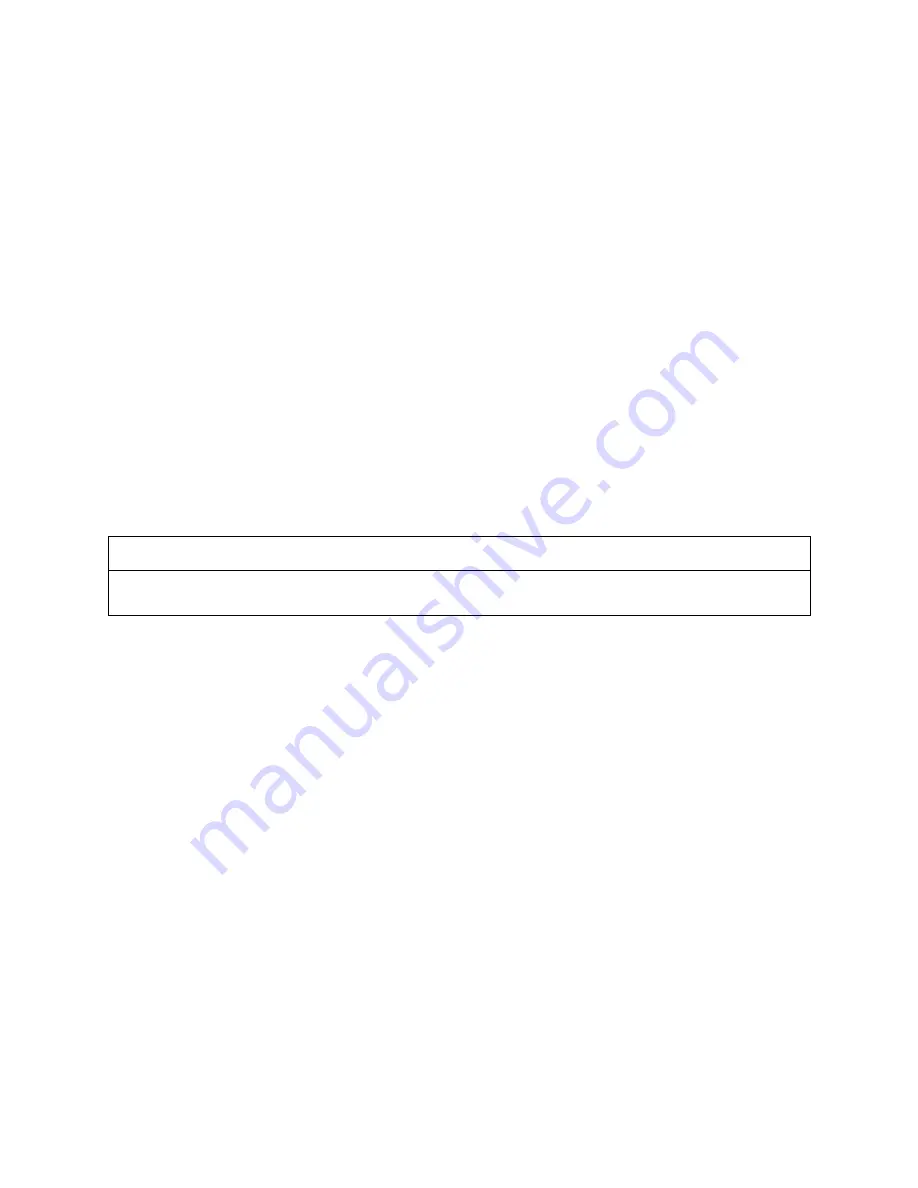
37-1-615 Page 13
Bypass Valve
– Installation of a bypass valve at the blower discharge (FIGURE 2-2) will allow the blower
to be started under no-load. Bypass line may be discharged at atmosphere or to blower inlet depending
on local requirements or material being handled.
Heat Exchanger
– When the bypass line discharges to blower inlet, a heat exchanger must be included
in the line between blower discharge and blower inlet, to remove the heat of compression before the gas
is reintroduced into the blower inlet. A check valve (FIGURE 2-2) should also be placed in the inlet line
between the bypass line and the inlet filter or silencer, to prevent discharging backwards through the filter
or silencer.
SAFETY DEVICES –
For all installations the following safety devices are a requirement for safe blower
operation. Numbers shown are reference numbers used in FIGURE 2-2.
7.
Check Valve, Blower Discharge Line
8.
Relief Valve, Vacuum or Pressure
12.
High Discharge Air Temperature Switch
Check Valve
(FIGURE 2-2)
– When the blower is used in a pneumatic conveying system, a check valve
must be used to prevent backflow of material into the blower. In any system it is a safety device
preventing the down stream pressure from motoring the blower through shutdown periods. A check valve
must be provided for each blower when several blowers are manifold into a common system.
Relief Valve
(FIGURE 2-2)
–The relief valve must be installed as close to blower ports as possible.
There should be no accessories such as valves, check valves, silencers, etc. between the relief valve and
blower ports. It should be set 2 to 3 PSI above normal blower operating pressure (1/2
” to 1” Hg. In
vacuum service), but not to exceed 2 PSI above maximum differential pressure rating of the blower for
pressure service.
NOTICE
Relief valves should be placed as close as possible to the blower inlet port (vacuum operation)
or discharge port (pressure operation).
High Temperature and High Pressure Shutdown
– All blower installations should be protected with a
high temperature shutdown switch. The controls should be set to stop the blower when the discharge
temperature reaches 355°F or temperature rise reaches 255°F. In some installations a high pressure
shutdown switch may also be advisable. The sensing element of these controls should be installed as
close to the blower discharge as possible. See FIGURE 2-2. On remote or unattended installations
these controls are normally mandatory.
INLET PIPING
– During the installation of piping make sure dirt and other foreign materials do not enter
blower openings. When inlet piping is used IT MUST BE CLEAN, AND FREE OF SCALE AND OTHER
FOREIGN MATERIALS WHICH COULD ENTER THE BLOWER. It is suggested that an expansion joint
be installed near blower openings to prevent stressing of the blower housing. Support the pipe to relieve
weight on the expansion joint and the blower. Make sure the pipe size is adequate and as straight as
possible to prevent pressure drop at the blower inlet. Where bends are necessary use long radius
fittings. All connections must be air tight.
For vacuum service, an accurate vacuum gauge must be used near the blower inlet to indicate operating
vacuum and a suitable vacuum relief valve must be used. A vacuum blower in pneumatic conveying
service requires pre-inlet separation and filtering to prevent material carry-over into the blower.
Inlet pipe size is determined as follows:
0 to 10 feet long, use pipe size equal to blower inlet flange size.
10 to 17 feet long, use pipe size larger than blower inlet.
17 to 33 feet long, two pipe sizes larger than blower inlet.