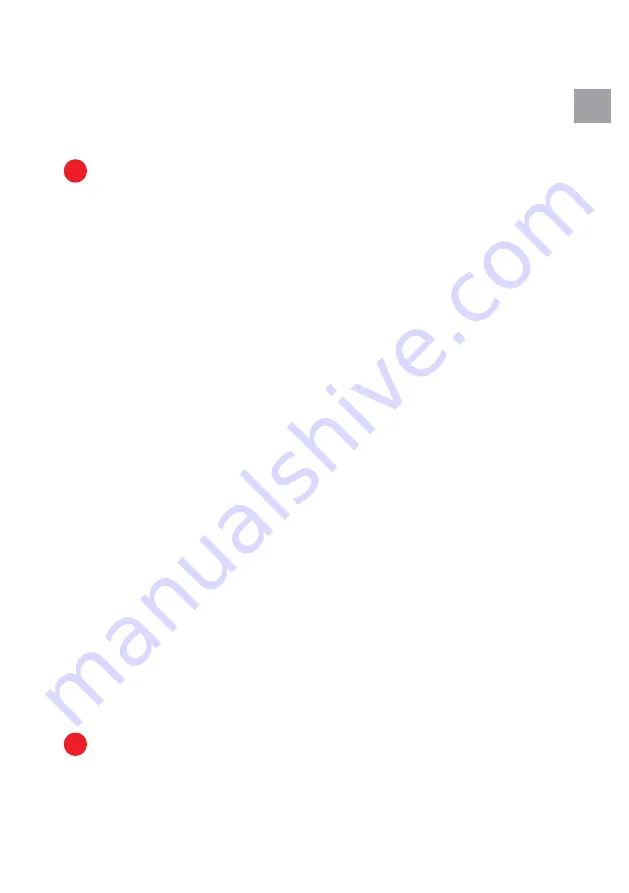
11/222
GB
Clutch lever
Fig.5: Machine description
3.
MaCHInE InSTaLLaTIon
Machine is delivered partly dismounted with cutting torch and arm parts separated. take all parts out of the
pack. install them in sequence as below to operate it.
3.1. Power suPPly
check power supply before connecting the machine to the network (see above the point 2.1. technical data).
only undamaged plug and cable can be connected to the power network. only the way of connection
conforming to national standards shall be used.
description of the colours of the power cable single wires:
•
brown: phase
•
blue: Neutral
•
green / Yellow: Earth
3.2. oxygen and fuel gas suPPly
3.2.1.
inlet fuel gas hose should be with 8mm internal diameter at least (depends on the hose length). only
hoses according to iso3821 / EN559 shall be used. Machine hose in let connection is g3/8”LH with fitting
acc. to EN560. For fuel gas pressure and flow-rate follow please cutting nozzles chart with all details above.
3.2.2.
Inlet oxygen hose should be with 6mm internal diameter (depends on the hose length and cutting
thickness). only hoses according to iso3821 / EN559 shall be used. Machine hose inlet connection is g1/4”
with fitting acc. to EN560. For oxygen pressure and flow-rate follow please cutting nozzles chart with all
details above (always the higher value should be taken from both heating and cutting oxygen).
note:
in order to prevent flashback (flame backfire) hazards, appropriate flashback arrestors should be
used specified in accessories below.
note:
only undamaged gas hoses with undamaged, clean and properly
fastened fittings shall be used. Tightness of the hoses shall be tested every three months at latest with using
of maximal working pneumatic pressure in water bath. it is recommended to exchange all gas hoses every
three years at latest.
3.3. InSTaLL CaBLE anD InTERnaL GaS HoSES
together e.g. with using of hose brace.
3.4. install cutting torch bar, cutting torch holder and CUTTInG ToRCH
as shown at the pic. 5 to 8 in accordance with requested cutting shape.
3.5. ConnECT InTERnaL HoSES To CUTTInG ToRCH anD GaS ManIFoLD.
as the hose connection of each gas hose is different, it’s not possible to mix them together.
3.6. insert the Power Plug of your machine
to a proper socket (use the type of connection according to national standard). connect inlet oxygen hose
and inlet fuel gas hose to proper supply system.
noTE
: install your machine to an earthed plug in order to
avoid electrical power hazards.
4.
oPERaTIon
4.1. BEFoRE STaRT CUTTInG
4.1.1.
the operator shall be aware of safety operation specified in this instruction for use before any handling
with gCE proFIT
®
. the operator shall be experienced with oxy-fuel equipment and trained according to
request of iso, EN or national standards with respecting all requests of legal authorities.
Summary of Contents for proFIT
Page 3: ......
Page 46: ...46 222 CZ...
Page 55: ...55 222 CZ ovl dac panel 240 v ov l dac panel 110 v ovl dac panel 240 v 240 v 110 v...
Page 56: ...56 222 Obr 13 Zm na nap t 240V 110V...
Page 106: ...106 222 ES...
Page 114: ...114 222 Fig 13 Cambio de voltaje 240V 110V 7 diagrama de la conexi n el ctrica...
Page 128: ...128 222 PT...
Page 166: ...166 222 RU...
Page 167: ...167 222 a 3 10 g1 4 g3 8 LH...
Page 172: ...172 222 11 1 2 3 6 7 M6x20 8 9 10 4 1 5 6 7 8 9 11 2 5 gcE proFIT 12 12 RU 240 10...
Page 173: ...173 222 5 5 1 gcE proFIT shell vitrea 31 5 2 5 3 RU 110 v 240 v 110...
Page 174: ...174 222 13 240 110 gcE proFIT...
Page 175: ...175 222 6 240 110 13 RU 7 8...
Page 176: ...176 222 9 9 1 gcE proFit 9 2 9 3 9 4 10 10 1 RU Bild 14 Exempel p inpackning...
Page 177: ...177 222 10 2 10 10 3 11...
Page 178: ...178 222 12 14 3 50 c 130 F en 730 1 en 560 14008408 g3 8 RU 13...
Page 179: ...179 222 14008263 g1 4 14008278 g3 8 LH RU...
Page 180: ...180 222 c...
Page 221: ......