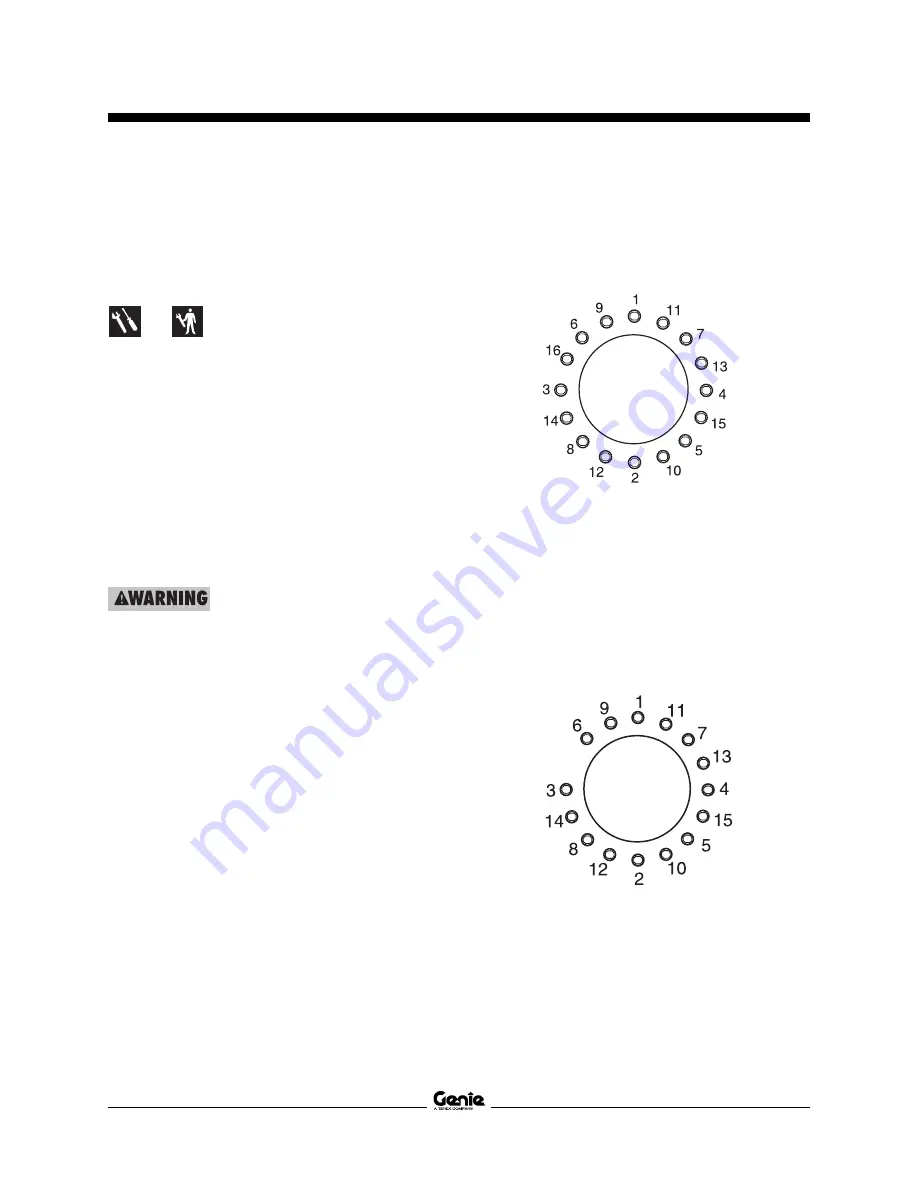
3 - 42
Z-34/22 IC
Part No. 128267
July 2007
Section 3 • Scheduled Maintenance Procedures
REV A
D-5
Check the Turntable Rotation
Bearing Bolts
Note: Genie requires that this procedure be
performed every 1000 hours or annually,
whichever comes first.
Maintaining proper torque on the turntable bearing
bolts is essential to safe machine operation.
Improper bolt torque could result in an unsafe
operating condition and component damage.
1 Raise the secondary boom and place a safety
chock on the secondary boom lift cylinder.
Carefully lower the boom onto the lift cylinder
safety chock. Turn the machine off.
Crushing hazard. Keep hands
away from the cylinder and all
moving parts when lowering the
secondary boom.
Note: The lift cylinder safety chock is available
through Genie Service Parts (Genie part number
36555).
2 Check to ensure that each turntable bearing
bolt is torqued in specified order to
180 ft-lbs / 244 Nm.
Bolt torque sequence
3 Remove the safety chock. Lower the boom to
the stowed position.
4 Access the turntable bearing bolts through the
access hole on the side of the chassis.
5 Check to ensure that each bearing mounting
bolt under the drive chassis is torqued in
specified order to 180 ft-lbs / 244 Nm.
Bolt torque sequence
CHECKLIST
D
PROCEDURES
Summary of Contents for Z-34/22IC
Page 4: ...Z 34 22 IC Part No 128267 July 2007 This page intentionally left blank iv...
Page 14: ...Z 34 22 IC Part No 128267 July 2007 This page intentionally left blank xvi...
Page 132: ...5 4 Z 34 22IC PartNo 128267 June 2007 Section 5 Schematics...
Page 133: ......
Page 137: ......
Page 141: ......
Page 145: ......
Page 169: ...Generator Option Wiring Diagram from serial number 3242 to 4081 Section 5 Schematics July 2007...
Page 172: ...Section 5 Schematics July 2007 Generator Option Wiring Diagram from serial number 4082 to 4799...
Page 176: ...Section 5 Schematics July 2007 Manifold and Limit Switch Wiring...
Page 177: ......
Page 180: ...Section 5 Schematics July 2007 Hydraulic Schematic 2WD Models...
Page 181: ......
Page 184: ...Section 5 Schematics July 2007 Hydraulic Schematic 4WD Models...