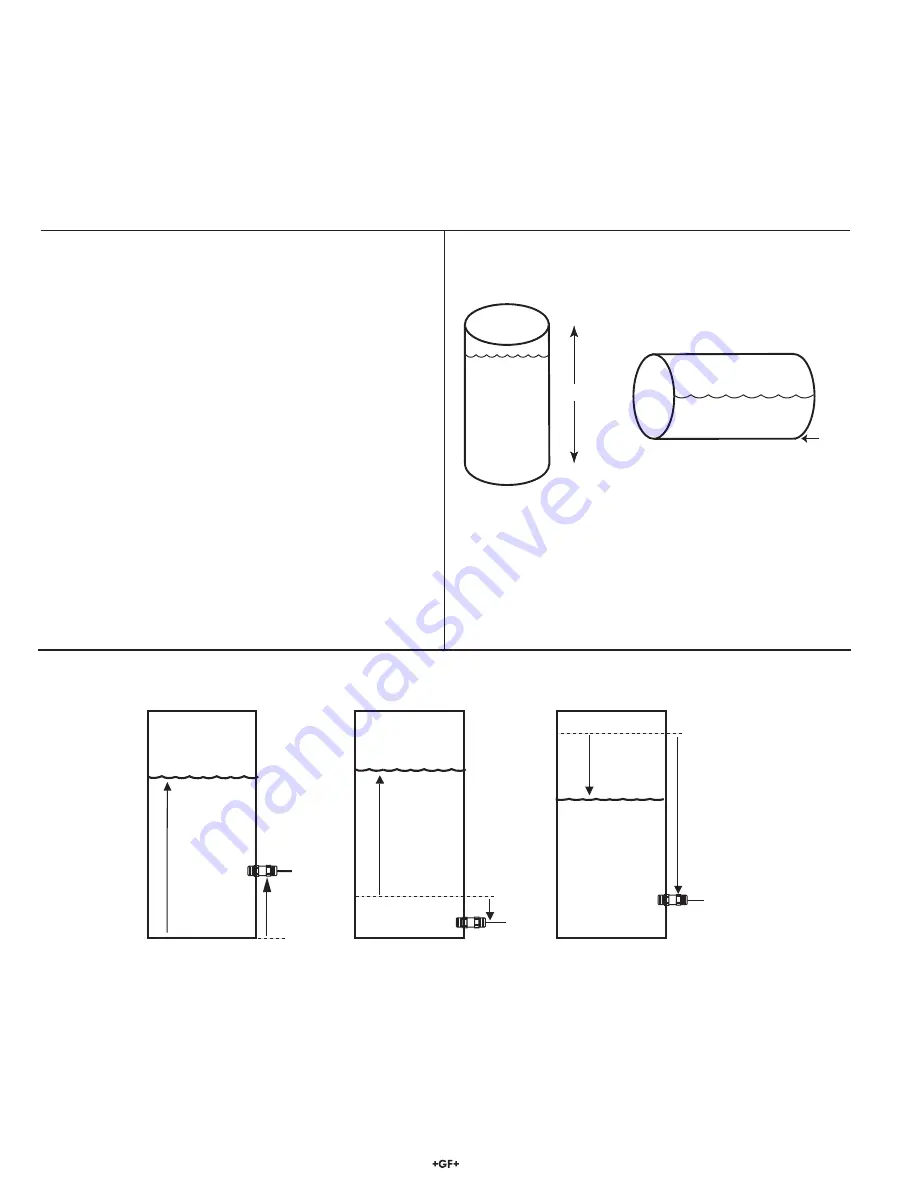
4
Signet 8250-2 Level Transmitter
Zero reference point (Z):
The point in the vessel where you want the 8250 to display zero
(0 ft., 0 gal. etc).
• If Z is located below the
fl
uid surface, the 8250 will display
a positive level measurement.
• If Z is located above the
fl
uid surface, the 8250 will display
a negative level measurement.
Sensor Location point (S
Loc
):
The point on the level sensor where the measurement is taken.
• The 2450 Pressure sensor measures from the centerline of
the diaphragm.
Offset (O):
The distance from Z to S
Loc
.
• Enter a positive value in the Calibrate menu if the sensor is
located above Z.
• Enter a negative value in the Calibrate menu if the sensor
is located below Z.
• Enter 0 in the Calibrate menu if the sensor is located at Z.
Level (L):
The distance from Z to surface of
fl
uid (displayed as "Level"
by transmitter).
L
> 0
O
> 0
Z
S
LOC
L
> 0
O
< 0
Z
S
LOC
L
< 0
S
LOC
O
< 0
Z
2450 Pressure Sensor Location and Offset
Z
Z
For horizontal cylinders only, the
zero reference point MUST be
the lowest point in the vessel.
For most vessels, the zero
reference point may be
designated as any height
in the vessel.
5. System
Confi guration
The 8250 Level Transmitter must be programmed using the following system con
fi
guration procedure.
1. Determine where you want the level measurement to start. This is the Zero reference point (
Z
).
Review the diagram to help select the best option.
2. Determine where you will mount the sensor. This is
S
Loc
.
Consult the Sensor manual for information regarding the best location for the sensor.
3. Measure the distance between Z and S
Loc
. This is
O(ffset).
4. Enter the Offset into the Calibrate menu.