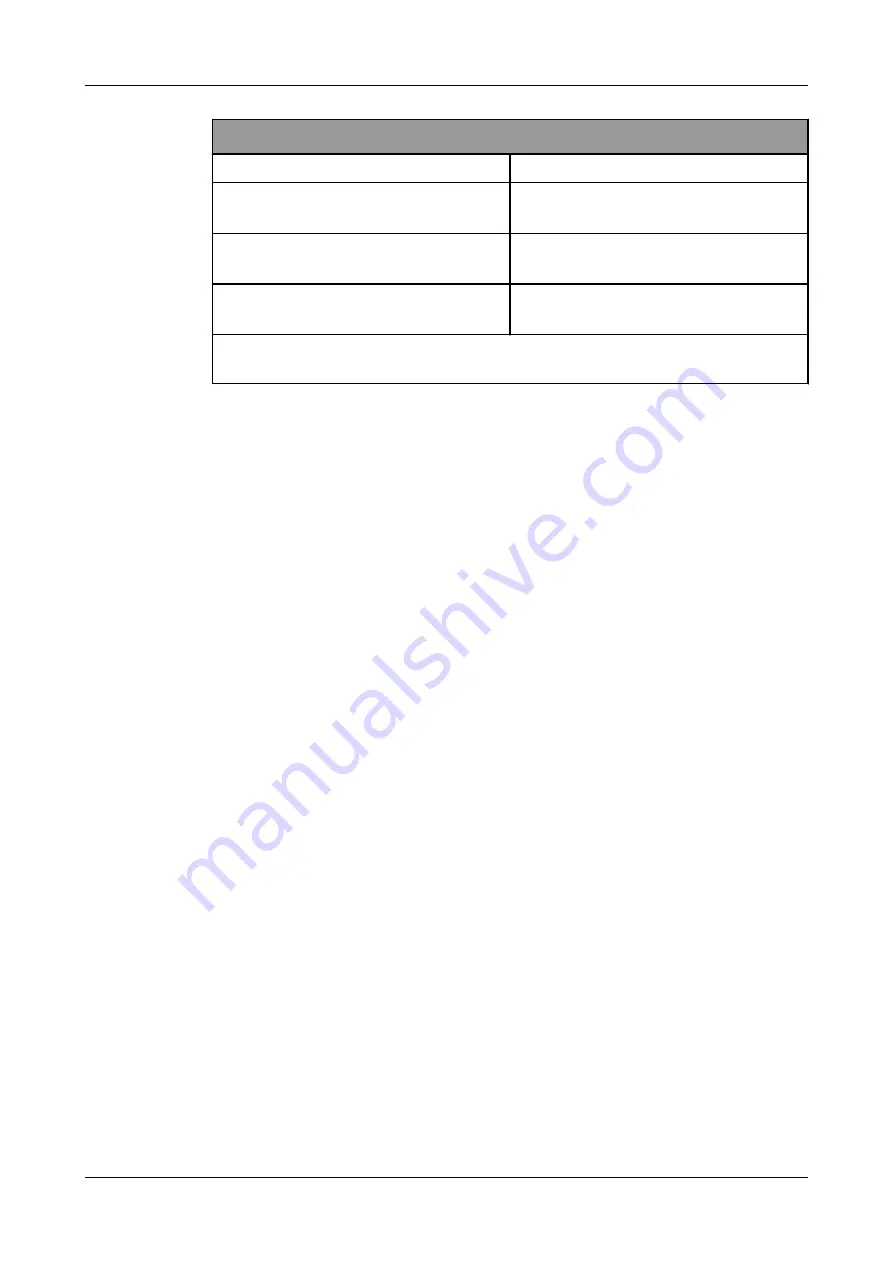
Table sealing materials - temperature resistance
Sealing materials
General temperature resistance*
EPDM
-40...+135 °C
(-40...275 °F)
FKM
-10...+200 °C
(+14...+392 °F)
HNBR
-25...+140 °C
(-13...+284 °F)
* The general resistance of the material does not correspond to the maximum
operating temperature.
Technical data
Resistance and permitted operating temperature of the sealing materials
430BAL008430EN_4
08.03.2022
25
Summary of Contents for VARIVENT X
Page 87: ...Appendix 430BAL008430EN_4 08 03 2022 87 ...
Page 88: ......