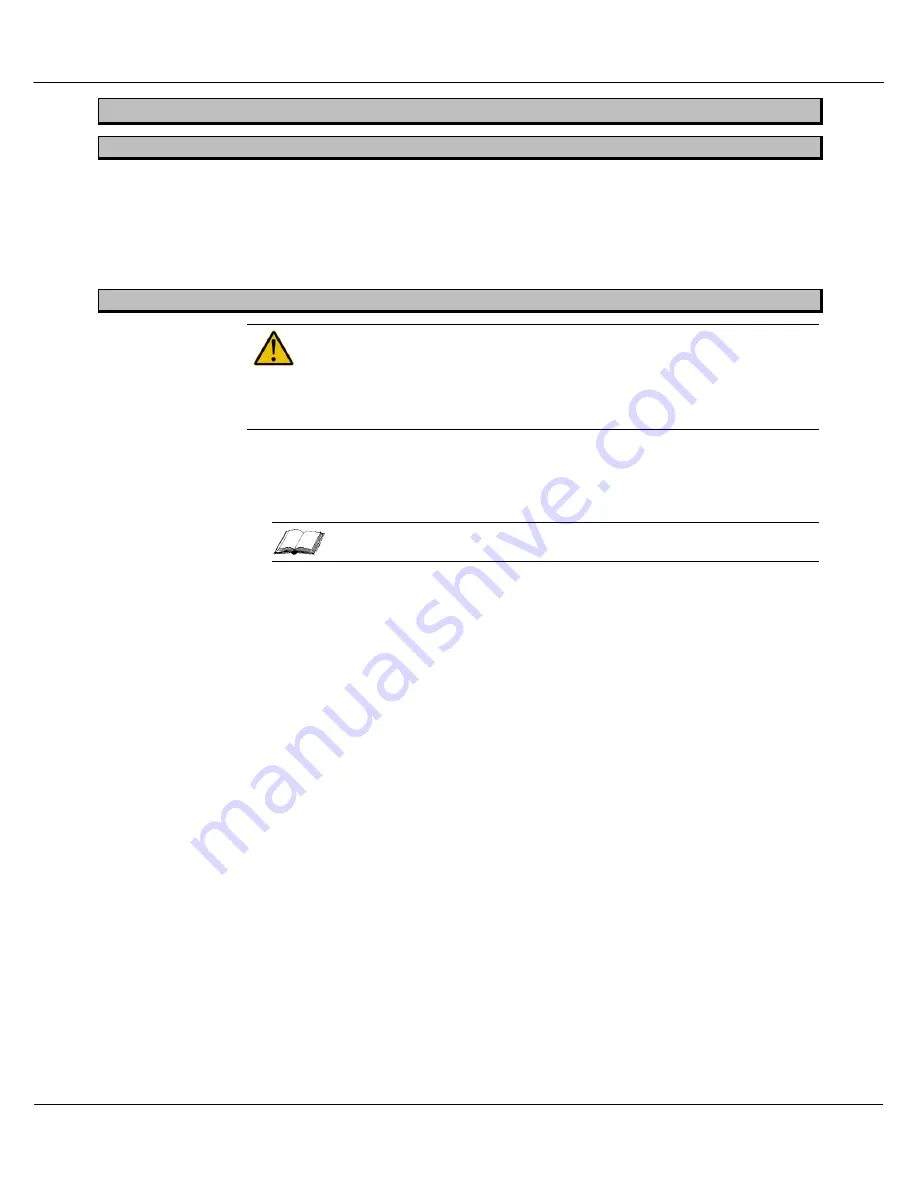
Operation
Safety instructions for operation
2007-9015-001
03-2014
7
Operation
7.1
Special personnel qualification required for operation
Operation may only be performed by specially qualified personnel in
accordance with the safety instructions.
The operator may only carry out work on the equipment if trained, instructed and
authorized to do so by the owner.
7.2
Safety instructions for operation
Caution!
Always open 2 ball valves under the hydraulic power unit before
operating the equipment. Operating the hydraulic power unit with
closed ball valves will result in failure and/or injuries due to excess of
pressure in the oil filter.
To prevent damage to property and/or life-threatening injury to personnel
always follow these instructions:
● Only fit or use the product for its intended purpose.
Also read the chapter on ”Safety”.
Special dangers involved in operation:
● Incorrect use may lead to serious damage to property and/or life-threatening
injury to people.
● Operating the hydraulic power unit with closed ball valves could result in
serious damage and/or injury.
● The careless use of personal protection equipment could result in serious
physical injury.
● Leaking lubricants, solvents,... could cause injury if they come into direct
contact with the skin and could make the floor surface slippery which could
result in dangerous fall.
● Insufficient ventilation inside buildings surrounding the manure pit could
lead to intoxication.
Before operating, make sure you are familiar with the following:
● the operating and control elements
● the equipment
● the method of operation
● the immediate environment
● the safety devices