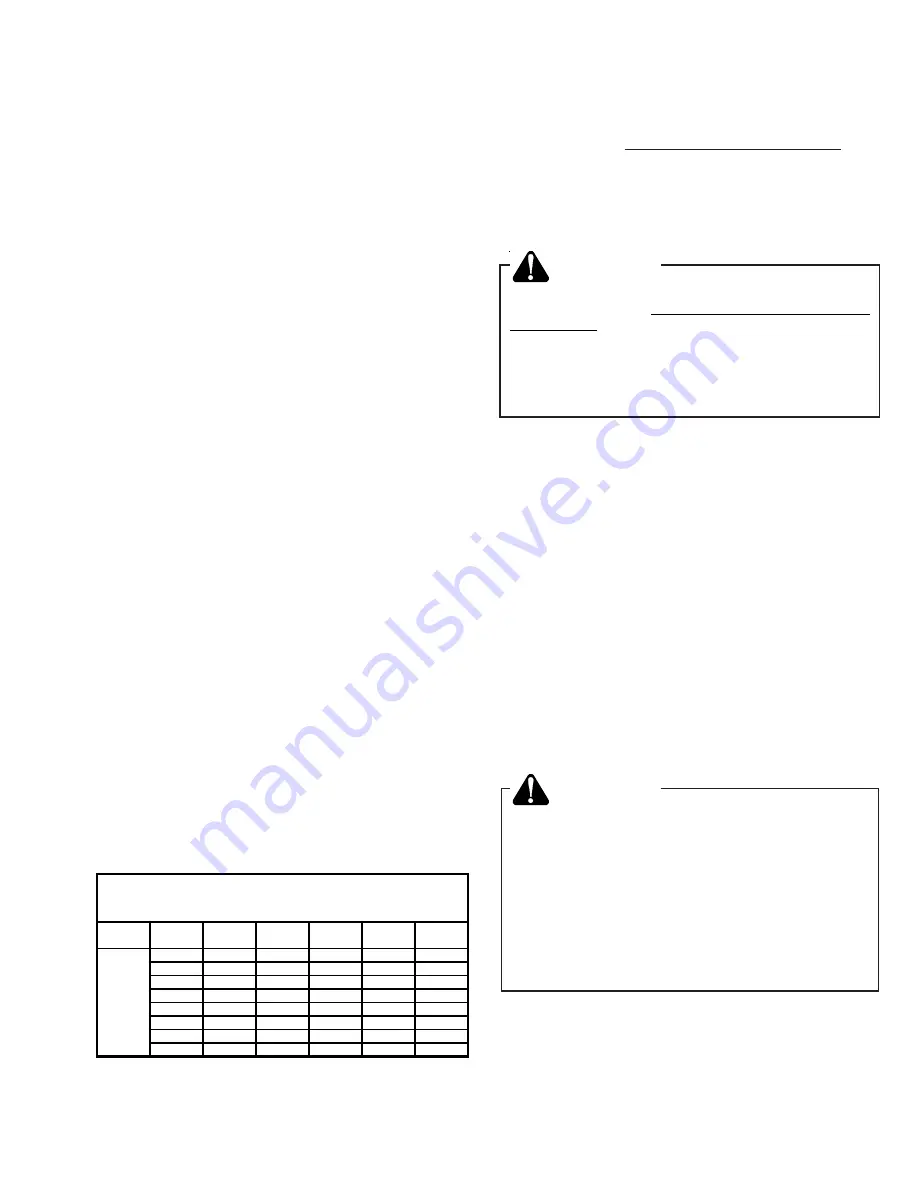
IO-213D
2/04
11
GAS PIPING & GAS PIPE CAPACITY TABLE
Check the rating plate to make certain that the gas supplied
is compatible with the unit requirements. Care should be
taken after the installation of this appliance that the gas
control valve is not subjected to high gas supply line
pressure. In making connections, avoid strains as they may
cause noise and damage the controls. Always use a back-
up wrench when tightening the gas supply pipe to the gas
control valve. Check for leaks in the gas supply using soap
bubbles or other approved methods.
NEVER USE AN OPEN FLAME TO CHECK FOR GAS
LEAKS. THIS PRACTICE MAY CAUSE A FIRE,
EXPLOSION, BODILY HARM OR PROPERTY DAMAGE.
Pipe joint compound must be resistant to the action of L.P.
gas. When connecting the gas service to the furnace, a
ground joint union and manual shutoff must be installed
exterior to the furnace cabinet and located in the same room
so the control assembly may be easily removed.
A 1/8" NPT plug on the supply pipe near the manual valve
for the purpose of making pressure measurement should
also be installed. The valve should be readily accessible for
turning on or off. A capped sediment trap, sometimes called
a drip leg, must be installed in the gas supply pipe as close
to the furnace as possible. The sediment trap must
incorporate a change of gas flow direction.
Refer to local codes or the previously mentioned publications
for proper location and size of the manual shutoff and
sediment trap lengths.
The gas pipe must be sized to eliminate undue pressure
drop. See pipe capacity table or consult your local utility.
Both the supply and manifold pressure must be measured
with the furnace running using the field supplied pressure
tap near the manual shut-off valve and the pressure adjusted
if necessary.
All gas piping must conform to local codes, or in the absence
of local codes, to the National Fuel Gas Code ANSI Z223.1
and / or CAN/CGA B149 Installation Codes.
Note:
Copper tubing must not be used for natural gas
installations where more than .3 grains of hydrogen sulfide
per 100 standard cubic feet of gas is present. (If the
quantities of hydrogen sulfide cannot be verified, do not use
copper).
FOR INSTALLATIONS IN THE COMMONWEALTH OF
MASSACHUSETTS SEE FUEL GAS AND PLUMBING
CODE 248 CMR: APPENDIX C.
P ip e
S iz e *
½
¾
1
1 ¼
1 ½
1 0
1 3 2
2 7 8
5 2 0
1 0 5 0
1 6 0 0
2 0
9 2
1 9 0
3 5 0
7 3 0
1 1 0 0
L e n g th
3 0
7 3
1 5 2
2 8 5
5 9 0
8 9 0
o f
4 0
6 3
1 3 0
2 4 5
5 0 0
7 6 0
P ip e
5 0
5 6
1 1 5
2 1 5
4 4 0
6 7 0
in F e e t
6 0
5 0
1 0 5
1 9 5
4 0 0
6 1 0
7 0
4 6
9 6
1 8 0
3 7 0
5 6 0
8 0
4 3
9 0
1 7 0
3 5 0
5 3 0
* N o m in a l s iz e o f iro n p ip e in in c h e s .
C a p a c ity o f g a s p ip e o f d iffe re n t d ia m e te rs a n d le n g th in
ft
3
/ h r. w ith a p re s s u re d ro p o f 0 . 3 " W .C . a n d a s p e c ific
g ra v it y o f 0 . 6 0 (n a t u ra l g a s ).
After the length of pipe has been determined, select the
pipe size, which will provide the minimum cubic feet per
hour of gas flow for the required input of the appliance. In
the case where more than one appliance utilizes the same
supply pipe be sure to consider the sum of all appliances.
The cubic feet of gas required for the appliances should be
determined using the following formula;
Cubic feet of Gas input of appliance (BTU/hr.)
gas required Heating value of gas (BTU/hr.)
The gas input of the appliance is marked on the specification
plate. The heating value of the gas may be determined by
contacting the gas utility or gas supplier.
CAUTION
IF THE LOCAL UTILITY PERMITS THE USE OF A FLEXIBLE
GAS CONNECTOR -
ALWAYS USE A NEW FLEXIBLE
CONNECTOR
.
DO NOT
USE FLEXIBLE GAS LINES THAT
HAVE SERVICED ANOTHER APPLIANCE. AFTER A PERIOD
OF TIME THESE LINES MAY BECOME BRITTLE AND CAN
DEVELOP LEAKS. THE CONNECTIONS TO A FLEXIBLE
GAS LINE MUST BE MADE OUTSIDE OF THE FURNACE
CABINET.
CIRCULATING AIR SUPPLY AND RETURN AIR
The circulating air supply may be taken from; 1) Outside
the building, 2) return ducts from several rooms, 3) central
return, 4) any combination of the above.
When a cooling coil is not installed it is recommended that
the supply duct have an access panel so the heat exchanger
can be viewed. This panel shall be of sufficient size to permit
the entrance of a light or probe to assist in the observation
of the heat exchanger integrity or sampling the air stream.
It should be sealed to prevent air leakage during normal
operation.
Return air from one dwelling shall not be discharged into
another dwelling through the heating system.
There shall be a positive separation between combustion
air and return air.
Do not obtain return air from a hazardous or insanitary
location or a refrigeration machinery room or any room or
space having any fuel-burning appliances therein.
CAUTION
DO NOT TAKE RETURN AIR FROM BATHROOMS,
KITCHENS, FURNACE ROOMS, GARAGES, UTILITY/
LAUNDRY ROOMS OR COLD AREAS. IF OUTSIDE AIR IS
UTILIZED, IT SHOULD NOT BE TAKEN FROM WITHIN 10
FEET OF AN APPLIANCE VENT OUTLET, A VENT OPENING
OR A PLUMBING DRAINAGE SYSTEM, OR THE DISCHARGE
FROM AN EXHAUST SYSTEM UNLESS THE OUTLET IS
THREE (3) FEET ABOVE THE OUTSIDE AIR INLET. DO
NOT TAKE RETURN AIR FROM AN AREA WHERE IT CAN
PICK-UP OBJECTIONABLE ODORS, FUMES, OR
FLAMMABLE VAPORS.
Note:
When a combination of outdoor and indoor air is
utilized the system should be designed and adjusted such
that the temperature reaching the appliance will not drop
below 50
o
F during heating operation. This will minimize the
possibility of condensate forming inside the heat exchanger.
When this type of system is utilized the volume of air must
not be reduced.
=