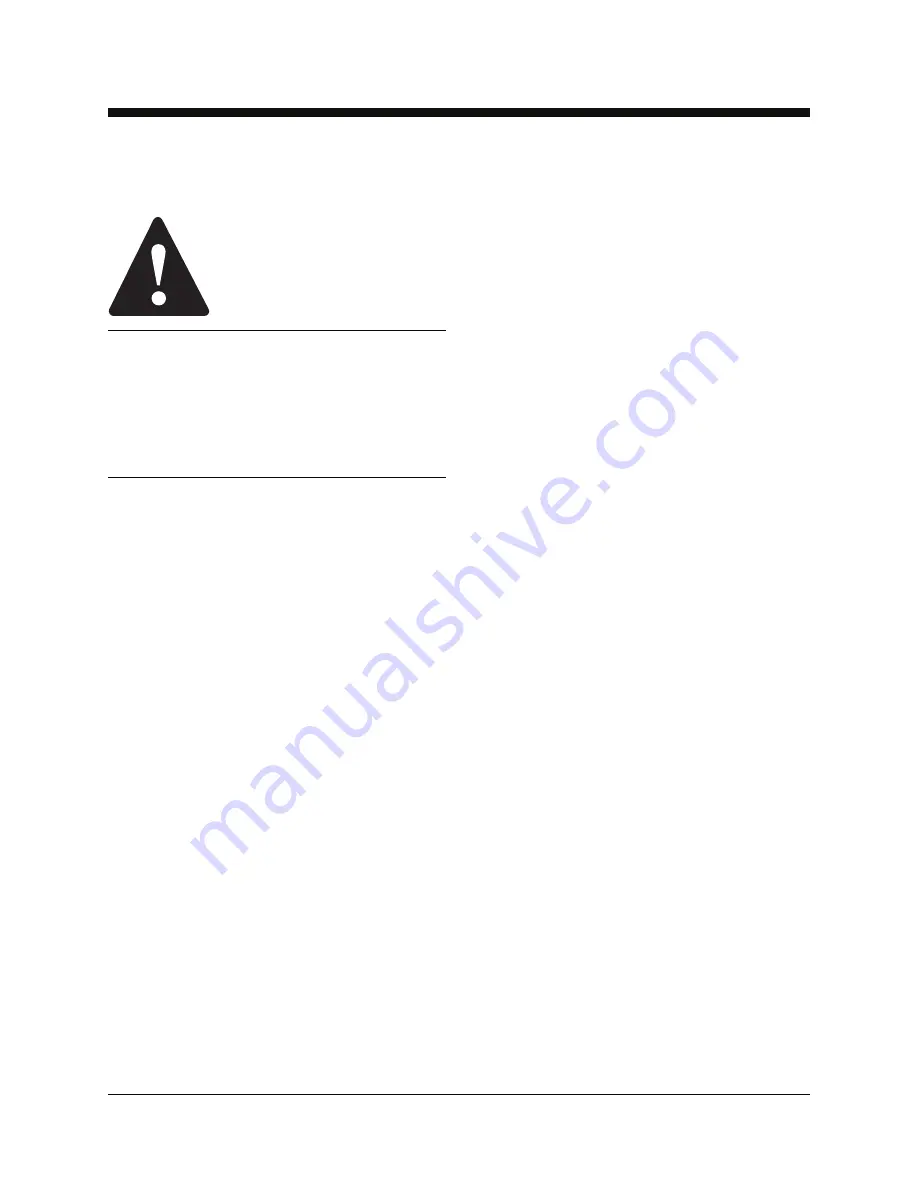
Part No. 114047
Self-Propelled Servicing Platform
1
Operator's Manual
Second Edition • Fifth Printing
Operating the Machine in
Hazardous Locations
Read, understand and obey the following
instructions before entering a Class 1, Division 2,
Group D hazardous location:
1 If the engine is running, turn off the engine.
2 Allow the engine to cool down until the
thermometer reads below 348°F.
3 Locate the engine and charger switches.
4 Move the switches to the off position and lock.
5 Lock all 3 AC plug covers.
6 Be sure the lanyards on the battery disconnect
plugs are in place and secured.
7 Be sure the engine side chassis cover is latched
and locked.
8 Be sure the plate in the back of the battery box
is in place to prevent battery movement.
Safe Operation in Hazardous Locations
Danger
Failure to obey the instructions and
safety rules in this manual will result
in death or serious injury.
This machine may be operated
in a Class 1, Division 2, Group D
hazardous location only if the
following safety rules and
requirements are strictly
followed.
Detailed definitions of a Class 1, Division 2
Hazardous Environment can be found in NFPA 505,
and NFPA 70.
Definitions for Hanger and Aircraft Class 1, Division
2 Hazardous Environments can be found in NFPA
70 Section 513.3 and are as follows:
Areas Not Cut Off or Ventilated. The entire area of
the hangar, including any adjacent and
communicating areas not suitably cut off from the
hangar, shall be classified as a Class I, Division 2
or Zone 2 location up to a level 450 mm (18 in)
above the floor.
Vicinity of Aircraft. The area within 1.5 m (5 ft)
horizontally from aircraft power plants or aircraft
fuel tanks shall be classified as a Class I, Division
2 or Zone 2 location that shall extend upward from
the floor to a level 1.5 m (5 ft) above the upper
surface of wings and of engine enclosures.
Only trained and authorized personnel shall be
permitted to operate this machine in hazardous
locations.
Do not enter hazardous locations unless the engine
and charger switches are off.
Do not enter hazardous locations unless the
thermometer reads below 348°F.
Do not operate the engine while the machine is in
hazardous locations.
Do not charge the batteries in hazardous locations.
Do not remove the red AC plug covers in hazardous
locations.
Do not disconnect the battery pack plugs in
hazardous locations.
Do not open the covers in hazardous locations.
Do not perform maintenance or repairs on this
machine in hazardous locations.
Summary of Contents for Z45/25J
Page 1: ......