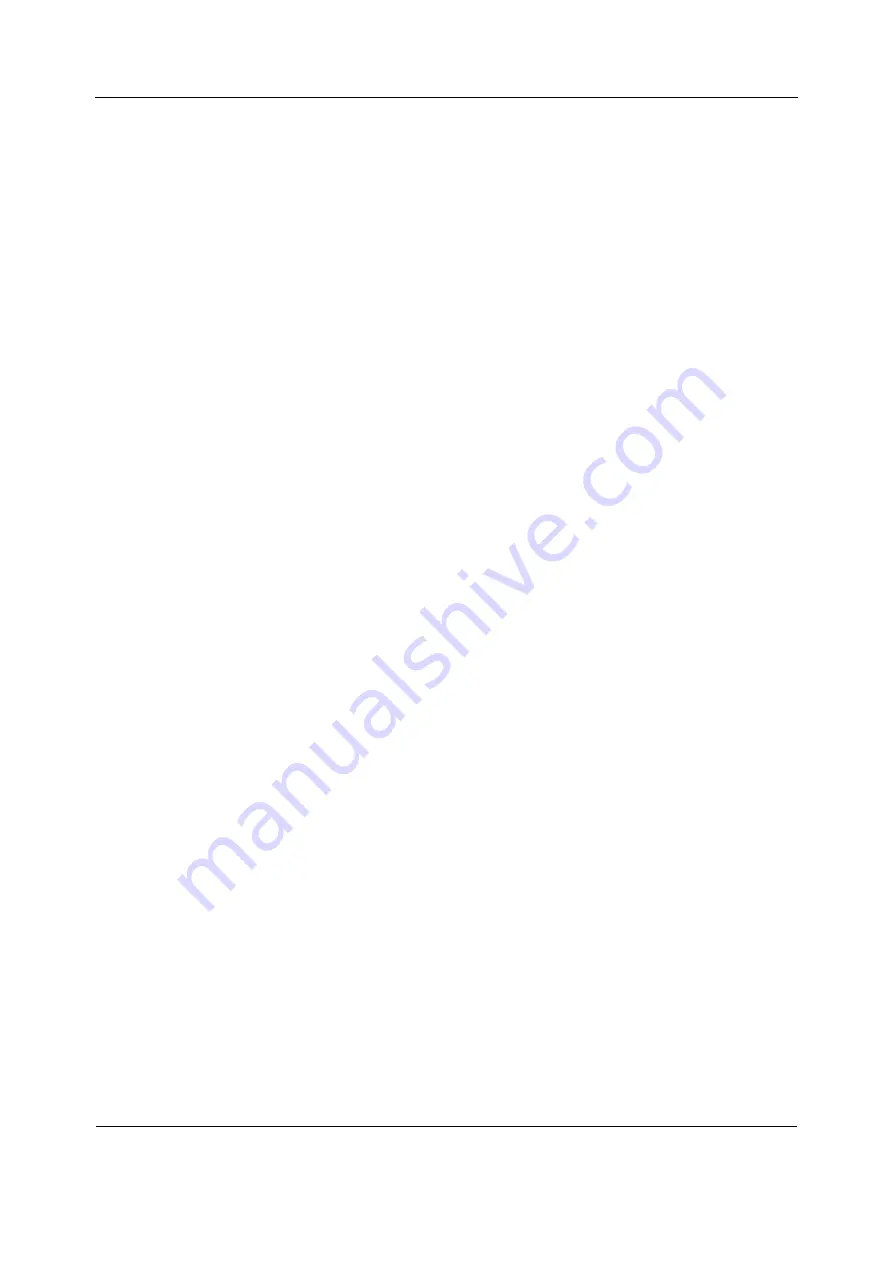
Table of contents
15 - i
2062973-004
Main components. . . . . . . . . . . . . . . . . . . . . . . . . . . . . . . . . . . . . . . . . . . . . . . . . . . . . . . . . . . . . . . . . . 15-3
1.3.1 Connectors and signals. . . . . . . . . . . . . . . . . . . . . . . . . . . . . . . . . . . . . . . . . . . . . . . . . . . . . . 15-3
1.3.2 EMBC Board. . . . . . . . . . . . . . . . . . . . . . . . . . . . . . . . . . . . . . . . . . . . . . . . . . . . . . . . . . . . . . . . . 15-6
1.3.3 Power Board . . . . . . . . . . . . . . . . . . . . . . . . . . . . . . . . . . . . . . . . . . . . . . . . . . . . . . . . . . . . . . . . 15-6
1.3.4 Mother board . . . . . . . . . . . . . . . . . . . . . . . . . . . . . . . . . . . . . . . . . . . . . . . . . . . . . . . . . . . . . . . 15-7
1.3.5 PDM/PSM flex board. . . . . . . . . . . . . . . . . . . . . . . . . . . . . . . . . . . . . . . . . . . . . . . . . . . . . . . . . 15-7
1.3.6 Front panel flex board . . . . . . . . . . . . . . . . . . . . . . . . . . . . . . . . . . . . . . . . . . . . . . . . . . . . . . . 15-7
Functional check. . . . . . . . . . . . . . . . . . . . . . . . . . . . . . . . . . . . . . . . . . . . . . . . . . . . . . . . . . . . . . . . . . 15-10
3.3.1 Test setup. . . . . . . . . . . . . . . . . . . . . . . . . . . . . . . . . . . . . . . . . . . . . . . . . . . . . . . . . . . . . . . . . . 15-10
3.3.2 Module communication test . . . . . . . . . . . . . . . . . . . . . . . . . . . . . . . . . . . . . . . . . . . . . . . . 15-10
3.3.3 Synchronization connector test . . . . . . . . . . . . . . . . . . . . . . . . . . . . . . . . . . . . . . . . . . . . . 15-11
3.3.4 Test completion . . . . . . . . . . . . . . . . . . . . . . . . . . . . . . . . . . . . . . . . . . . . . . . . . . . . . . . . . . . . 15-13
Disassembling and reassembling
Disassembly and reassembly procedure . . . . . . . . . . . . . . . . . . . . . . . . . . . . . . . . . . . . . . . . . . . 15-21
6.2.1 7-module frame, F7 . . . . . . . . . . . . . . . . . . . . . . . . . . . . . . . . . . . . . . . . . . . . . . . . . . . . . . . . 15-21
6.2.2 5-module frame, F5 . . . . . . . . . . . . . . . . . . . . . . . . . . . . . . . . . . . . . . . . . . . . . . . . . . . . . . . . 15-24
Summary of Contents for E-PRESTN
Page 2: ......
Page 4: ...Module Frames and Modules 2062973 004 For your notes ...
Page 6: ...Module Frames and Modules 1 ii 2062973 004 ...
Page 10: ...Module Frames and Modules 1 4 2062973 004 For your notes ...
Page 11: ...2 Hemodynamic Modules E PRESTN E RESTN E PRETN Rev 00 E PSMP E PSM Rev 01 Technical Manual ...
Page 12: ......
Page 92: ...Module Frames and Modules 2 78 2062973 004 For your notes ...
Page 94: ...Module Frames and Modules 2 80 2062973 004 For your notes ...
Page 95: ...3 Continuous Cardiac Output Module E PiCCO Technical Manual ...
Page 96: ......
Page 124: ...Module Frames and Modules 3 26 2062973 004 For your notes ...
Page 126: ......
Page 159: ...Cardiac Output Modules E COPSv E COP 4 31 2062973 004 ...
Page 160: ...Module Frames and Modules 4 32 2062973 004 For your notes ...
Page 162: ...Module Frames and Modules 4 34 2062973 004 For your notes ...
Page 163: ...5 Dual Pressure Module E PP Pressure Temp Module E PT Pressure Module E P Technical Manual ...
Page 164: ......
Page 198: ...Module Frames and Modules 5 32 2062973 004 For your notes ...
Page 199: ...6 Masimo Module E MASIMO Technical Manual ...
Page 200: ......
Page 202: ...Module Frames and Modules 6 ii 2062973 004 ...
Page 218: ...Module Frames and Modules 6 16 2062973 004 For your notes ...
Page 220: ...Module Frames and Modules 6 18 2062973 004 For your notes ...
Page 221: ...7 Nellcor Compatible Module E NSAT E NSATX Technical Manual ...
Page 222: ......
Page 224: ...Module Frames and Modules 7 ii 2062973 004 ...
Page 236: ...Module Frames and Modules 7 12 2062973 004 ...
Page 244: ...Module Frames and Modules 7 20 2062973 004 For your notes ...
Page 246: ...Module Frames and Modules 7 22 2062973 004 For your notes ...
Page 247: ...8 Respiratory Modules E sCAiOVX E sCAiOV E sCAiO E sCOVX E sCOV E sCO Technical Manual ...
Page 248: ......
Page 284: ...Module Frames and Modules 8 34 2062973 004 ...
Page 316: ...Module Frames and Modules 8 66 2062973 004 For your notes ...
Page 319: ...9 Compact Airway Modules E CAiOVX E CAiOV E CAiO E COVX E COV E CO Technical Manual ...
Page 320: ......
Page 336: ...Module Frames and Modules 9 14 2062973 004 For your notes ...
Page 353: ...Compact Airway Modules E CAiOVX E CAiOV E CAiO E COVX E COV 9 31 2062973 004 ...
Page 379: ...Compact Airway Modules E CAiOVX E CAiOV E CAiO E COVX E COV 9 57 2062973 004 ...
Page 380: ...Module Frames and Modules 9 58 2062973 004 For your notes ...
Page 381: ...10 Single width Airway Module E miniC Technical Manual ...
Page 382: ......
Page 410: ...Module Frames and Modules 10 28 2062973 004 ...
Page 419: ...11 Entropy Module E ENTROPY Rev 01 Technical Manual ...
Page 420: ......
Page 442: ...Module Frames and Modules 11 20 2062973 004 For your notes ...
Page 443: ...12 EEG Module E EEG and EEG Headbox N EEG Technical Manual ...
Page 444: ......
Page 468: ...Module Frames and Modules 12 22 2062973 004 For your notes ...
Page 470: ...Module Frames and Modules 12 24 2062973 004 For your notes ...
Page 471: ...13 BIS Module E BIS Rev 01 Technical Manual ...
Page 472: ......
Page 494: ...Module Frames and Modules 13 20 2062973 004 For your notes ...
Page 495: ...14 NeuroMuscular Transmission Module E NMT Rev 01 Technical Manual ...
Page 496: ......
Page 518: ...Module Frames and Modules 14 20 2062973 004 For your notes ...
Page 520: ...Module Frames and Modules 14 22 2062973 004 For your notes ...
Page 521: ...15 F5 5 Module Frame F7 7 Module Frame Technical Manual ...
Page 522: ......
Page 558: ...Module Frames and Modules 15 34 2062973 004 For your notes ...
Page 560: ...Module Frames and Modules 15 36 2062973 004 For your notes ...
Page 561: ...16 Patient Data Module v2 Technical Manual ...
Page 562: ......
Page 620: ...Module Frames and Modules 16 56 2062973 004 ...
Page 621: ......