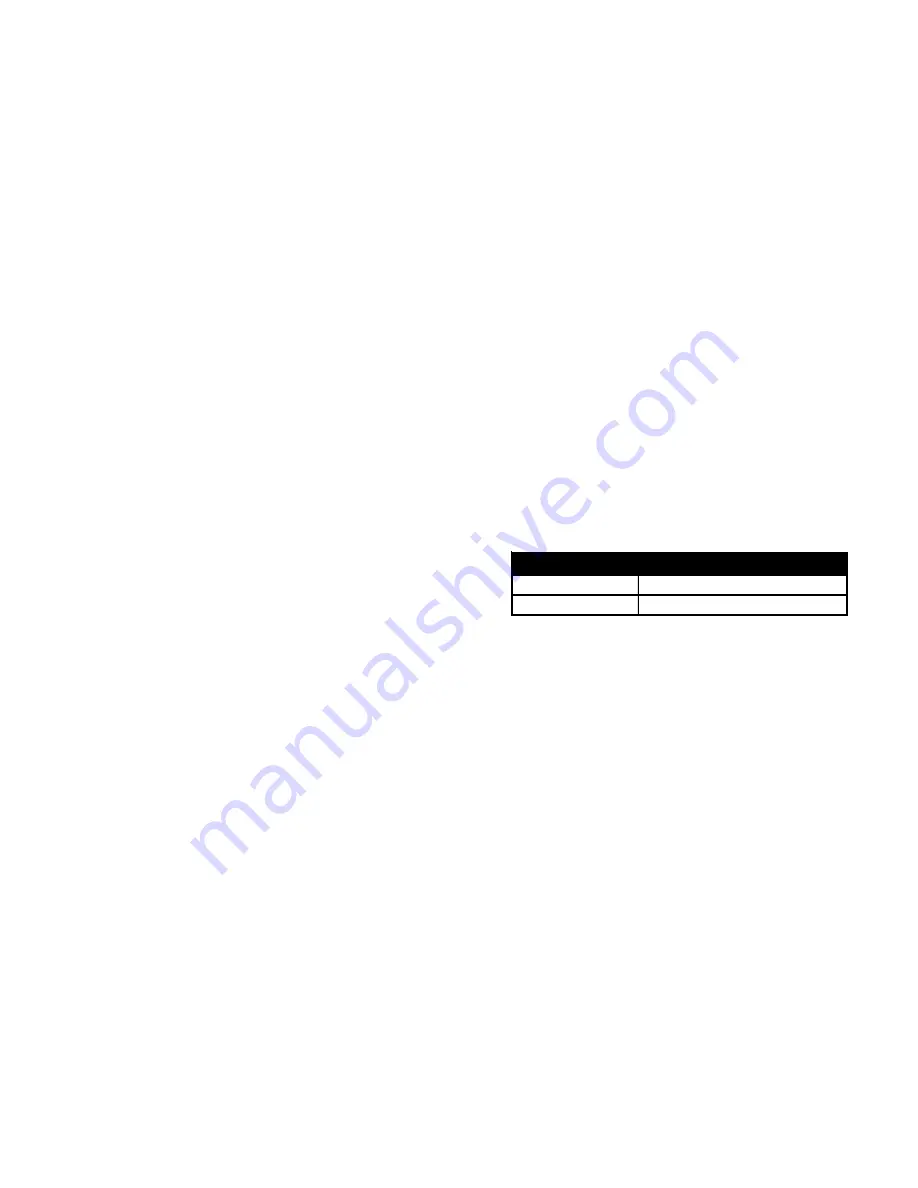
9
For installation greater than 25’ of line set, indoor unit airflow,
condensing unit location and number of tubing fittings will have
an impact on final unit charge amount. Start with half of the 25’
line set charge and proceed.
Turn the electrical power on, and let the system run. Wait for the
refrigerant pressures to stabilize.
EXPANSION VALVE INDOOR COILS:
NOTE:
EXPANSION VALVE BULB, MUST BE IN PLACE ON
SUCTION LINE & INSULATED.
Outdoor Temperature Over 60
o
F.
When the outdoor temperature
is above 60
°
F, the system is to be charged with the room thermostat
set in the “Cooling” mode and the fan operating in the “Auto”
position.
Outdoor Temperature Less Than 60
°
F.
If the outdoor
temperature is less than 60
°
F, the unit is to be charged with the
room thermostat set in the “Heat” mode and the fan set in the
“Auto” position.
System Charging – Cooling Mode
The following describes adjusting the refrigerant charge with the
ambient temperature in excess of 60
°
F and the room thermostat
adjusted as indicated above.
At stabilized cooling conditions and with an outdoor temperature
of
60
°
F
or higher, the system should have from 9
°
F
to 13
°
F
subcooling. For a proper subcooling reading, measure the
refrigerant pressure and temperature at the outdoor unit’s liquid
line service valve. If you have less than 9
°
F
subcooling, add
charge.
If you have more than
13
°
F subcooling, remove charge.
While reaching the proper subcooling level, it is important to know
the discharge line temperature. This temperature should be at
least 80
°
F over ambient or unit is flooding back to compressor. If
flooding (i.e. low discharge line temperature) occurs, adjust valve
stem on expansion valve inward (clockwise viewing end of
expansion valve). This will increase the super heat.
After achieving the proper subcooling and a sufficient discharge
temperature, make small adjustment to expansion valve stem to
reach 8
°
F to 10
°
F of super heat. Adjusting the valve stem in
(clockwise), increases super heat. Adjusting the valve stem out
(counter clockwise), decreases superheat . If the system is
performing properly, reinstall the service port caps and the valve
bonnets. With the valve opened, the valve bonnet is the primary
seal against refrigerant leaks. Apply two drops of clean oil to the
cap threads, allowing the oil to run down to the inner cap seal
surface. Close caps finger-tight. Then tighten cap additional two
to three hex flats.
System Charging – Heating Mode
The following method can be employed as a method to check the
system charge in the heating mode by measuring the hot gas
discharge at the compressor.
1.
Allow the system to operate for at least 20 minutes.
2.
Attach and insulate an electronic thermometer to the hot gas
discharge line mid way between the compressor and the re-
versing valve.
Note:
The thermometer is to be well insulated
to prevent ambient influences.
3.
Adjust the charge to maintain a clear sight glass.
4.
Allow the compressor to operate for about 10 additional min-
utes and measure the hot gas discharge temperature.
5.
Using an additional electronic thermometer, measure the
ambient.
6.
Adjust the charge until the hot gas temperature equals 105
°
F + ambient (+ or – 5
°
F). Remove charge to increase the
temperature.
Note:
When adjusting the charge, allow the compressor to
operate for about 10 minutes before taking readings.
Note:
Subsequent opening and replacement of the cap will
require only 1/2 to 1 hex flat. See the table below for the
torque required for an effective seal on the valve bonnet (1/6
turn past finger tight.
After closing the valve bonnet, perform a final refrigerant leak test
on the valves and sweat connections. Return the room thermo-
stat to the desired settings.
XIV
DEFROST CONTROL (DC)
The CPLE uses a Time/Temperature method for defrost. A thermal
sensor is attached to the condenser coil to determine the outdoor
coil temperature. The coil temperature sensor is electrically
“Normally Open” and is wired to the electronic defrost control that
is located in the control box.
Both coil temperature and compressor run time determine de-
frosting of the outdoor coil. Adjustments to the defrost timing se-
lection can be changed from the 60 minute factory setting to ei-
ther 30 or 90 minutes by moving the jumper on the defrost con-
trol. To initiate a defrost, the following statements must be true:
¾
The defrost sensor must be closed, and
¾
The compressor run time must equal the timing selection on
the defrost board.
Note:
The compressor run time is accumulative during multiple
“heating” cycles. The timer will reset to zero only when the de-
frost sensor returns to an open condition. If the room thermostat
is operating in the “EM HT” mode, no accumulation of compres-
sor time is recorded.
Tubing Size
Torque (Foot-Pounds)
5/8
14
1-3/8
16
Table 8.