
Flushing shall be achieved by breaking the vacuum in the system with OFN and
continuing to fill until the working pressure is achieved, then venting to
atmosphere, and finally pulling down to a vacuum. This process shall be
repeated until no refrigerant is within the system. When the final OFN charge is
used, the system shall be vented down to atmospheric pressure to enable work
to take place. This operation is absolutely vital if brazing operations on the pipe-
work are to take place.
Ensure that the outlet for the vacuum pump is not close to any ignition sources
and there is ventilation available.
13.Charging procedures.
In addition to conventional charging procedures, the following requirements
shall be followed. Ensure that contamination of different refrigerants does not
occur when using charging equipment. Hoses or lines shall be as short as
possible to minimise the amount of refrigerant contained in them.
Cylinders shall be kept upright.
Ensure that the refrigeration system is earthed prior to charging the system with
refrigerant. Label the system when charging is complete (if not already).
Extreme care shall be taken not to overfill the refrigeration system.
Prior to recharging the system it shall be pressure tested with OFN. The system
shall be leak tested on completion of charging but prior to commissioning. A
follow up leak test shall be carried out prior to leaving the site.
14.Decommissioning.
Before carrying out this procedure, it is essential that the technician is
completely familiar with the equipment and all its detail. It is recommended good
practice that all refrigerants are recovered safely. Prior to the task being carried
out, an oil and refrigerant sample shall be taken in case analysis is required prior
Summary of Contents for D 16M
Page 46: ...45 BG D 16 20 M...
Page 47: ...46 a b c d...
Page 48: ...47...
Page 49: ...48...
Page 50: ...49...
Page 51: ...50 8 1...
Page 52: ...51 PCB T 3 15A 250V 350V CO2 R290 R32 4 2...
Page 53: ...52 R32 R290 R32 R290...
Page 54: ...53 1 2 3 4 5 6 1 2 3 4 5 CO2 6...
Page 55: ...54 7 8 9 7 1 2...
Page 56: ...55 8 9 10 11 LFL 25 OFN 12...
Page 57: ...56 13 14...
Page 58: ...57 80 k 15 16...
Page 59: ...58 1 POWER 2 MODE 3 4 35 RH 85 RH 5...
Page 60: ...59 0 0 24 5 TURBO 6 TIMER 7 ION 8 35 85 0 24 5 30 RH 90 RH AS ES P1 P2 E3 EC EC Bucket Full...
Page 62: ...61 TIMER On TIMER Off 0 0 LED P2...
Page 63: ...62 Dryer 10 A 30 50...
Page 64: ...63 1 2 3 4 5 1 2 3 4 5 6 20 5 C 41 F 5 C 41 F 40 20 20 20 20...
Page 65: ...64 24 5 C 41 F 35 C 95 F 1 Full P2 30 Full P2 1 2 3...
Page 66: ...65 2 ID 13 5mm...
Page 67: ...66 1 2 3 4...
Page 68: ...67 5 C 41 F ES AS P1 P2...
Page 185: ...181 16 20...
Page 186: ...182 a...
Page 187: ...183...
Page 188: ...184...
Page 189: ...185...
Page 190: ...186 8 1...
Page 191: ...187 PCB T 3 15 250 350 CO2 R290 R32 4 2...
Page 192: ...188 R32 R290 R32 R290 1 2 3 4...
Page 193: ...189 5 6 1 2 3 4 5 6 7 8...
Page 194: ...190 9 7 1 2 8 9 10...
Page 195: ...191 11 25 12 13...
Page 196: ...192 14 a b c d e f g h 80 i j k 15 16...
Page 197: ...193...
Page 199: ...195 5 7 ION 8 35 85 0 24 5 30 90 RH...
Page 200: ...196 AS ES P1 P2 E3 EC EC 3 3 3 45 55...
Page 201: ...197 TIMER TIMER OFF TIME ON TIMER TIMER ON TIME OFF UP DOWN 30 10 1 24 5 TIMER ON OFF P2 10...
Page 202: ...198 1 2 3 4 5 1 2 3 4 5 6 20 5 C 5 C...
Page 203: ...199 24 5 35 C 1 8 P2 30 8 P2...
Page 204: ...200 2 ID 13 5...
Page 205: ...201 1 2 3 30 4...
Page 206: ...202 5 C ES AS P1 P2...
Page 260: ...256 D 16 20 M...
Page 261: ...257 e f g h...
Page 262: ...258...
Page 263: ...259...
Page 264: ...260...
Page 265: ...261 8 1...
Page 266: ...262 T 3 15A 250V 350V CO2 R290 R32...
Page 267: ...263 4 2 R32 R290 R32 R290...
Page 268: ...264 1 2 3 4 5 6 1 2 3 4 5 2 6...
Page 269: ...265 7 8 9 7 1 2...
Page 270: ...266 8 9 10 11 25 12...
Page 271: ...267 13 14 80...
Page 272: ...268 15 16...
Page 273: ...269 1 2 3 4 35 RH 85 RH 5...
Page 274: ...270 0 0 24h 5 6 7 e 8 35 85 0 24 5 30 RH 90 RH...
Page 275: ...271 AS ES P1 P2 E3 EC 3 3 3 45 55...
Page 276: ...272 10 1 24 5 0 0 2...
Page 277: ...273 10 30 50 30 50...
Page 278: ...274 11 12 13 14 15 13 14 15 16 17 18 40 20 20 20 20...
Page 279: ...275 20 5 C 41 F 5 C 41 F 4...
Page 280: ...276 24 5 C 41 F 35 C 95 F 3 5 8 P2 30 8 P2 1 2 3...
Page 281: ...277...
Page 282: ...278 6 ID 13 5mm...
Page 283: ...279 5 6 7 30...
Page 284: ...280 8...
Page 285: ...281 5 C 41 F ES AS P1 P2...
Page 286: ...282 RU D 16 20 M...
Page 287: ...283...
Page 288: ...284...
Page 289: ...285...
Page 290: ...286...
Page 291: ...287 8 1...
Page 292: ...288 T 3 15A 250 350 CO2 R290 R32 4 2...
Page 293: ...289 R32 R290 R32 R290...
Page 294: ...290 1 2 3 4 5 6 1 2 3 4 5 CO2 6...
Page 295: ...291 7 8 9 7 1 2...
Page 296: ...292 8 9 10 11 25...
Page 297: ...293 12 13 14...
Page 298: ...294 80 15 16...
Page 299: ...295...
Page 300: ...296 1 2 3 4 35 85 5 0 24 On Off...
Page 301: ...297 5 6 7 8 35 85 0 24 5 30 90...
Page 302: ...298 AS ES P1 P2 E3 EC 3 3 3 45 55...
Page 303: ...299 Off On On Off 0 5 10 1 24 5 On Off 0 0 P2 10 30 50 30 50 30 50...
Page 304: ...300 1 2 3 4 5 1 2 3 4 5 6 20 5 C 41 F 5 40 20 20 20 20...
Page 305: ...301 24 5 C 41 F 35 C 95 F 1 8 P2 30 8 P2 1 2 3 5 6...
Page 306: ...302 2 13 5...
Page 307: ...303 1 2 3 30 4...