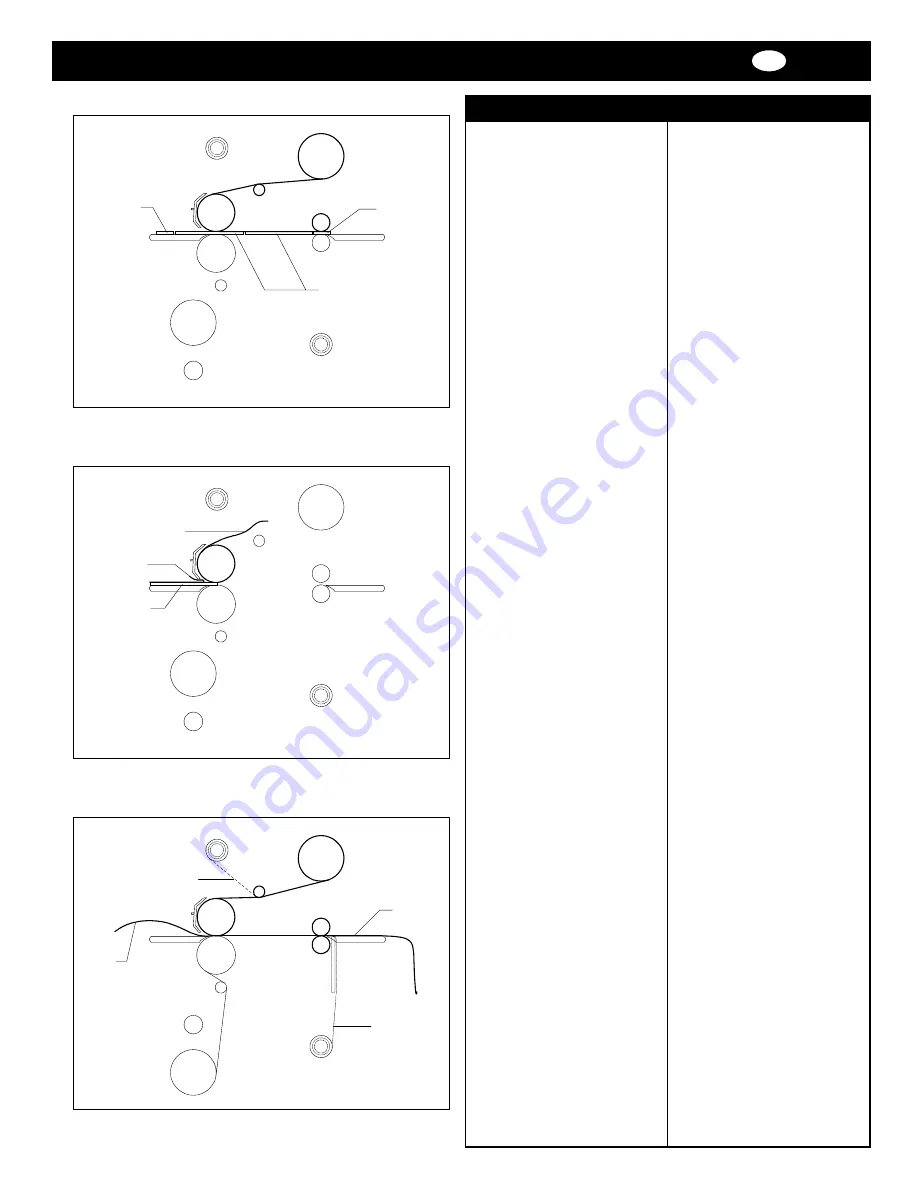
42
I
Fig. 34
Fig. 35
Fig. 36
TIPS FOR MOUNTING PRE-
COATED BOARDS (Figure 35)
1. This application can also be
performed from the rear
operating position. Reference
Figure 38 for illustration.
2. Use a leader board to set the
main roller pressure prior to
mounting the image.
3. Ensure the chill idler is removed
and the rear slitter is to one side.
4. Heat, 125
O
F (52
O
C), may assist
the process and increase output
quality.
5. Do not stop once you have
started the mounting process
through the machine.
TIPS FOR SINGLE SIDED
LAMINATION (Figure 36)
1. Load the laminator as illustrated
in Figure 36.
2. Use kraft paper for one-sided
lamination whenever the items to
be laminated are narrower than
the film you are using.
3. If not using kraft paper, use a
scrap piece to finish the run or
you will have adhesive on your
rollers.
4. For high volume runs, use Kraft
paper and the lower rear rewind
for roll to roll operation.
5. Running the web over the chill
idler may improve the flatness of
the output.
6. A little heat, 125
O
F (52
O
C), may
help eliminate silvering effects
associated with PSA films.
APPLICATIONS
TIPS FOR PRE COATING BOARDS
(Figure 34)
1. Load the laminator as illustrated
in Figure 34. Remove chill idler.
2. The width of the roll should not
exceed the width of the board
by more than 1/2 in. (1.3 cm).
3. Use a leader board to set the
main roller and pull roller
pressure prior to webbing.
4. Use a leader board to start the
run and a trailer board to finish
the run.
5. Using the pull rollers will allow
you to leave gaps between
boards.
6. If not using the pull rollers, have
the boards nearby to butt end to
end during feeding.
Mount
Adhesive
Leader board
Trailer board
Boards
Image
Pre-coated baord
Release liner
Thermal
or PSA
Film
Kraft
Paper
Option
Release liner from PSA film
Roll to roll option
Output
Image
Preliminary
Copy
Summary of Contents for Falcon 60+ (-1)
Page 2: ...2 Preliminary Copy...
Page 5: ...5 NL F E Preliminary Copy...
Page 7: ...7 NL F E Preliminary Copy...
Page 9: ...9 NL F E Preliminary Copy...
Page 11: ...11 NL F E Preliminary Copy...
Page 13: ...13 NL F E Preliminary Copy...
Page 15: ...15 D NL F E Preliminary Copy...
Page 17: ...17 D NL F E Preliminary Copy...
Page 19: ...19 D NL F E Preliminary Copy...
Page 21: ...21 D NL F E Preliminary Copy...
Page 23: ...23 D NL F E Preliminary Copy...
Page 25: ...25 D NL F E Preliminary Copy...
Page 27: ...27 D NL F E Preliminary Copy...
Page 29: ...29 D NL F E Preliminary Copy...
Page 31: ...31 D NL F E Preliminary Copy...
Page 33: ...33 D NL F E Preliminary Copy...
Page 35: ...35 D NL F E Preliminary Copy...
Page 37: ...37 D NL F E Preliminary Copy...
Page 39: ...39 D NL F E Preliminary Copy...
Page 41: ...41 D NL F E Preliminary Copy...
Page 43: ...43 D NL F E Preliminary Copy...
Page 45: ...45 D NL F E Preliminary Copy...
Page 47: ...47 D NL F E Preliminary Copy...
Page 51: ...51 NL F E Preliminary Copy...
Page 53: ...53 D NL F E Preliminary Copy...
Page 55: ...55 NL F E Preliminary Copy...
Page 57: ...57 I Preliminary Copy...
Page 58: ...58 D Preliminary Copy...
Page 59: ...59 NL Preliminary Copy...
Page 60: ...60 F Preliminary Copy...
Page 61: ...61 E Preliminary Copy...
Page 62: ...62 This page intentionally left blank Preliminary Copy...
Page 63: ...Preliminary Copy...
Page 64: ...General Binding Corporation One GBC Plaza Northbrook IL 60062 4195 Preliminary Copy...