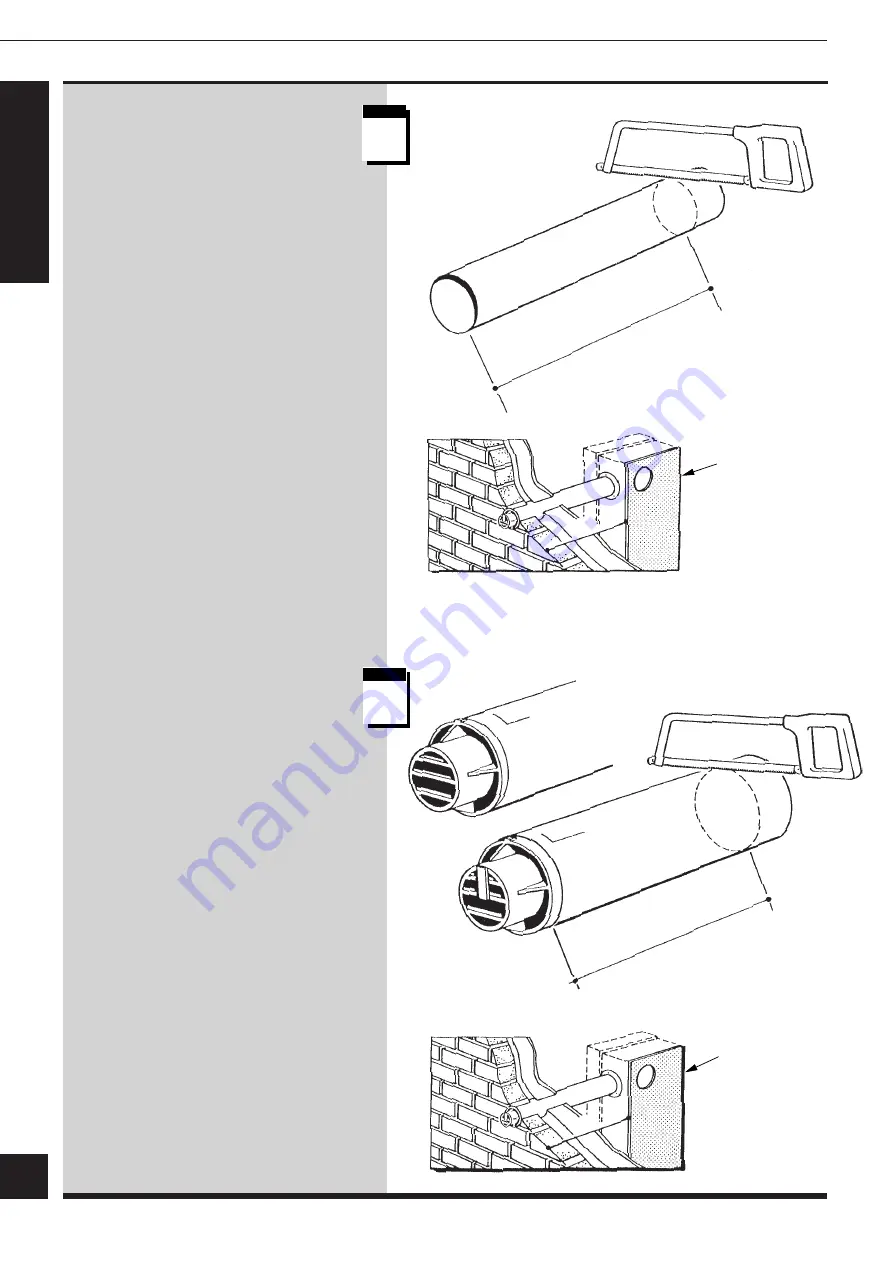
18
221051B
18
SECTION
Flue Duct (Standard or
Long)
Mark the duct to length “S”+11mm then
cut square and remove any burrs.
Flue Installation
5
s t e p
9
2895
s t e p
10
Terminal/Air Duct
(Standard or Long)
Mark the duct to the length “S”+13mm
then cut square and remove any burrs.
S+11mm
S
S+13mm
WALLPLATE
/TEMPLATE
WALLPLATE
/TEMPLATE
S
1M AND 2M FLUE
TERMINAL
STANDARD
FLUE TERMINAL